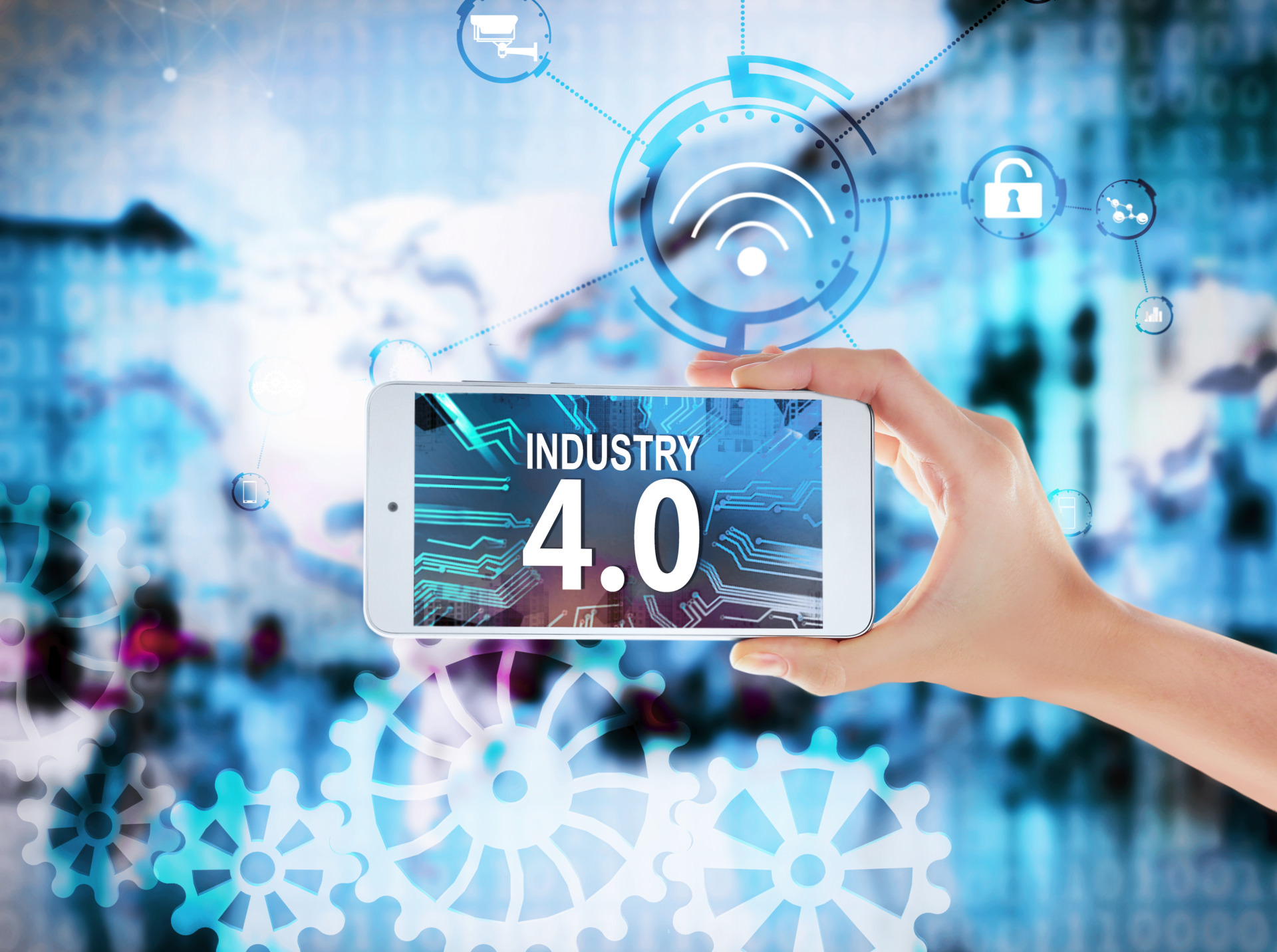
Jak Ruland realizuje założenia Przemysłu 4.0?
Czym jest czwarta rewolucja przemysłowai dlaczego Ruland podąża za wytyczonymi przez nią trendami?
Pojęcie Przemysłu 4.0 pojawiło się po raz pierwszy w 2011 roku podczas targów Hanover Messe, a za sam początek rewolucji uznawany jest rok 2013, kiedy to w Niemczech opublikowany został raport, określający założenia nowej koncepcji rozwoju dla tamtejszej gospodarki. Z perspektywy czasu jest to zjawisko stosunkowo młode, które jednak, na przestrzeni tych zaledwie kilku lat, zasadniczo zrewolucjonizowało świat produkcji przemysłowej. Postępujący rozwój nowych technologii w postaci chmur obliczeniowych, wielkich baz danych, Internetu rzeczy i sztucznej inteligencji współpracującej z człowiekiem, to w obecnych czasach nieuchronna konieczność każdego przedsiębiorstwa nastawionego na sukces. Dziejąca się na naszych oczach czwarta rewolucja to
odpowiedź na zindywidualizowane potrzeby współczesnego Klienta oraz wszechobecny trend personalizacji produktów i usług. Produkowane przez nas instalacje procesowe dedykowane wszelkiego rodzaju płynom, dostarczane są do dużych zakładów produkcyjnych, które w obliczu czwartej rewolucji stawiają na daleko posuniętą automatyzacje i cyfryzację procesu produkcyjnego. Ruland stara się podążać za obecnymi trendami i wprowadzać nowoczesne rozwiązania wpisujące się w ideę Industry 4.0. Mamy pełną świadomość, że tylko inwestowanie w innowacyjność i bycie na bieżąco, a nawet krok do przodu w temacie nowoczesnych technologii, pozwoli nam na pełną konkurencyjność i zainteresowanie ze strony naszych Klientów.
Jakie rozwiązania z obszaru Przemysłu 4.0 proponuje Ruland?
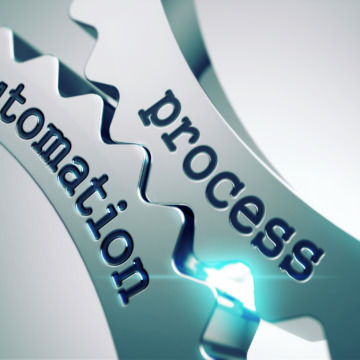
W zakresie automatyzacji urządzeń
Ruland dostarcza nie tylko kompletne instalacje procesowe, ale zapewnia również dostosowaną do indywidualnych potrzeb automatykę i rozwiązania IT. Obecnie zdecydowana większość naszych urządzeń jest w pełni zautomatyzowanych. W naszych układach wykorzystujemy systemy sterowania bazujące przede wszystkim na nowoczesnych rozwiązaniach firmy Siemens. Stosujemy sterowniki programowalne serii 1500,1200 oraz starsze 300 i 400. Nasz autorski System Zarządzania Procesem (PMS) należy do najnowocześniejszych systemów automatyzacji urządzeń procesowych. System obejmuje wiele maszyn i planuje zlecenia produkcyjne niezależnie na wielu liniach produkcyjnych i urządzeniach. Analizę prowadzonych procesów wspomagają wartościowe raporty zawierające niezbędne dane procesowe.
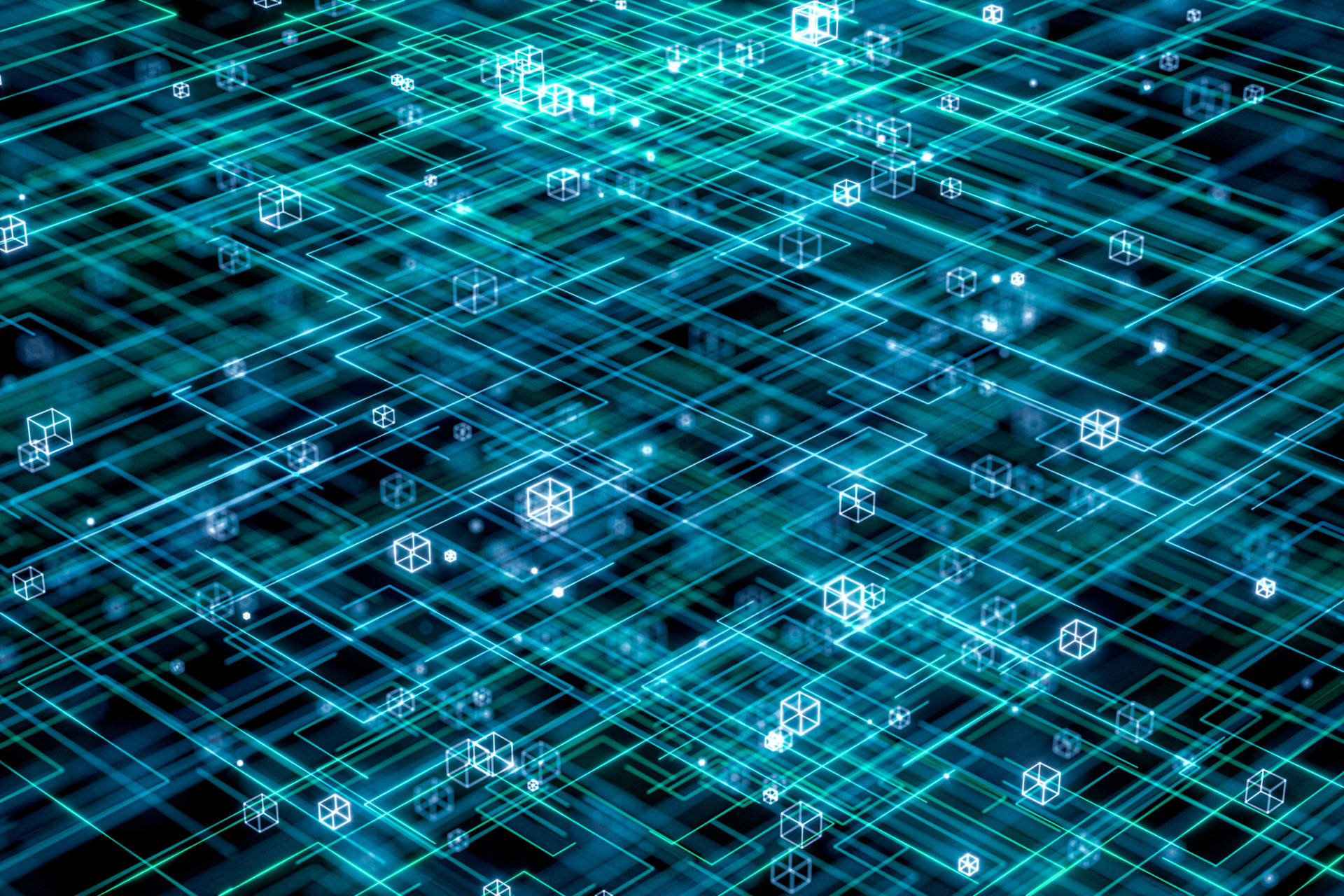
W zakresie sieci przemysłowych
Często budowane instalacje procesowe są bardzo rozległe i zawierają wiele rozporoszonych wejść oraz wyjść. W takim wypadku, do połączenia poszczególnych komponentów z układem sterującym stosujemy sieci przemysłowe. Niezawodna sieć przemysłowa to nieodłączny element współczesnych systemów sterowania, których celem jest zoptymalizowanie procesów produkcyjnych. Tworzone przez nas sieci przemysłowe umożliwiają pełną automatyzację zakładu, poprawiając efektywność komunikacji pomiędzy poszczególnymi urządzeniami oraz całymi liniami produkcyjnymi. W swoich projektach najczęściej stosujemy sieci Profinet oraz AS-i. Coraz większą popularność zdobywa również sieć IO-Link.
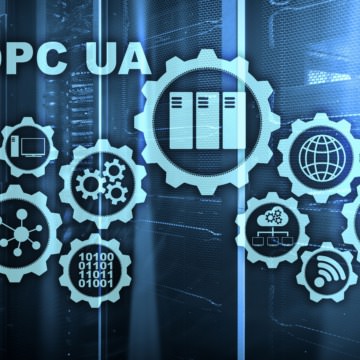
W zakresie nowoczesnej komunikacji przemysłowej
Jednym z trendów Przemysłu 4.0 jest wszechobecna komunikacja pomiędzy urządzeniami i systemami. Często jest to komunikacja pomiędzy systemami różnych producentów. Z pomocą przychodzi tu technologia OPC, która pozwala na zbieranie danych z wielu różnych źródeł (np. różnych sterowników PLC) i udostępnianie tych danych aplikacjom i bazom danych za pomocą ujednoliconych interfejsów. Ruland wykorzystuje rozwiązania serwerów OPC dostarczanych przez jednego z wiodących producentów tego typu oprogramowania – firmę Kepware. Serwery OPC integrują w systemach automatyki różne urządzenia i systemy, umożliwiając optymalną komunikację, będącą warunkiem sprawnego zarządzania całością procesu produkcyjnego.
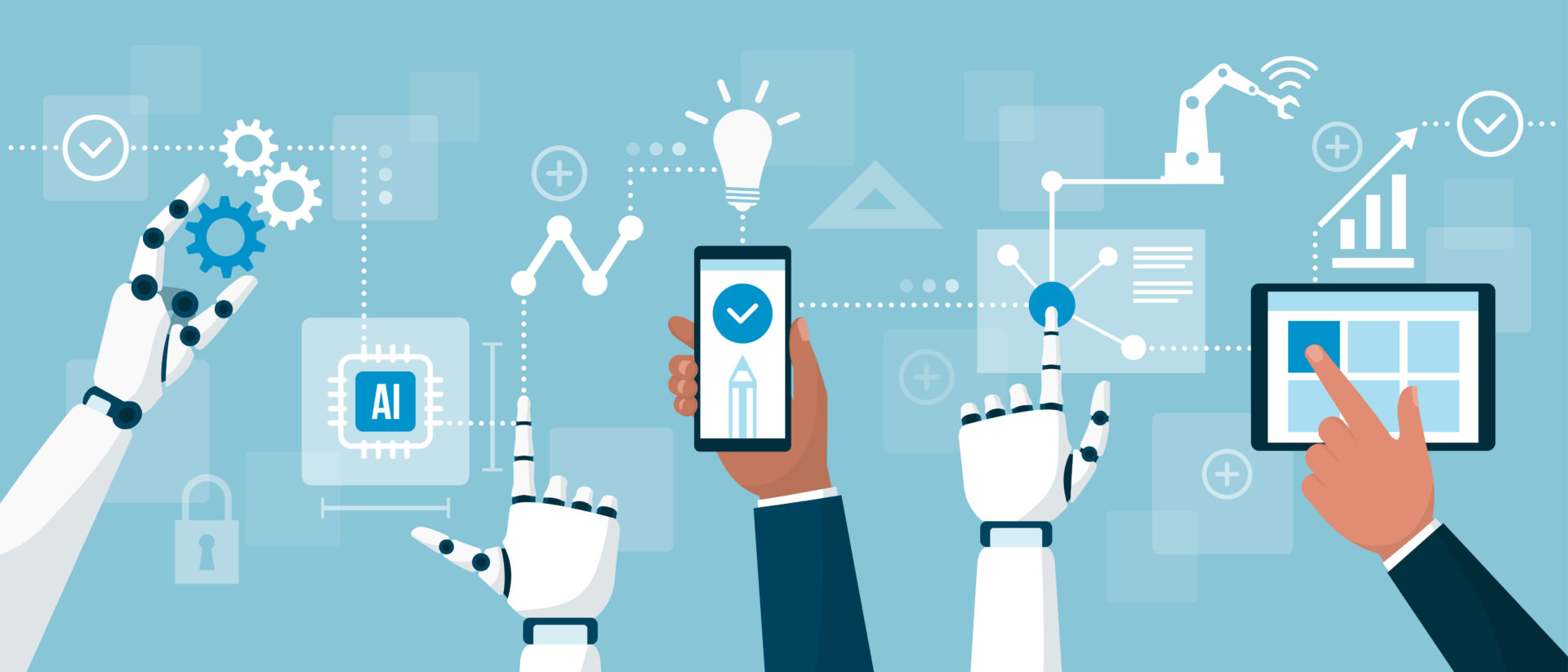
W zakresie kontroli procesów produkcyjnych
Dobór systemu uzależniony jest od wymogów procesowych. W instalacjach mniej skomplikowanych technologicznie, do obsługi urządzeń stosujemy panele operatorskie HMI, a w tych bardziej rozbudowanych i zaawansowanych systemy SCADA. Panele HMI są wykorzystywane do komunikacji z pojedynczymi urządzeniami i mniejszymi liniami technologicznymi. Systemy SCADA natomiast są oparte na komputerach PC, posiadają rozbudowaną funkcjonalność, pozwalają na stworzenie architektury klient-serwer, redundancję czy wirtualizację. Wykorzystywane przez nas systemy SCADA umożliwiają Klientowi wgląd w cały proces produkcyjny w czasie rzeczywistym. Dzięki takim rozwiązaniom operatorzy monitorują na bieżąco działanie naszych urządzeń, co pozwala na szybką reakcję i eliminowanie sytuacji negatywnie wpływających na procesy produkcyjne – zmniejszenie wydajności czy też przestoje produkcyjne.
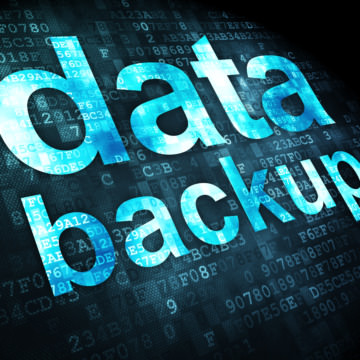
W zakresie rozwiązań autorskich
Gdy potrzebna jest dodatkowa funkcjonalność, stosujemy rozwiązania autorskie. Systemy SCADA udostępniają pewne środowisko programistyczne i dają znaczne możliwości. Często jednak trzeba sięgnąć po dodatkowe narzędzia, by stworzyć produkt kompatybilny z instalacją i jak najlepiej dopasowany do wymagań Klienta. W naszej firmie wykorzystujemy w tym celu oprogramowanie Visual Studio, które daje możliwość tworzenia autorskich aplikacji obejmujących systemy recepturowe i raportujące. Z każdego procesu może zostać wygenerowany szczegółowy raport pozwalający stwierdzić, czy proces odbywa się zgodnie z założeniami.
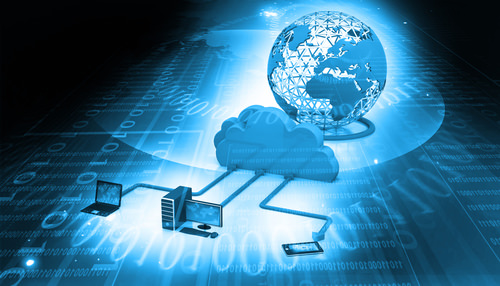
W zakresie zdalnego dostępu i serwisu
Zdalny dostęp do naszych urządzeń to rozwiązanie stosowane przez nas na długo przed globalną pandemią. Ta jednak, przez ograniczenie dostępu do zakładów produkcyjnych, pokazała skuteczność i niezawodność tego narzędzia. Każda z naszych instalacji jest wyposażona w moduły zdalnego dostępu VPN. Najczęściej wykorzystujemy przemysłowe routery VPN marki EWON. Są one częścią kompletnej platformy do zarządzania połączeniami, użytkownikami wraz z raportami ze wszystkich wykonanych połączeń. Czasem wymagane są jednak inne rozwiązania dla ustanowienia łączności VPN. Tak więc każdorazowo uzgadniamy sposób zdalnego dostępu z działem IT naszego Klienta. Zdalny dostęp daje możliwość serwisowania instalacji bez konieczności opuszczania biura przez naszych specjalistów, co przekłada się na optymalizację kosztów naprawy ewentualnych usterek.
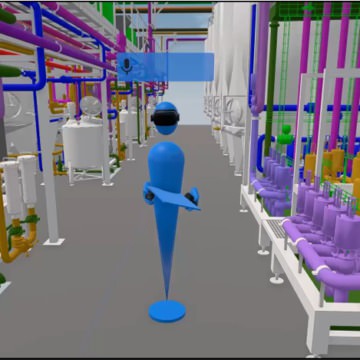
W zakresie rzeczywistości rozszerzonej
Globalna pandemia postawiła przed nami zupełnie nowe wyzwania, zmuszając do szukania rozwiązań w kwestii spotkań z Klientami. Z czasem, telekonferencje, tak spopularyzowane w czasach lockdownów, przestały nam wystarczać, dlatego poszliśmy o krok dalej, stawiając na technologie VR z wykorzystaniem gogli OCULUS. To nowoczesne narzędzie pozwoliło nam na zaaranżowanie wirtualnych spotkań z Klientem niejako wewnątrz układu przedstawionego w formie 3D. Gogle 3D dają poczucie pełnej immersji, nasze postacie-awatary są proporcjonalnie odwzorowane w wirtualnej rzeczywistości. Możliwy staje się wirtualny spacer i sprawdzenie czy instalacja będzie wygodna dla obsługi przez operatora. Można nawet zajrzeć do wnętrza zbiorników…
Cały czas przy tym, utrzymujemy również połączenie głosowe ze wszystkimi „awatarami”. Używając okularów rzeczywistości rozszerzonej lub w prostszym przypadku smarftona, możemy skorzystać z rozwiązania oferowanego przez firmę TeamViewer w przypadku nagłych problemów na instalacji. Serwisant łączy się z biura z klientem, który odbiera połączenie w aplikacji na smartfonie lub w okularach AR. Na obrazie transmitowanym z kamery smartfona/okularów serwisant lub Klient umieszcza znaczniki, które zostają „zakotwiczone” w przestrzeni. Można w ten sposób wskazać, z którym elementem instalacji jest problem i następnie próbować go rozwiązać.
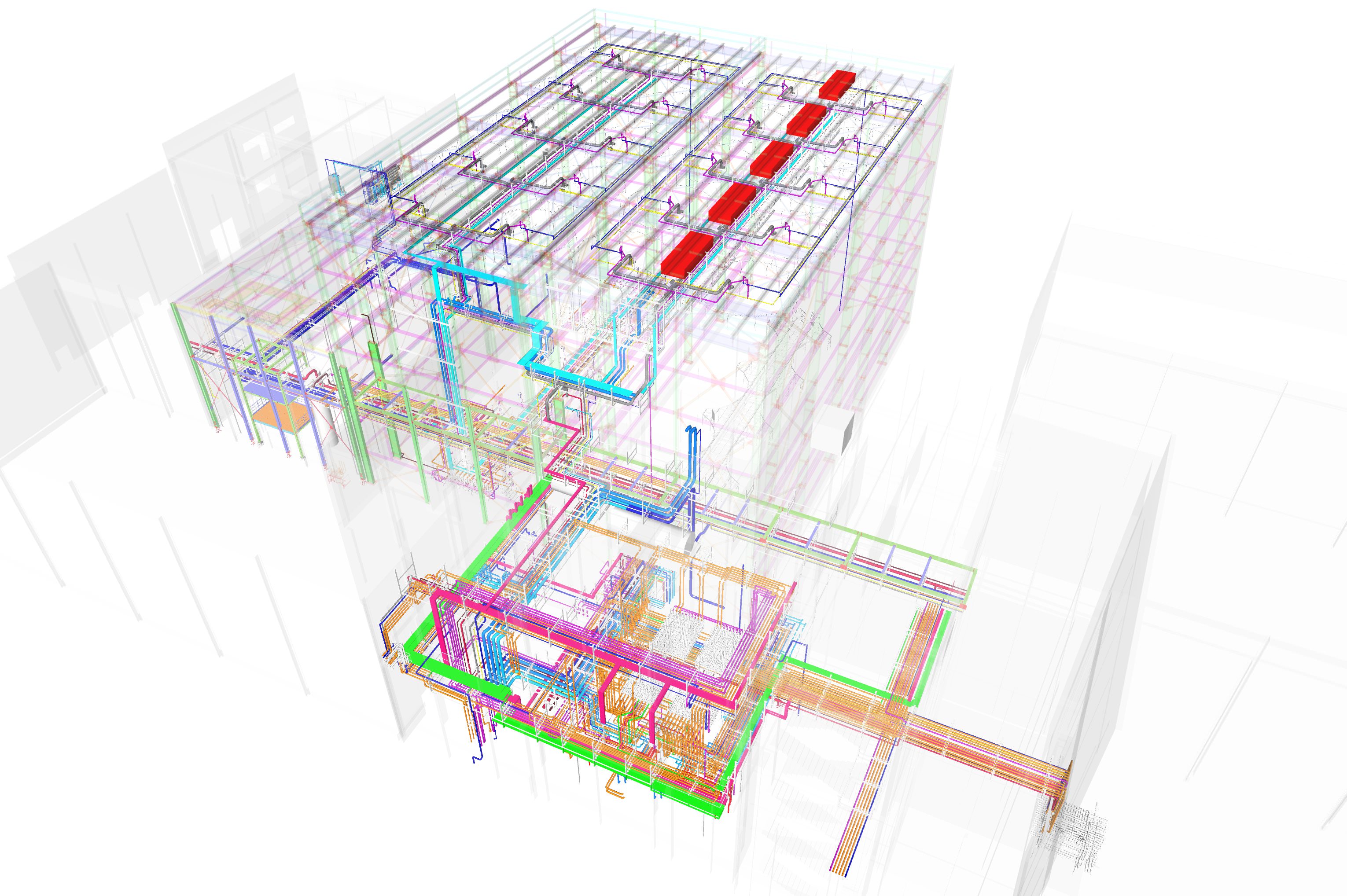
W zakresie korzystania z nowoczesnych rozwiązań pomiarowych w technologii 3D
Jednym z etapów realizacji naszych projektów jest wizja lokalna u Klienta i dokonanie pomiarów w hali produkcyjnej, w której mają zostać umieszczone urządzenia. Zwykle zadanie to należy do jednego z inżynierów zaangażowanych w projekt. Niestety w ostatnim roku możliwość wyjazdów została znacznie ograniczona, a my stanęliśmy przed koniecznością znalezienia odpowiedniego rozwiązania. Z pomocą przyszła technologia skanowania 3D, którą wykorzystaliśmy podczas realizacji jednego z projektów dla Klienta w Rosji. Ta innowacyjna technologia pomiarowa pozwala zebrać dane przestrzenne za pomocą skanera 3D, a następnie przy użyciu oprogramowania Autodesk ReCAP zweryfikować istniejące warunki, dokonać pomiarów i podjąć dalsze decyzje odnośnie rozmieszczenia urządzeń i tras rurociągowych.