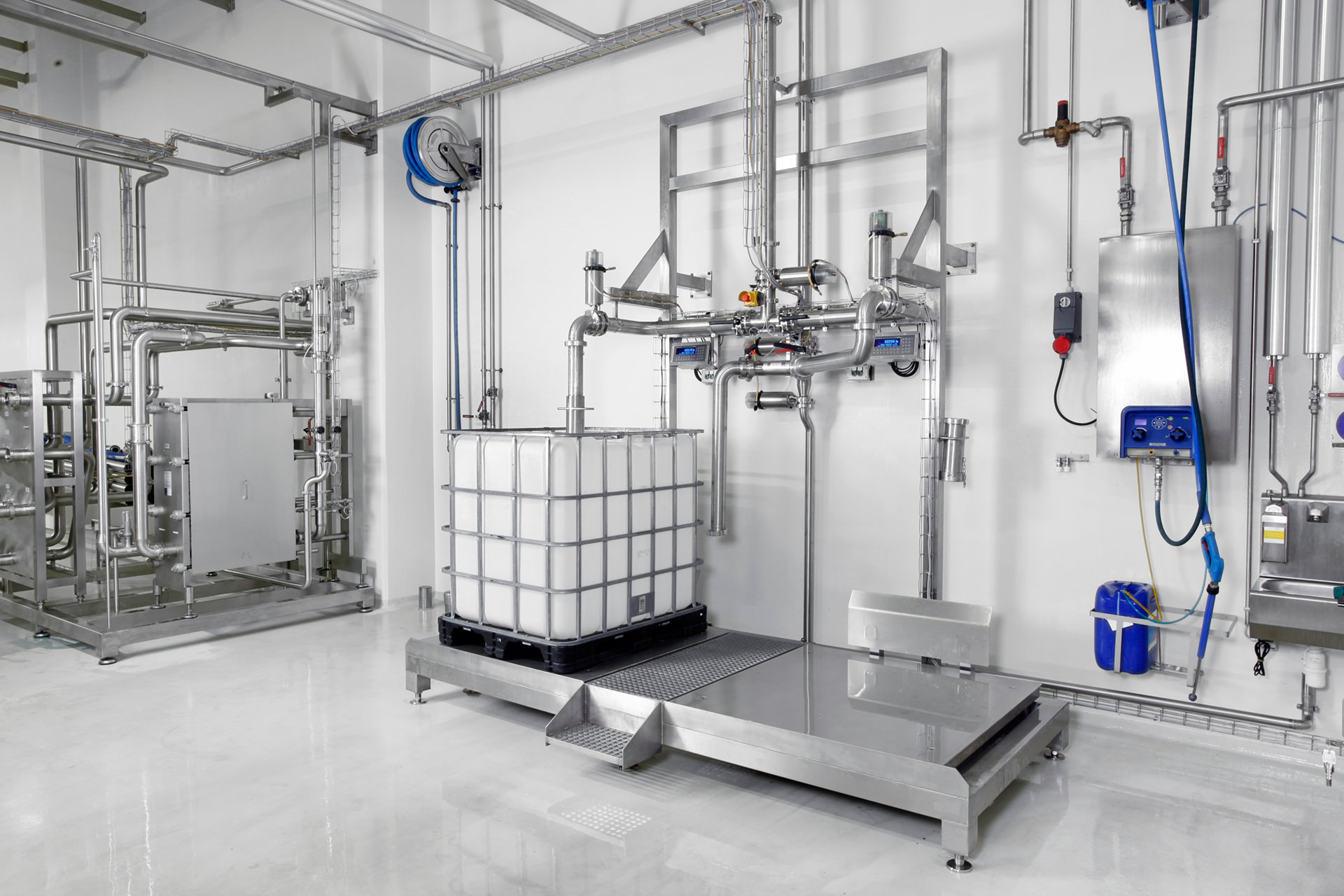
Container handling
Modular container stations for consistent aseptic handling
Frequently, stainless steel containers, aseptic IBC (Intermediate Bulk Containers) or aseptic disposable containers are used for the transportation or storage of liquid products. These containers must also be kept consistently germ-free with the help of a sterile process. Critical points are always the filling in and draining out from transport containers. To this end, we have developed special container stations. Ruland provides systems for washing, cleaning and sterilising that simplify handling thanks to our having paid attention to many details. Furthermore, these automated systems can be validated. In order that every company can build its own aseptic container management, our systems for container handling are available as a flexible and modularly designed range of components.
Our scope
Cleaning / Sterilisation / Filling / Emptying / Dosing
Best practice: Container station for aseptic filling and draining
Minimum losses with aseptic filling
Producers of foods, pharmaceutical, body and health care products or chemicals very frequently use mobile containers for the transportation or intermediate storage of their liquid products.
Producers of foods, pharmaceutical, body and health care products or chemicals very frequently use mobile containers for the transportation or intermediate storage of their liquid products. Such products include everything ranging from ointments, creams, basic compounds for beverages to fruit preparations, yoghurts, flavours and pastes through to paints and varnishes. The diversity of products being transported covers everything from low-viscosity, diluted products to semi-solid products. There are various reasons for the use of such containers:
- Transport to the commissioned bottling company
- Transport for further processing
- Transport to the customer
- Intermediate storage
Among other things, the advantage of this packaging is that it can really be used again. Its durability contributes to avoiding waste and also conserving natural resources. For sensitive products, such as those from the food industry, the manual connection of the container to the production unit (mixer, mixing station, etc.) or the filling unit is absolutely critical. This is because microorganisms could penetrate when the system is opened.
Based on the long-term experience with our customers, Ruland has developed a container station that offers a number of advantages in terms of handling. Furthermore, this station eliminates the microbiological risk and the entire process is automated and documented.
The transport/storage container
Generally speaking, these containers have a volume capacity of 200 to 1,500 litres and are capable of incorporating a wide range of extra features including:
- Pressure/vacuum container
- Double walls for heating or cooling
- Insulation
- Various angles of sloping bottom/outlet depending on the flow properties of the product
- Screwed down, hinged and screwed or bayonet locking lids
- Integrated safety valves, ventilation valves, sterile filters and other fittings
- Stackability within a single system
- Material AISI 316L
The key feature that the containers have in common is the outlet valve. In the food industry, for example, the DN 50 butterfly valve with a DIN 11851 threaded connection has become standard. Meanwhile, in pharmaceutical production companies there is a larger variety of fittings and connections, and special adapters are designed for them.
The container cycle
In cases where high standards of hygiene are required, special measures are necessary in order to ensure microbiological safety. This requires both the container and the piping associated with it having to be sterilised. The measures are less complex when it comes to less sensitive products.
Container sterilisation
The sterilisation process involves steam being passed through the container. The sterilisation time and temperature profile will depend on the product for which it is intended as well as the design capacity of the container. The direction of steam flow (top down or bottom up) is also dependent on the existing connections and their nominal diameters. Sufficient throughput must be achievable for both fast heating and for the dry blowing. Following sterilisation, the steam is blown out of the container with sterile air or nitrogen and the system is dried.
Sterilisation of the feed lines
The sterilised container stands on a weighing machine at the filling station. Prior to being filled, the input piping must also be steam sterilised. The filling hose is manually connected – either directly or via a short length of pipe with a screw fitting – to the butterfly valve on the container and the feed line is now steamed down to the closed disc valve on the container. This can result in condensate escaping through a small valve on the connecting pipe. Filling can start immediately after sterilisation time or the piping can alternatively be blown dry with sterile air. It is essential in both instances to avoid vacuum formation from steam condensation in the feed line.
Filling the container
The container valve is opened, the tare weight established on the scales and the container is then filled until a signal from the scales closes the valve again. The air that is displaced during this process must be vented through a sterile filter that can either be integrated or attached to the container, but only so much that higher pressure is retained in the head space. The actual filled weight is printed onto the container label and the container is then prepared for dispatch.
Transport to the customer
The container is transported to the customer or the place of destination within the production facility. For this adequate features as castors, fork-lift plates, connector for handling devices are required.
Emptying the container
The full container with a slight head of pressure is connected to an outlet pipe and emptied. In principle, the same steps are required as is the case with filling. The outlet pipe is sterilised and blown dry and the container is then emptied. The pressure head is maintained during emptying by piping in sterile air or nitrogen.
Return journey
The container is then returned to the filling factory.
Container cleaning
The container is first depressurised and then connected to a CIP unit and cleaned. The cleaning process comprises pre-rinsing, washing with an alkaline agent and rinsing. Depending on the product, a second rinse step with an acid agent may be included and cleaning of the exterior is also recommended. Following cleaning, the container is re-assembled and can then be put through the sterilisation process again.
Special features of the Ruland Container Station
The experience with the use of transport/storage containers in the production facilities of several customers was the incentive for the creation of a container station that would both improve working conditions and guarantee a safe work process. Therefore, Ruland added the relevant equipment to the basic design.
A pneumatic connector is used for an operator-friendly, time-saving handling when connecting and disconnecting. This enables the filling head to be pressed into the butterfly valve of the container, which in turn creates a leakage proof connection. The actuator is engineered to assure a safe connection even if air is lost and it should be noted that the valve variations will have to be checked. Meanwhile, the product and service media valves are directly welded onto this pneumatic connector in order to keep dead space to a minimum and guarantee very low product losses. The filling head has handles and is attached to a cantilever arm with a balancer to enable easy and weight-free handling.
The valves used for sterile filling meet aseptic process engineering specifications as diaphragm valves or butterfly valves, if sterility requirements are less stringent. The valves are arranged so as to avoid dead spaces that might not be fully cleaned during rinsing or CIP treatment. If required, a sampling facility can be integrated.
Temperature and pressure measurements are captured in both the feed line and the container for sterility control and monitoring. The key process parameters are set data in the control. The automated process following connection of the filling head to the container comprises the following steps:
- Input product data such as the operator’s name, customer data, product, batch number, tank capacity, tank number, filling weight
- Sterilise piping with time and temperature monitoring
- Blow dry pipes
- Open container valve/fill tank/close container valve
- Rinse filling head
- Blow out rinsing water from filling head
- Disconnect filling head
- Batch end or change of container
A weighing module that can be calibrated precisely measures the container content. Barcode readers can directly read the container number. Furthermore, the control can be connected with other superior systems and is capable of exchanging data with these systems. The process is displayed with a touch panel and you can also record data and archive the complete process, and thus maintain records of critical parameters, which can be followed if necessary.
Filling and emptying of IBC containers
The modular container station support easy and safe filling and emptying of transport containers.
The pneumatic lift enables an inclined position, and thus an optimum emptying of the mobile containers without any residuals. The integrated lifting and lowering function and the non-spill quick coupling offer special operating comfort.
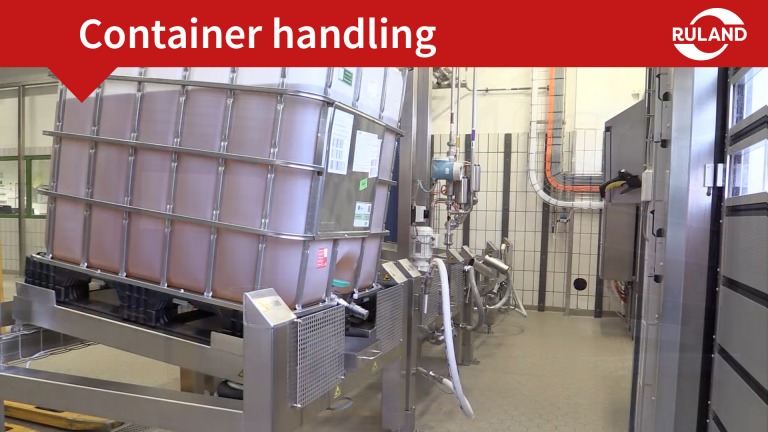
Click at the link below to activate the video. Please note that after activation your data will be submitted to the respective provider.
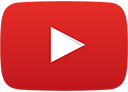
Are you interested in container handling?
Please do not hesitate to get in touch.
All on our systems for container handling in short in our flyer.