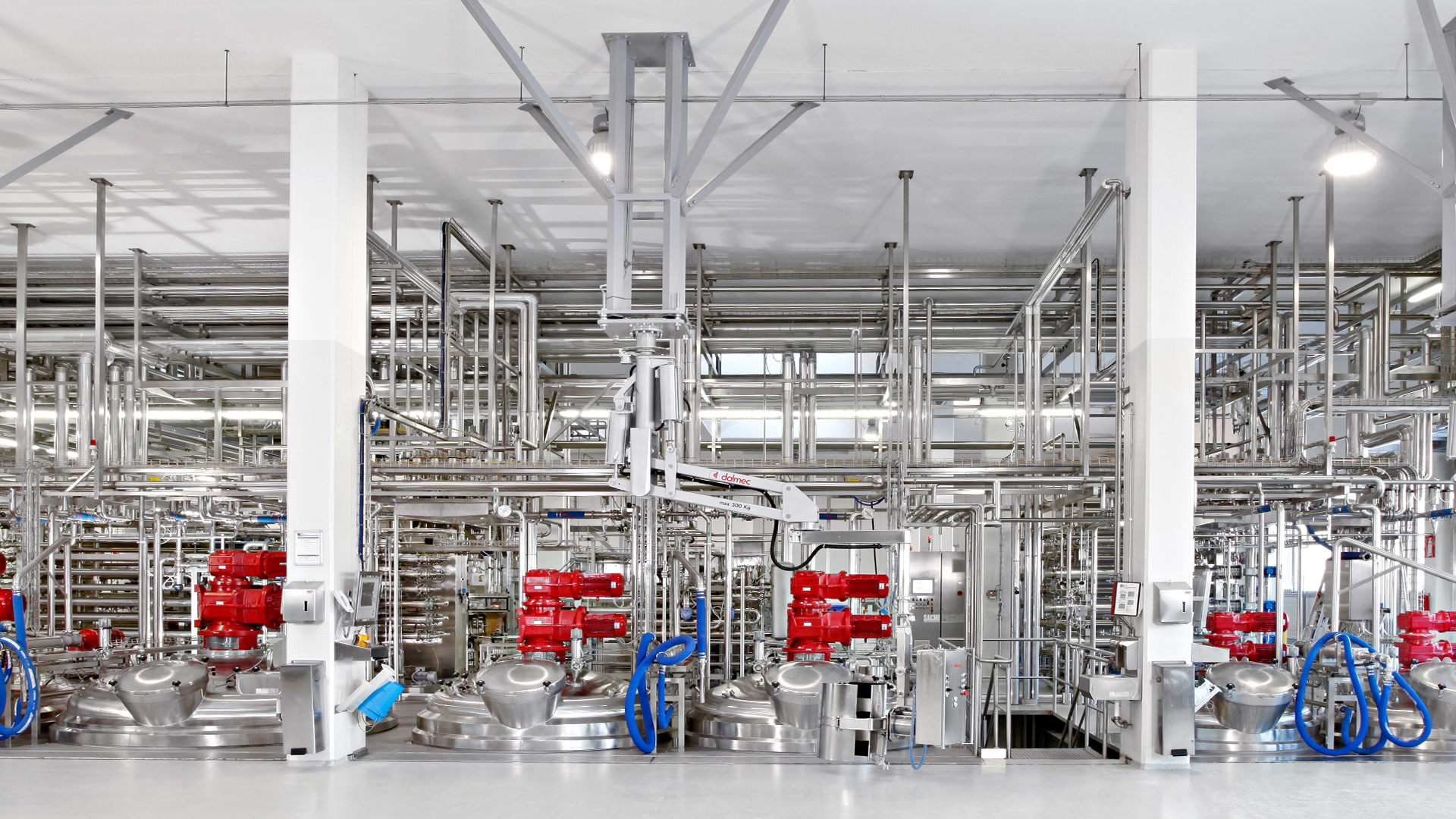
Raport dotyczący projektu
Instalacja procesowa do przetwarzania i rafinacji owoców
Iprona AG
Wyposażenie nowego zakładu produkcyjnego w instalacje procesowe do przetwarzania i rafinacji owoców
Dla firmy IpronaAG, Ruland zrealizował projekt pod nazwą "wyposażenie nowo wybudowanego zakładu w systemy procesowe". Ten projekt został zrealizowany w dwóch etapach: konsulting i realizacja.
Konsulting
Po wielu latach dynamicznego rozwoju firmy, w 2005 roku rozpoczęła się budowa nowego zakładu produkcyjnego w miejscowości Lana, we Włoszech. W celu określenia optymalnego przebiegu działań nakierowanych na realizację projektu, nasz klient zdecydował się skorzystać z naszych usług konsultingowych. Etap pierwszy obejmował planowanie ogólnej koncepcji, która miała stanowić podstawę do opracowania koncepcji szczegółowej/projektu technicznego w etapie drugim. Nasze prace rozpoczęliśmy od zarejestrowania aktualnych metod produkcji i opracowania schematu blokowego, który przedstawia kompletny przepływ materiałów, począwszy od odbioru/magazynowania surowców aż do linii produkcyjnych gotowych produktów. Zbieranie informacji na temat aktualnej sytuacji oraz rozmowy na temat szczegółów odbywały się od samego początku przy współudziale zespołu projektowego firmy Iprona. W skład zespołu wchodzili kierownicy zakładu/projektu oraz pracownicy działu technicznego, zapewnienia jakości, działu informatycznego i wydziału produkcyjnego. Włączenie pracowników produkcji do zespołu okazało się szczególnie ważnym posunięciem, ze względu na możliwość wykorzystania ich ogromnej wiedzy. Ponadto, pracownicy ci uczestniczyli w projektowaniu nowych procesów/technologii i opracowywaniu nowych koncepcji działania i, dzięki temu, będą posiadali pełną wiedzę na temat planowanych innowacji. Z naszej strony, w pracach zespołu konsultingowego uczestniczyli: główny konsultant, inżynier projektu oraz dodatkowi inżynierowie, specjaliści z zakresu projektowania rurociągów i automatyzacji.
Szczegółowe planowanie
Bazując na schemacie blokowym, zespół ten stopniowo opracował schematy technologiczne dla każdego obszaru. Te schematy technologiczne zostały następnie dopracowane w toku dalszych, szczegółowych rozmów z firmą IpronaAG. Celem działań prowadzonych podczas tego etapu planowania był prawidłowo zdefiniowany opis procesów, a nie określenie parametrów poszczególnych komponentów instalacji (szerokość, producent, itd.). Dla obszarów wspólnych, opracowano, zaprezentowano, przedyskutowano, zweryfikowano i wybrano różne koncepcje działania/automatyzacji. Stosując takie podejście, w przypadku obszaru zbiornika magazynowego na sok zarzucono początkowo preferowaną koncepcję zespołu zaworowego na rzecz złożonego, lecz nadal łatwego w obsłudze, rozwiązania wykorzystującego układ rurociągów pionowych. Już na tym wczesnym etapie zastosowaliśmy nasze narzędzia 3D CAD do prezentowania omawianych kwestii, co okazało się bardzo przydatne. W szczególności, użytkownicy przyszłych instalacji bardzo docenili uwzględnienie ich procedur w szczegółowych planach. Częścią zakresu naszych usług konsultingowych było podstawowe, dwuwymiarowe planowanie układu rurociągów. Plany wykonano dla wszystkich mediów, aby zapobiec kolizjom rurociągów. Końcowym elementem planowania ogólnego było opracowanie oferty dla planowanego zakresu prac. Na tym etapie prac konsultingowych, zamówienie na realizację projektu zostało przyznane firmie Ruland.
Proces produkcyjny
Firma Iprona AG przetwarza świeże owoce i owoce mrożone, które są najpierw przetwarzane w celu uzyskania tak zwanego „soku macierzystego”. Owoce są wyciskane, a następnie przetwarzane w kolejnych etapach procesu w celu uzyskania klarownych lub naturalnie mętnych soków, które są potem podgrzewane przez krótki czas i przechowywane w sterylnych zbiornikach o pojemności 30 m³. Asortyment przetwarzanych owoców jest całkiem zróżnicowany, począwszy od melonów miodowych i jagód leśnych poprzez truskawki, jeżyny, porzeczki, itp. aż do kwiatów dzikiego bzu. Sok macierzysty może być zagęszczany w dwóch różnych instalacjach. Stosowana jest instalacja zagęszczania termicznego jak również instalacja zagęszczania na zimno. Na liniach gotowych produktów, główne produkty, takie jak pulpa owocowa, puree owocowe i koncentraty soków, z kawałkami owoców i składników lub bez, mogą być mieszane według indywidualnych wymagań klienta w zbiornikach do mieszania o różnych wielkościach, pasteryzowane w różnorodnych wymiennikach ciepła i rozlewane aseptycznie.
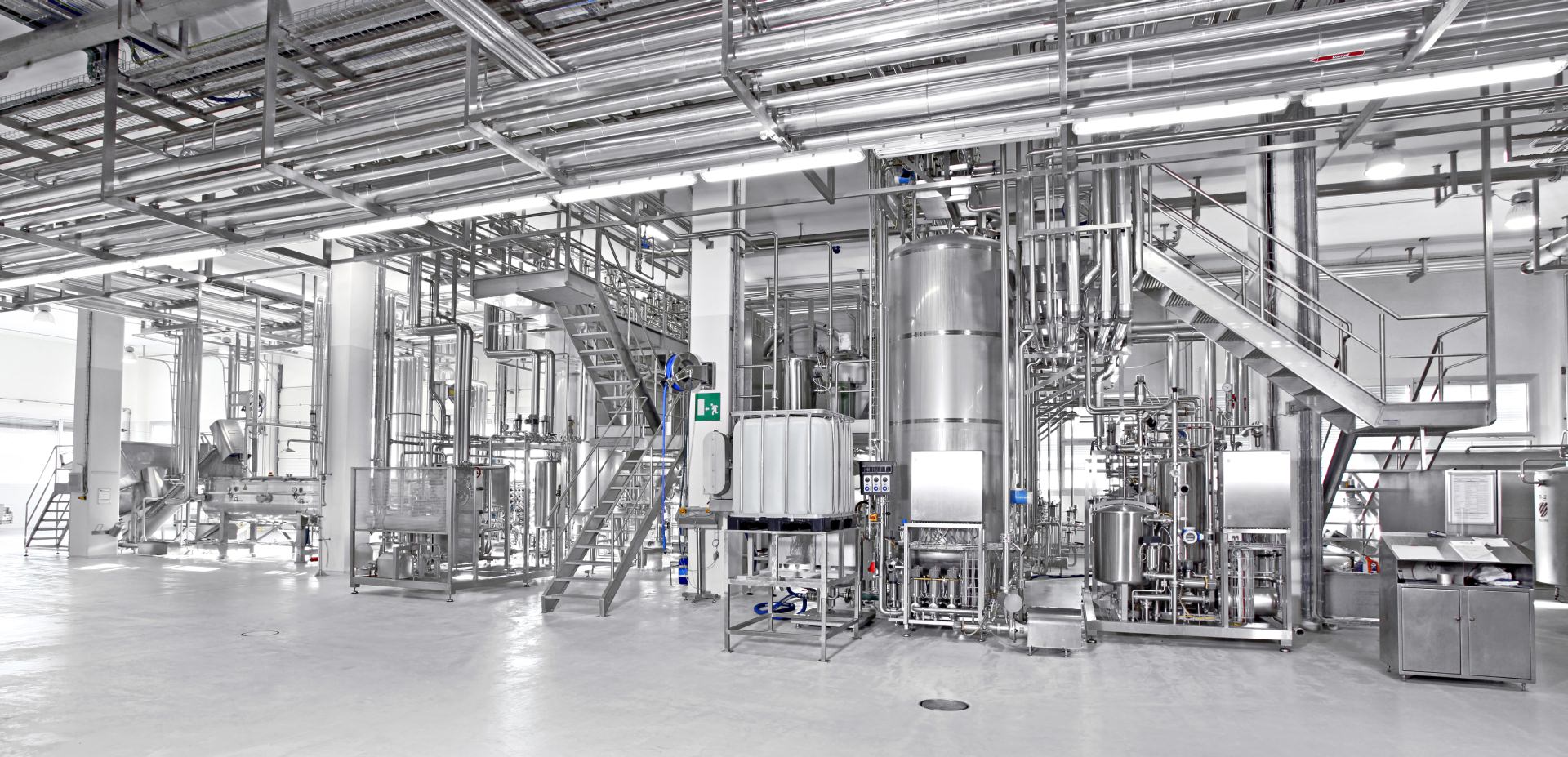
Realizacja
Firma Ruland była odpowiedzialna za wszystkie obszary produkcyjne: począwszy od wytwarzania soku, poprzez system zbiorników na soki, włączenie do projektu istniejących instalacji zagęszczania, aż do linii gotowych produktów i zapewnienia procesu czyszczenia na miejscu (CIP) dla wszystkich instalacji. W celu zapewnienia ergonomicznej wysokości roboczej, zbiorniki do mieszania zostały obniżone do poziomu piętra pośredniego. Zastosowanie mieszadeł współosiowych w zbiornikach do mieszania zapewnia przygotowanie homogenicznej porcji materiału dla procesów ciągłej pasteryzacji. Aby zapewnić maksymalną elastyczność, w zależności od wielkości partii i wymagań dla danego produktu, w procesie można zastosować płytowe lub skrobakowe wymienniki ciepła. Niezależnie od tego, jaki typ wymiennika jest wybrany, uzyskany ciąg technologiczny jest szczelny, co umożliwia prowadzenie innej produkcji lub czyszczenia w równoległych lub poprzecznych ciągach technologicznych. Ta elastyczność jest również widoczna w przypadku napełniania opakowań typu bag-in-box, bag-in-drum lub transportowych pojemników ze stali nierdzewnej przy użyciu sterylnych zespołów zaworowych. W obrębie pojedynczej partii produktu, przejście na inny system napełniania można wykonać bez wysiłku. Dla potrzeb czyszczenia instalacji produkcyjnych, firma Ruland wybudowała dwie centralne stacje CIP. Linie gotowego produktu i wytwarzania soku są tym samym dokładnie rozdzielone, co eliminuje zanieczyszczenie krzyżowe. Takie rozwiązanie spełnia wysokie wymagania jakościowe firmy Iprona AG. Przy użyciu matrycy, 13 kompletnych obwodów czyszczenia rozprowadzono w taki sposób, że pokrywanie się poszczególnych obszarów ograniczono do minimum i zapewniono maksymalną wydajność produkcji. Najbardziej ekonomicznym rozwiązaniem w tym obszarze było ponowne użycie istniejących zbiorników, poprzez wymianę osprzętu, w celu ich wykorzystania w instalacji CIP. Oprócz prac wykonanych w tych obszarach, firma Ruland wdrożyła koncepcję wykorzystania energii z pary wodnej pochodzącej z instalacji zagęszczania termicznego.
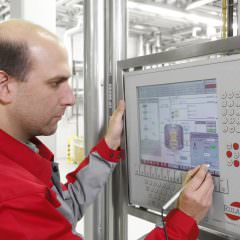
Sterowanie systemem
Aby umożliwić zunifikowaną kontrolę i obsługę skomplikowanych procesów, firma Ruland zaleciła zastosowanie systemu sterowania. W firmie Iprona, zastosowano system PCS7 opracowany przez Siemensa w połączeniu z systemem MES opracowanym przez firmę Ruland, który sprzęga komputery z systemem Ipronas ERP. Wszystkie konieczne dane są importowane z systemu ERP, przekształcane na receptury produkcyjne przez system MES, a następnie wprowadzane do układu sterowania procesem, wraz z odpowiednimi parametrami dotyczącymi produkcji i czyszczenia, które są opracowywane indywidualnie dla różnych produktów i zapisane w różnorodnych recepturach. Ponadto, wszystkie komponenty pochodzące od podwykonawców, posiadające indywidualny system automatyki, są zintegrowane z układem sterowania za pomocą wspólnego interfejsu opracowanego przez firmę Ruland. Dzięki zastosowaniu tej koncepcji, operator instalacji może jednocześnie obsługiwać i nadzorować działanie wszystkich zespołów instalacji. W ten sposób wyeliminowano odizolowane układy automatyki, różniące się konstrukcją i działaniem, które wymagają ciągłych zmian sposobu myślenia operatora. Takie odizolowane układy całkowicie wyeliminowano z całej instalacji. Ponieważ system stworzony przez firmę Ruland składa się z bloków odpowiedzialnych za sterowanie procesem, zarządzanie recepturami i zamówieniami oraz identyfikowalność partii produktu, zawsze możliwe jest odtworzenie przebiegu procesu produkcyjnego w przejrzysty sposób, od poziomu operatorów aż do poziomu kierownictwa firmy, oraz uwidocznienie rzeczywistej wydajności instalacji produkcyjnej. Począwszy od zarządzania zamówieniami i identyfikowania partii produktu z poziomu sterowni aż do praktycznego działania czujników i aktuatorów, stworzono zunifikowany system automatyzacji – pochodzący z jednego źródła.
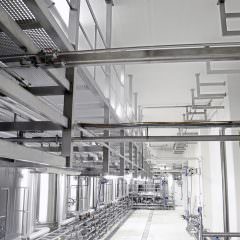
Na pięciu poziomach budynku zainstalowano ponad 50 km przewodów rurowych. Ze względu na tę skomplikowaną sytuację przestrzenną, opracowano trójwymiarowy projekt całego przedsięwzięcia. Taki projekt oraz wczesny i stały monitoring prac instalacyjnych prowadzony przez naszych inżynierów projektu umożliwił zoptymalizowanie instalacji rurociągowej pod kątem inżynierii procesu produkcyjnego oraz strat produktu. Dzięki bardzo intensywnej komunikacji i konstruktywnej współpracy pomiędzy zespołem projektowym i osobami odpowiedzialnymi w firmach Iprona i Ruland, zrealizowaliśmy bardzo duży i skomplikowany projekt w wyjątkowo efektywny i udany sposób.
Z przyjemnością doradzimy Ci osobiście.
Czekamy na wyzwanie!