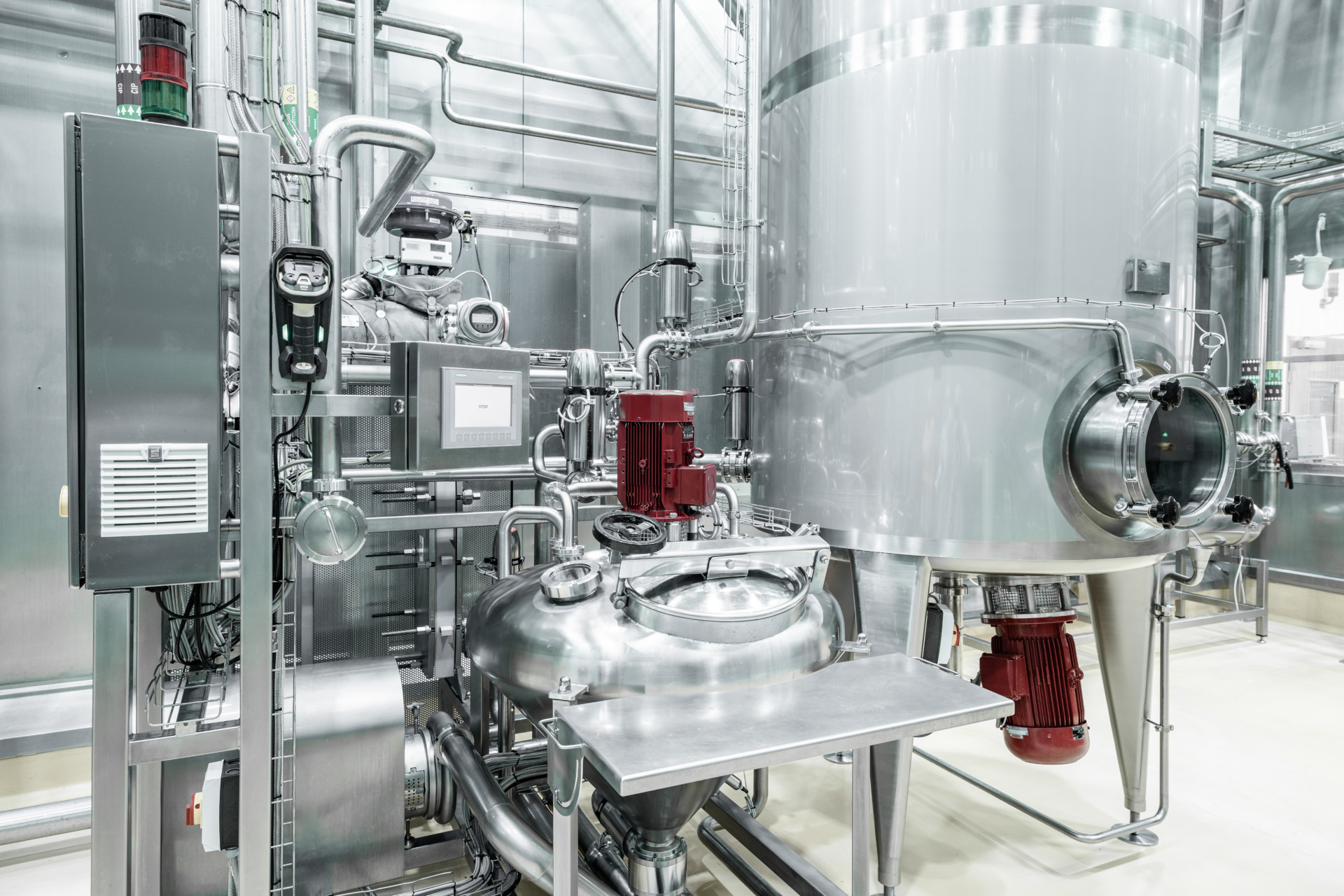
Zaawansowana technologia rozpuszczania w produkcji napojów
Uniwersalne rozwiązanie dla szerokiego zakresu surowców
Nasze systemy rozpuszczania i dozowania komponentów sypkich gwarantują wysoką skuteczność procesu rozpuszczania, powtarzalną jakość produktu i maksymalną wydajność – nawet w przypadku słabo rozpuszczalnych proszków, takich jak pektyna, guma ksantanowa lub środki zagęszczające. Uniwersalność systemu powoduje, że układ doskonale odpowiada na potrzeby producentów napojów energetycznych i funkcjonalnych, których receptury są często złożone i wymagające pod względem dozowania oraz rozpuszczalności składników aktywnych.
Czyste rozpuszczanie i precyzyjne dozowanie
Niezawodność procesów
Produkcja napojów, to złożony proces, który wymaga precyzji, higieny oraz nowoczesnych technologii. W obecnych czasach nie mniej ważna jest elastyczność, bycie innowacyjnym i odpowiedzialnym. Producent musi reagować na trendy konsumenckie, wyzwania środowiskowe, technologiczne czy też te związane z automatyzacją – jednocześnie zachowując konkurencyjność i wysoką jakość produktów. Jako lider rynku urządzeń przemysłu spożywczego, mamy świadomość jak kluczowym etapem w produkcji napojów jest rozpuszczanie i dozowanie. Dostarczane przez nas rozwiązanie gwarantuje jakość, bezpieczeństwo, powtarzalność i opłacalność całego procesu technologicznego, ze szczególnym naciskiem na:
- wysoką efektywność rozpuszczania – nawet w przypadku substancji krytycznych,
- bezpyłową obsługę i higieniczną konstrukcję,
- precyzyjne i automatyczne dozowanie,
- modułową konstrukcję – możliwość pełnego dostosowania do zróżnicowanego asortymentu produktów,
- łatwą integrację z istniejącymi liniami produkcyjnym.
Standardy EHEDG w praktyce
Bezpieczne i czyste rozwiązania gwarantujące niezawodne rozpuszczanie proszków
Instalacje naszego autorstwa powstają w oparciu o rygorystyczne zasady higienicznego projektowania. Naszym priorytetem jest zapewnienie pełnej zgodności z wymaganiami sanitarno-technicznymi, które są kluczowe w przemyśle spożywczym i napojowym. Dlatego – jako aktywny członek organizacji EHEDG – przywiązujemy szczególną wagę do spełniania najwyższych standardów w zakresie higieniczności konstrukcji – począwszy od etapu projektowania, przez prefabrykację, aż po montaż i uruchomienie instalacji u klienta. W przypadku układu rozpuszczania komponentów sypkich, higieniczny design znajduje odzwierciedlenie w:
- doborze materiałów – wszystkie elementy mające kontakt z produktem wykonane są ze stali nierdzewnej dopuszczonej do kontaktu z żywnością,
- konstrukcji bez martwych stref – zapewniającej łatwość czyszczenia i brak zalegania produktu,
- rozwiązań procesowych – umożliwiających automatyczne mycie (CIP), opłukiwanie opakowań oraz pełną kontrolę parametrów procesowych.
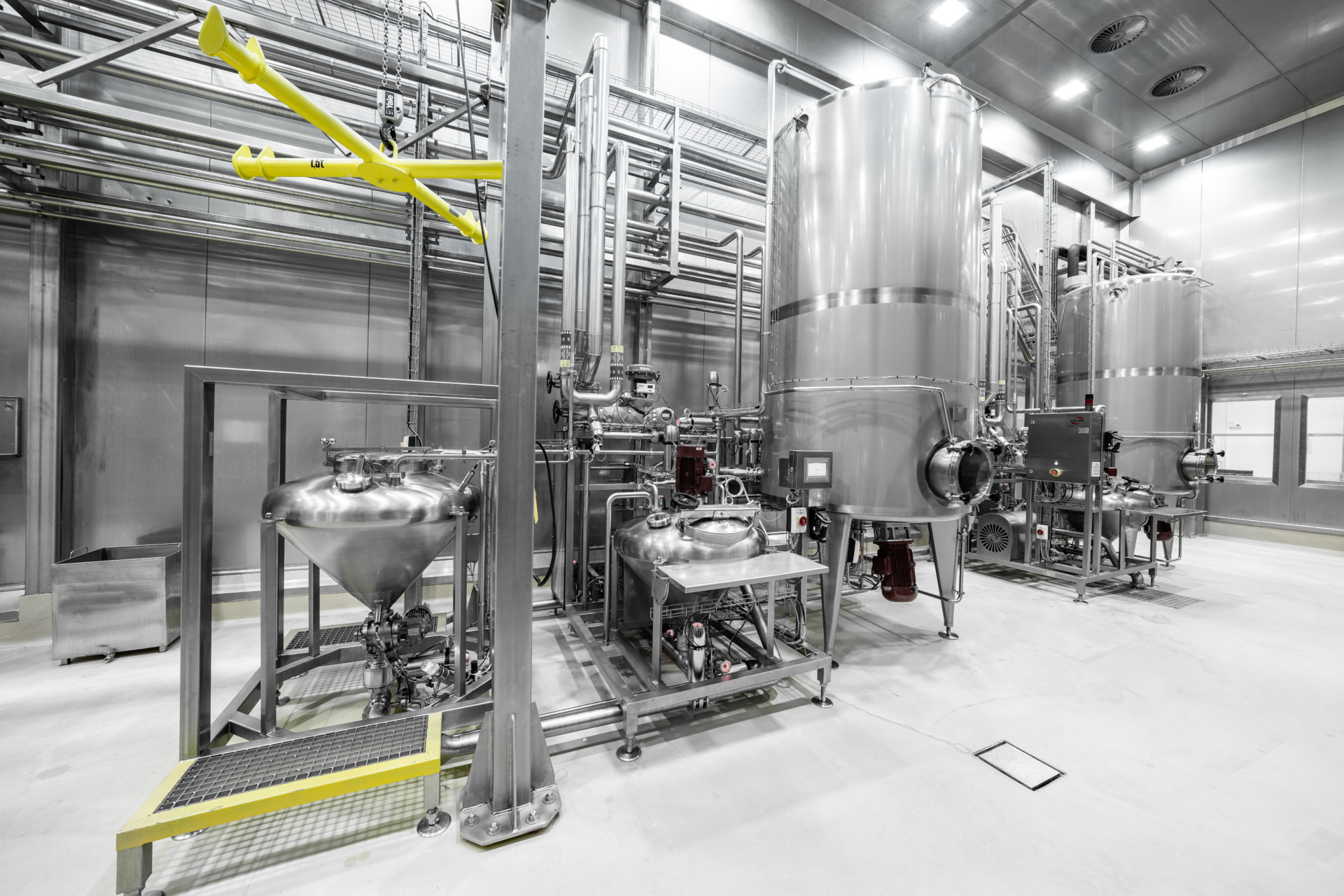
Modułowy system dozowania i rozpuszczania
dla wydajnej produkcji napojów
Opracowany system rozpuszczania i dozowania komponentów sypkich składa się z kilku kluczowych elementów, takich jak: dwa zasypniki, zbiornik reakcyjny, układ grzewczy oraz suwnica przeładunkowa. Każdy z tych modułów został zaprojektowany z myślą o maksymalnej funkcjonalności, higieniczności i elastyczności zastosowań w środowisku produkcji napojów. Pierwszy zasypnik przystosowany jest do pracy z komponentami występującymi w dużych ilościach – dostarczanymi głównie w workach typu big-bag. Z tego względu instalacja wyposażona została w zintegrowaną suwnicę, umożliwiającą sprawną obsługę tego typu opakowań. Konstrukcja suwnicy wykonana jest w całości ze stali nierdzewnej, co pozwala na jej zastosowanie w strefach higienicznych oraz umożliwia mycie i pianowanie bez ryzyka powstania korozji. Dodatkowo, specjalna konstrukcja zasypnika ogranicza emisję pyłu w trakcie opróżniania big-bagów, co znacząco poprawia warunki pracy i bezpieczeństwo procesu. Drugi zasypnik został zaprojektowany jako moduł uniwersalny – umożliwia dozowanie zarówno komponentów sypkich, jak i płynnych, pochodzących z różnorodnych opakowań – worków, butelek czy kanistrów. Dzięki wysokiemu poziomowi elastyczności układ może być wykorzystywany zarówno do rozpuszczania na zimno, jak i na ciepło dzięki zastosowaniu wymiennika ciepła. Zintegrowany wymiennik odpowiada za kontrolę parametrów cieplnych i umożliwia zarówno podgrzewanie wody procesowej, jak i precyzyjne sterowanie temperaturą gotowego roztworu, aby spełnić wymagania realizowanej receptury
Trójstopniowy układ rozpuszczania
Maksymalna efektywność i elastyczność procesu
Kluczowym elementem gwarantującym skuteczność rozpuszczania jest trój-etapowe mieszanie. Proces rozpoczyna się od podania niewielkiej ilości wody do zasypnika, gdzie operator może wprowadzić komponent, który zostaje natychmiast rozdrobniony i wstępnie rozpuszczony za pomocą szybkoobrotowego mieszadła tnącego. Takie podejście znacząco skraca czas procesu i poprawia jednorodność mieszaniny już na jego wczesnym etapie. Drugim kluczowym etapem procesu jest zassanie wstępnie rozpuszczonego komponentu do układu za pomocą dyszy inżektorowej, a następnie jego cyrkulacja w zamkniętej pętli. Etap trzeci to właściwe, finalne mieszanie w zbiorniku reakcyjnym. Odbywa się ono z wykorzystaniem dwóch uzupełniających się elementów: dolnego mieszadła typu high-shear, precyzyjnie dobranego do charakterystyki medium, oraz dyszy turbo-jet, która generuje intensywny strumień powodujący skuteczną recyrkulację wewnątrz zbiornika i równomierne wymieszanie całej objętości. Zastosowanie tego rozwiązania umożliwia efektywne i szybkie rozpuszczenie wszystkich komponentów, niezależnie od ich właściwości fizykochemicznych.
Elastyczna technologia dozowania
Adaptowalne rozwiązanie systemowe dla różnych wielkości partii
System został zaprojektowany z myślą o maksymalnej elastyczności operacyjnej – umożliwia zarówno pełne wykorzystanie objętości roboczej zbiornika, jak i pracę z mniejszymi szarżami produkcyjnymi. To szczególnie istotne w zakładach, gdzie produkowane są różnorodne receptury w krótkich seriach. Dodatkowo, dolne mieszadło zapewnia skuteczne mieszanie także w trakcie opróżniania zbiornika, co jest wymagane przez niektóre receptury – zwłaszcza te, w których istotne jest zachowanie jednorodności aż do momentu przepompowania roztworu do kolejnego etapu procesu. Zbiornik reakcyjny został wyposażony we wziernik i szklany właz, które umożliwiają kontrolę wizualną w czasie rzeczywistym bez przerywania procesu. Ponadto składany stół roboczy na zasypniku zapewnia łatwą obsługę szerokiej gamy typów opakowań. Znacząco zwiększa to ergonomię i poprawia bezpieczeństwo pracy.
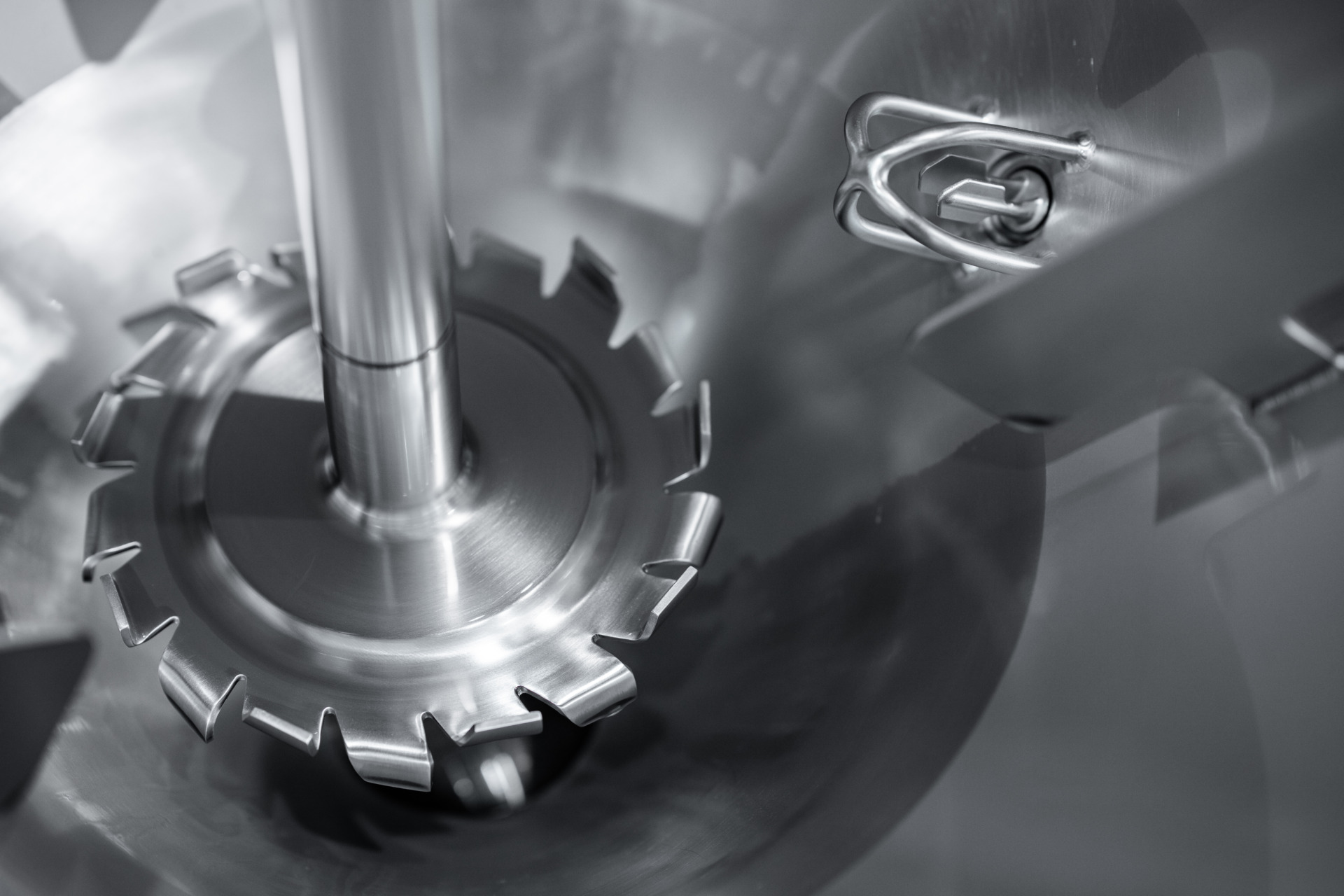
System czujników i inteligentne sterowanie
– gwarancja bezpieczeństwa w systemach Ruland
Projektując instalacje procesowe, przywiązujemy dużą wagę do kompleksowego podejścia w zakresie bezpieczeństwa – zarówno operatora, jak i realizowanego procesu technologicznego. System zabezpieczeń oparty jest na trzech uzupełniających się poziomach: mechanicznym, elektrycznym i programowym. W części zasypowej zastosowano fizyczne zabezpieczenie w postaci kraty, która zapobiega przypadkowemu przedostaniu się fragmentów opakowań do wnętrza układu. Dodatkowo, krata ta została zintegrowana z systemem czujników położenia – ich zadaniem jest natychmiastowe wyłączenie mieszadła w przypadku jej demontażu.
Zautomatyzowana kontrola receptur rozpuszczania i dozowania
dla powtarzalnej jakości produktu
Kluczowym elementem całego układu jest autorski program recepturowy, opracowany przez firmę Ruland. System ten w sposób ciągły monitoruje parametry procesu, takie jak temperatura medium, prędkości obrotowe mieszadeł oraz czasy poszczególnych faz mieszania. Dzięki temu operator otrzymuje jasne i precyzyjne wskazówki – dotyczące kolejności, momentu oraz ilości dodawanych komponentów. Tak zaprojektowane środowisko pracy minimalizuje ryzyko błędów ludzkich, zapewniając jednocześnie wysoką powtarzalność procesów oraz zgodność realizacji z założeniami receptury – co ma kluczowe znaczenie dla jakości końcowego produktu. Dzięki inteligentnemu połączeniu automatyzacji i bezpieczeństwa tworzymy kontrolowane środowisko procesowe. Takie podejście gwarantuje stałą jakość produktu – niezależnie od operatora lub partii. W ten sposób system spełnia wszystkie wymagania nowoczesnej produkcji napojów: jest bezpieczny, powtarzalny i wydajny.
Intuicyjne oprogramowanie do receptur
z funkcją automatycznego obliczania ilości składników
Nasze przyjazne dla użytkownika oprogramowanie do receptur jest integralną częścią systemu sterowania instalacją. . Interfejs został zaprojektowany w taki sposób, aby po krótkim szkoleniu prowadzonym przez ekspertów Ruland, użytkownik mógł samodzielnie tworzyć nowe receptury lub modyfikować już istniejące. Oprogramowanie dostarczane wraz z instalacją ma otwartą strukturę i nie wiąże się z dodatkowymi kosztami użytkowania – nie wymaga wykupu licencji ani subskrypcji. Co więcej, system automatycznie wylicza ilości poszczególnych komponentów na podstawie zadanej wydajności, co znacząco upraszcza planowanie i realizację produkcji. Tym samym cały proces produkcyjny jest zaplanowany efektywnie i jest wykonywany niezawodnie.
Nowoczesny układ rozpuszczania
- optymalizacja procesu i redukcja strat
W opracowanym przez firmę Ruland systemie rozpuszczania i dozowania zastosowano szereg rozwiązań technicznych, które realnie wpływają na ograniczenie kosztów eksploatacyjnych oraz zwiększenie wydajności procesu. Przykładem jest wykorzystanie jednej pompy zarówno do rozpuszczania, jak i przepompowywania gotowego roztworu. W połączeniu z bezobsługowym systemem inżektorowym oraz odpowiednim sparametryzowaniem elementów układu, rozwiązanie to umożliwia znaczące ograniczenie zużycia mediów oraz kosztów serwisu. Dodatkową funkcjonalnością zwiększającą efektywność instalacji jest specjalnie zaprojektowany system opłukiwania opakowań. Pozwala on na odzyskiwanie pozostałości składników z opakowań, co ogranicza ich straty i wpływa na wysoką dokładność oraz powtarzalność procesu dozowania. Co istotne, woda używana do opłukiwania nie jest traktowana jako strata – jej objętość jest automatycznie zliczana i uwzględniana w bilansie wodnym realizowanej receptury.
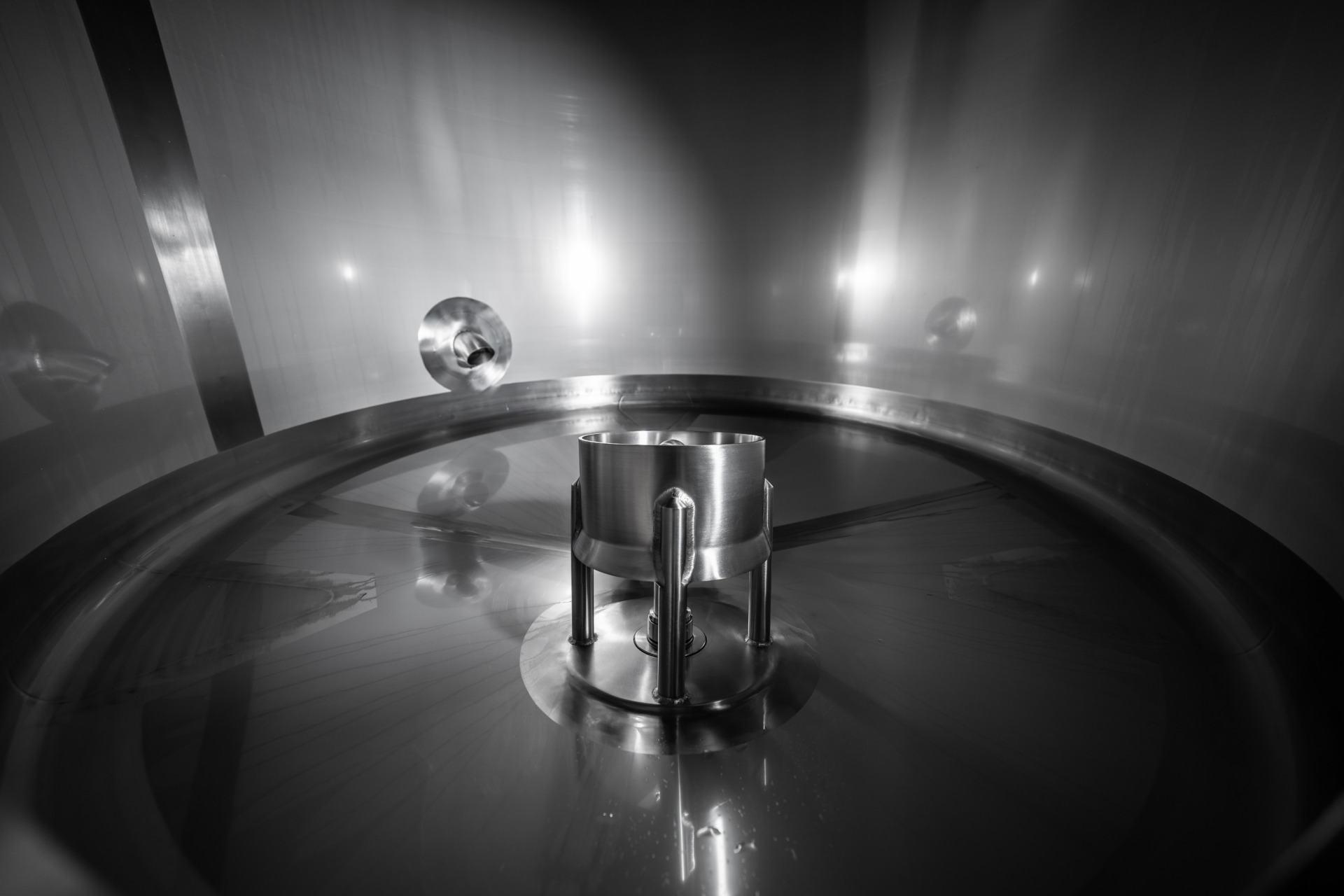
Modułowe, skalowalne, przyszłościowe
zautomatyzowane systemy dla szerokiego zakresu receptur
Systemy rozpuszczania i dozowania, jakie mamy w swoim portfolio to rozwiązanie uniwersalne, które z powodzeniem zostało wdrożone u wielu klientów z branży napojowej. Innowacyjna konstrukcja, wysoki poziom automatyzacji i dbałość o detale sprawiają, że system stanowi kluczowy element nowoczesnej i wydajnej produkcji. Modułowa budowa oraz szerokie możliwości adaptacji do różnorodnych receptur, stanowią realne wsparcie dla zakładów produkcyjnych poszukujących sprawdzonych i skalowalnych rozwiązań procesowych.
Inżynieria procesowa z doświadczeniem
Spotkaj się z nami na targach Drinktec 2025 i porozmawiajmy o Twoich projektach
Odwiedź nas w dniach 15–19 września na targach Drinktec 2025 w Monachium i zobacz najnowszą wersję naszego systemu rozpuszczania i dozowania komponentów sypkich. Rozwiązania Ruland znajdują zastosowanie we wszystkich segmentach branży napojowej – od napojów bezalkoholowych, soków i koncentratów owocowych, przez produkty mleczne i roślinne, aż po napoje energetyczne, syropy i premiksy. Skorzystaj z okazji, aby porozmawiać z naszymi ekspertami o innowacyjnych technologiach procesowych – funkcjonalnych, efektywnych i precyzyjnie dostosowanych do indywidualnych potrzeb Twojego zakładu.