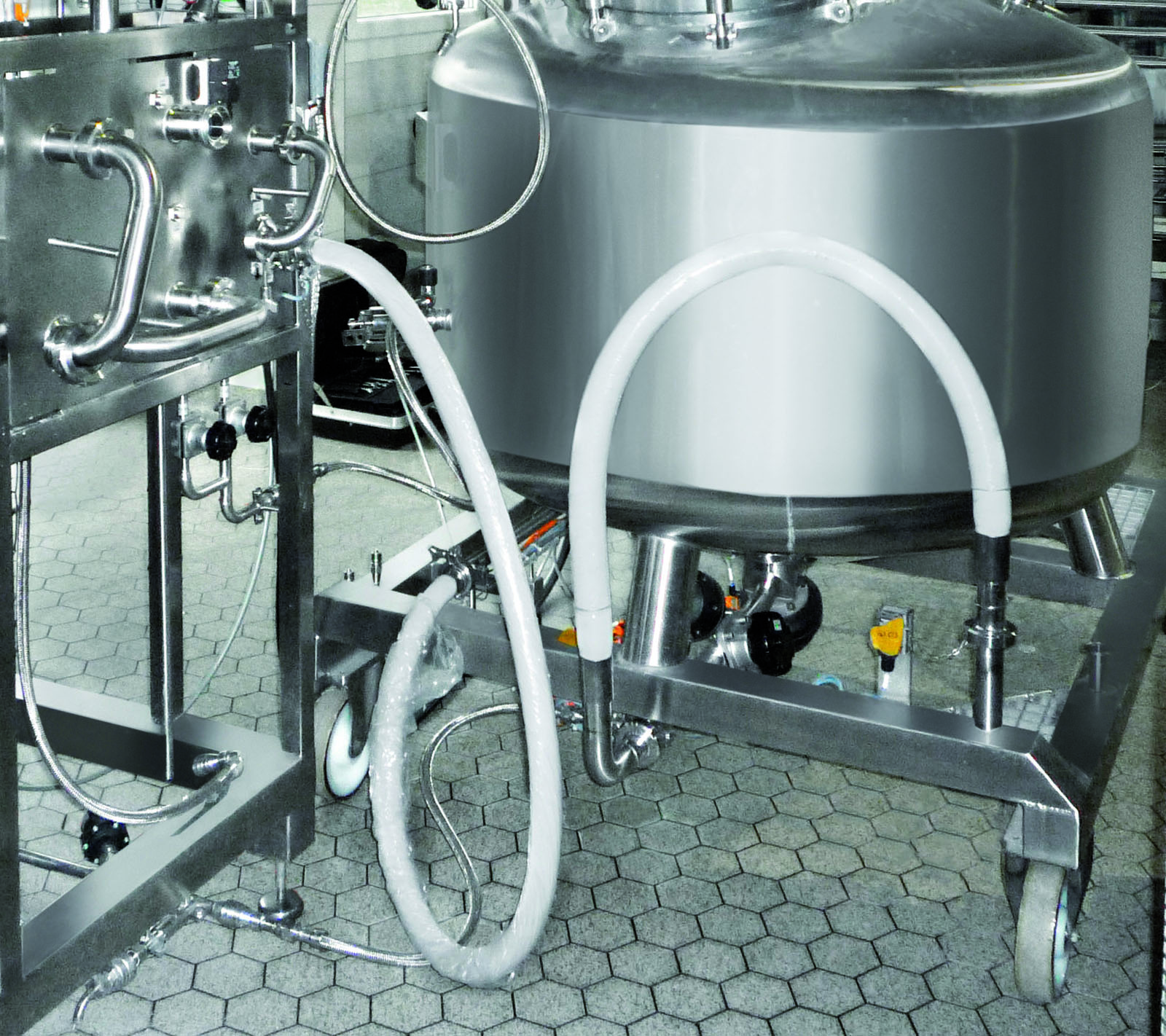
Raport dotyczący projektu
Małe partie – duża różnorodność produktów
Plantextrakt GmbH & Co. KG
Do wytwarzania skomplikowanych produktów w niewielkich partiach wymagane jest zastosowanie zoptymalizowanych procesów technologicznych.
Ruland zbudował instalację technologiczną do pasteryzacji ekstraktów z ziół i herbaty dla firmy Plantextrakt GmbH & Co. KG w Vestenbergsgreuth. Plantextrakt jest jednostką biznesową Grupy Martin Bauer i światowym leaderem w produkcji ekstraktów z herbaty, owoców i ziół oraz bezkofeinowej czarnej herbaty i bezkofeinowej zielonej herbaty.
Innym obszarem działalności firmy jest wytwarzanie aromatu herbaty. W sumie, firma oferuje ponad 2000 indywidualnych receptur bazujących na wykorzystaniu ponad 120 różnych roślin. Aby wejść na nowe rynki z istniejącymi produktami, firma Plantextrakt chciała rozszerzyć zakres swojej działalności produkcyjnej o pasteryzację i aseptyczne napełnianie. W ramach projektu konsultingowego, firma Ruland i klient opracowali trójstopniową koncepcję rozbudowy zakładu produkcyjnego.
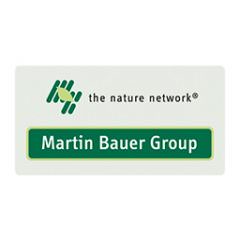
Interesującym zadaniem na etapie konsultacji była koordynacja dyskusji ze wszystkimi działami firmy Plantextrakt. Przedyskutowano wszystkie za i przeciw wynikające z potrzeb zgłaszanych przez poszczególne wydziały firmy oraz zdefiniowano parametry projektowe dla nowego obszaru produkcyjnego, takie jak podwyższenie poziomu jakości poprzez zastosowanie pojemników aseptycznych, niewielkie partie produktów, częste zmiany asortymentu produkcji, wysoka lepkość produktów, jak najmniejsze straty produktów.
Na etapie realizacji projektu, w ramach rozbudowy zakładu wybudowano nową halę produkcyjną obok istniejącego obszaru mieszania. Aby ułatwić stałe zarządzanie zaopatrzeniem w media, firma RULAND zaplanowała rurociągi energetyczne oraz ich układ w nowym budynku przywykorzystaniu modelowania 3D. W planach uwzględniono możliwość późniejszej rozbudowy istniejącej instalacji oraz budowy nowej instalacji.
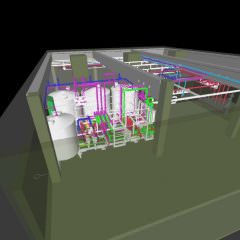
Zrealizowana instalacja
Zrealizowana instalacja technologiczna składa się z modułu nagrzewania z podłączeniem do istniejącego obszaru mieszania, 6000 litrowego zbiornika sterylnego, dwóch mobilnych pojemników, stacji CIP, połączonej podwójnej stacji mycia i sterylizacji tych mobilnych pojemników oraz podwójnej stacji mycia dla 1000 litrowych pojemników z tworzywa sztucznego. Produkty, ze zbiornika sterylnego lub mobilnego pojemnika, są aseptycznie napełniane za pomocą napełniarki bag-in-box. W pierwszym etapie budowy, linię nagrzewania zrealizowano jako instalację czyszczoną poprzez przepuszczanie tłoka, o wydajności 500 l/h. To rozwiązanie optymalnie spełnia wymagania określone na etapie konsultacji. Ze względu na niską prędkość procesu produkcji (500 l/h) zastosowano instalację rurową o małej średnicy (w tym przypadku DN 20). W przypadku instalacji rurowych o większych średnicach,
wymiana ciepła byłaby ograniczona ze względu na gorsze warunki przepływu. Zastosowanie instalacji rurowej o jeszcze mniejszej średnicy spowodowałoby zwiększenie strat ciśnienia, co z kolei wymagałoby użycia bardziej wydajnych wymienników ciepła i pomp produktu. Aby uzyskać prawidłowe specyfikacje dla wymiennika ciepła, we wczesnej fazie projektu przeprowadzono testy na instalacji pilotażowej. Wiele produktów Plantextrakt ma relatywnie niską zawartość wody (50 do 65% suchej substancji) i produkty te muszą być chronione przed działaniem świeżej wody lub kondensatu podczas obróbki w instalacjach technologicznych. Rozwiązaniem jest „odizolowanie” produktu na początku i na końcu produkcji przy wykorzystaniu technologii czyszczenia rurociągu poprzez przepuszczanie tłoka czyszczącego. Dla rurociągów o mniejszej średnicy opracowano specjalny tłok czyszczący.
Dostarczanie dużych i małych partii produktu
Produkt może być dostarczany do podgrzewacza na dwa sposoby. W przypadku większych partii produktu, do 6000 litrów, stosowane są zbiorniki w obszarze mieszania. Produkt jest transportowany z tych zbiorników przez rurociąg transferowy do pojemnika zasilającego moduł podgrzewania. Aby zapobiec mieszaniu produktów, również w tym przypadku stosowana jest technologia czyszczenia rurociągu poprzez przepuszczanie tłoka czyszczącego. Na koniec produkcji, tłok czyszczący jest przepychany przez rurociąg przy użyciu sprężonego powietrza. Dzięki temu, woda nie dostaje się do produktu, ponieważ rurociąg produktu jest suchy zarówno przed rozpoczęciem jak i po zakończeniu produkcji. W przypadku mniejszych partii produktu, do 1000 litrów, mobilne pojemniki można napełniać w obszarze mieszania i przeładowywać bezpośrednio do podgrzewacza. Dzięki temu, można zminimalizować straty produktu wynikające z przylegania produktu do ścianek pojemnika lub połączeń przewodów giętkich. Poprzez interfejs, mobilne pojemniki są połączone ze sterownikiem i są w pełni zautomatyzowane. Wszystkie połączenia przewodów giętkich o krytycznym znaczeniu dla jakości produktu są nadzorowane przez układ sterowania. Sterylność i ciśnienie systemowe pompy podgrzewacza są monitorowane i kontrolowane przy użyciu czujnika ciśnienia. Urządzenia uruchamiające mogą być również obsługiwane ręcznie za pomocą skrzynki sterowniczej mobilnego pojemnika. W ten sposób, mobilne pojemniki mogą być używane również w przypadku, gdy nie ma możliwości połączenia z układem sterowania,
na przykład na stacjach instalacji pilotażowej. Mobilne pojemniki są stosowane również jako zbiorniki sterylne. Umożliwia to pasteryzację niewielkich partii produktu przy przepływie z jednego mobilnego pojemnika do drugiego. Pojemniki mogą być magazynowane przed wydaniem zgody na napełnianie. Oczywiście, możliwe jest również napełnianie pojemnika z jednej strony i odprowadzanie produktu do nalewarki z drugiej strony pojemnika, jak w przypadku każdego zbiornika sterylnego. Stacja CIP/SIP zapewnia możliwość czyszczenia i sterylizacji mobilnych pojemników. W tej stacji, pojemniki są czyszczone i, jeżeli jest to wymagane, sterylizowane czystą parą wodną, przy czym wszystko odbywa się w trybie w pełni automatycznym. Po sterylizacji, kondensat jest wydmuchiwany, a pojemniki są napełniane sterylnym powietrzem. Plantextrakt przechowuje wiele półproduktów do mieszania w 1000 litrowych pojemnikach z tworzywa sztucznego i czasami dostarcza je w tych pojemnikach do klientów. Ze względu na różnorodne zastosowanie pojemników, konieczne jest ich dokładne czyszczenie. W przeciwnym razie, może dojść do zanieczyszczenia produktów wlewanych później do pojemników. Aby ujednolicić i zautomatyzować czyszczenie pojemników z tworzywa sztucznego, firma RULAND dostarczyła stację czyszczenia dla dwóch plastikowych pojemników, która jest połączona ze stacją CIP i do której doprowadzone są wszystkie media. Tą stację czyszczenia można rozbudować, aby zapewnić trzecie stanowisko czyszczenia.
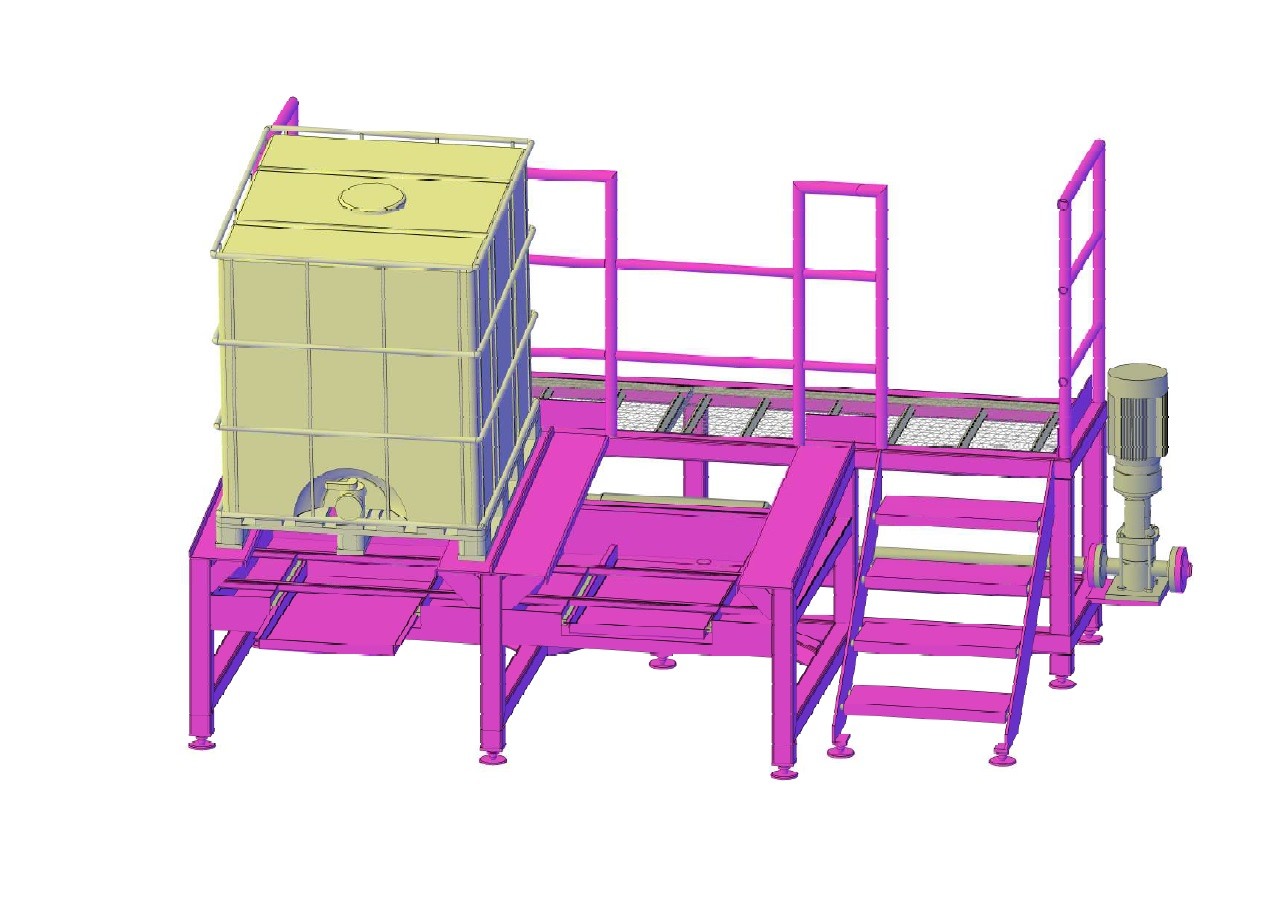
Czyszczenie i kontrola instalacji technologicznej
Czterozbiornikowa instalacja CIP z dwoma układami czyszczenia jest używana dla instalacji technologicznych i stacji CIP dla mobilnych, plastikowych pojemników. Instalacja może być rozbudowana do czterech układów czyszczenia. W celu uzyskania optymalnej jakości czyszczenia wszystkich elementów składowych instalacji (podgrzewacza, zbiornika sterylnego i napełniarki), wdrożono system administrowania recepturami. Umożliwia to stosowanie indywidualnych receptur czyszczenia dla wszystkich grup produktów. Nadzór i obsługa instalacji wykonywane są przy użyciu 19“ ekranu dotykowego na module podgrzewacza i komputera klasy PC w sterowni. Obie stacje są zaprojektowane w identyczny sposób. Ich obsługa jest ułatwiona przez to, że mają taki sam wygląd i funkcje. W przemyśle spożywczym, kompletna rejestracja wszystkich etapów produkcji stanowi ważną część systemu zarządzania jakością. Oprogramowanie do rejestracji partii produktów może być bardzo precyzyjnie dostosowane do potrzeb użytkownika. W firmie PLANTEXTRAKT, wraz z numerem zamówienia wprowadzane są takie informacje jak programy sterylizacji, wszystkie aktualizacje statusu, alarmy, dane wprowadzone przez operatora i wybrane diagramy dotyczące poszczególnych partii.
Z przyjemnością doradzimy Ci osobiście.
Czekamy na wyzwanie!