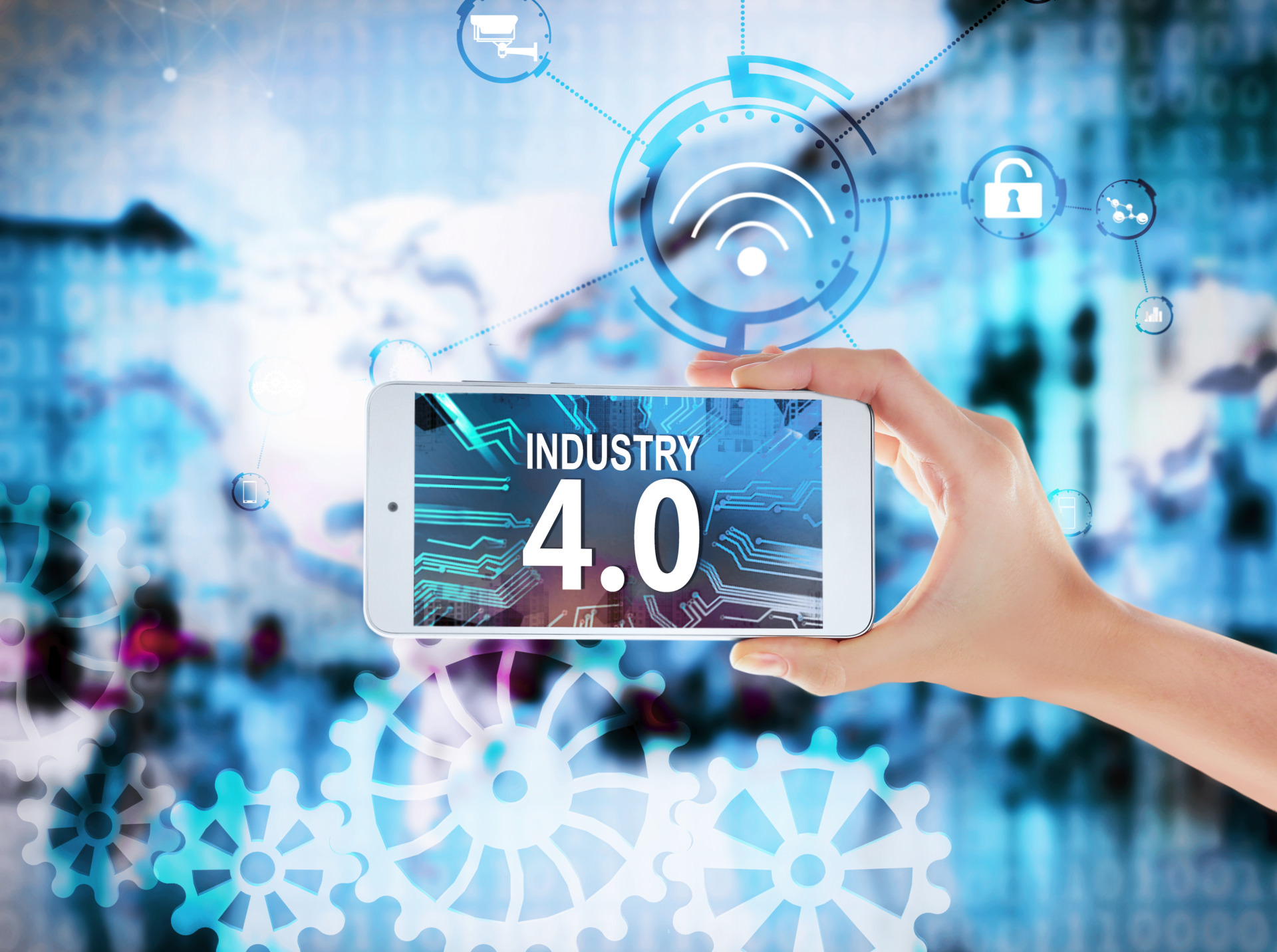
Automation of industrial plants
Implementation of Industry 4.0 solutions in individual plant engineering
The automation of industrial plants made its way into manufacturing companies with the digital revolution in the 1970s. In 2011, at the Hannover Messe, the industry spoke for the first time about the next industrial revolution, Industry 4.0. The progressive development of new technologies in the form of cloud computing, large databases, the Internet of Things and artificial intelligence is now considered a necessity for every successful company. Industry 4.0 (ioT) is considered the answer to the individualised needs of a modern customer and the omnipresent trend towards personalisation of products and services. Ruland supports the automation and digitalisation of production processes with its systems for liquid products.
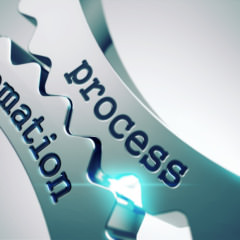
The plant automation
Automation systems and control cabinet construction as basis for Industry 4.0
To complement our process plants, we supply customised automation and IT solutions. Today, most of our plants are fully automated. Our control and visualisation systems are mainly based on modern solutions from Siemens, Rockwell and Aveva. All Ruland plants are modularly constructed and equipped with decentralised control cabinets, which we build in our workshop. In this way, we increase the internal degree of prefabrication of our modules. In addition, this solution reduces assembly and commissioning times, as we carry out the wiring of the modules and the signal check before delivery. The basis of Industry 4.0 is to collect as much digital data as possible in real time and to make it available to higher-level systems for intelligent evaluation and further processing. This increases the demands on the sensors and communication paths installed in the system.
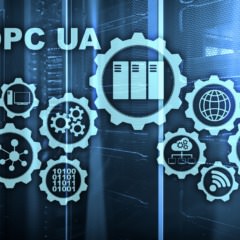
Networking in the industrial aera
Connection of the system modules and control components
in many cases our process engineering systems are very extensive. Data and measured values are generated at most diverse points and under most diverse conditions, devices are controlled and the operation of the plants is made possible. We use industrial Ethernet, mainly ProfiNet or Ethernet I/P, for the continuous networking between the plant parts and the control components. Depending on the requirements, this is coupled with various other networks such as AS-i Bus and IO-Link. Open Platform Communications (OPC-UA) is now used as a standard for exchange between systems from different manufacturers or sources. For example, data can be collected from different PLC systems and software applications. This data is available to various applications and databases via a uniform interface. OPC technology thus enables manufacturer-independent communication between different systems and supports the comprehensive control and tracking of production processes.
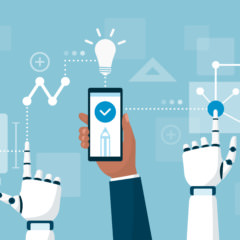
Monitoring of the production process
Automation systems according to the requirements by the process
The choice of automation system depends on the process requirements. For simply constructed plants, we use HMI operator panels to control the plants. In more complex plants SCADA systems are usually used. SCADA systems are based on PCs and offer a wide range of possibilities with their scalability and functionalities. The SCADA system can be scaled from a single-user to a decentralised multi-user system with a large number of operator stations. Additional functions such as redundant designs, distributed and secure data storage or access via mobile terminals increase the availability and user-friendliness of the plants. With these SCADA systems, plant operators can monitor the entire production process in real time. If necessary, they can react quickly, debug any disruptions in the production process directly and avoid production downtimes.
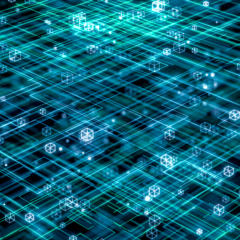
Plant automation made by Ruland
Plant management with RPMS – Ruland Process Management System
Individual plants often require individual solutions for plant automation. Our specialists work with the Microsoft .NET development aera, which is used for customised applications. For higher-level plant management our developers have developed the Ruland Process Management System (RPMS). RPMS controls and records the complete production process. RPMS manages and coordinates the individual PLC controls at plant management level and organises the daily production flow. In addition, it offers customisable interfaces to ERP systems, financial and CRM software or laboratory software, provided that this data is relevant to the production process. The various modules of our process management system reflect the individual areas of the manufacturing process. The system is freely scalable and combinable and can also be used in small applications, as for example as a simple production data acquisition system. The Ruland Process Management System can manage resources for the process | plan productions from resources | run processes product-dependently via different recipes | create production plans with the help of recipe orders | store and retrieve quality characteristics with associated evaluations | document and track product flow in the form of batches | document and archive process values and process events as reports.
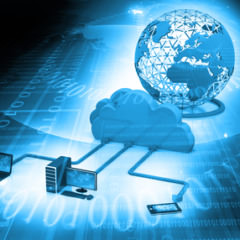
Remote maintenance and remote access
In case of malfunctions and online maintenance
Our plant specialists can access the plants via secured remote maintenance systems if necessary. Remote access to our systems is standard in order to support the customer quickly in case of a malfunction, for error analyses and for maintenance. System updates and minor optimisations can also be carried out online via remote access. As a rule, access or the network connection to the customer’s network is carried out with the customer’s existing security mechanisms.