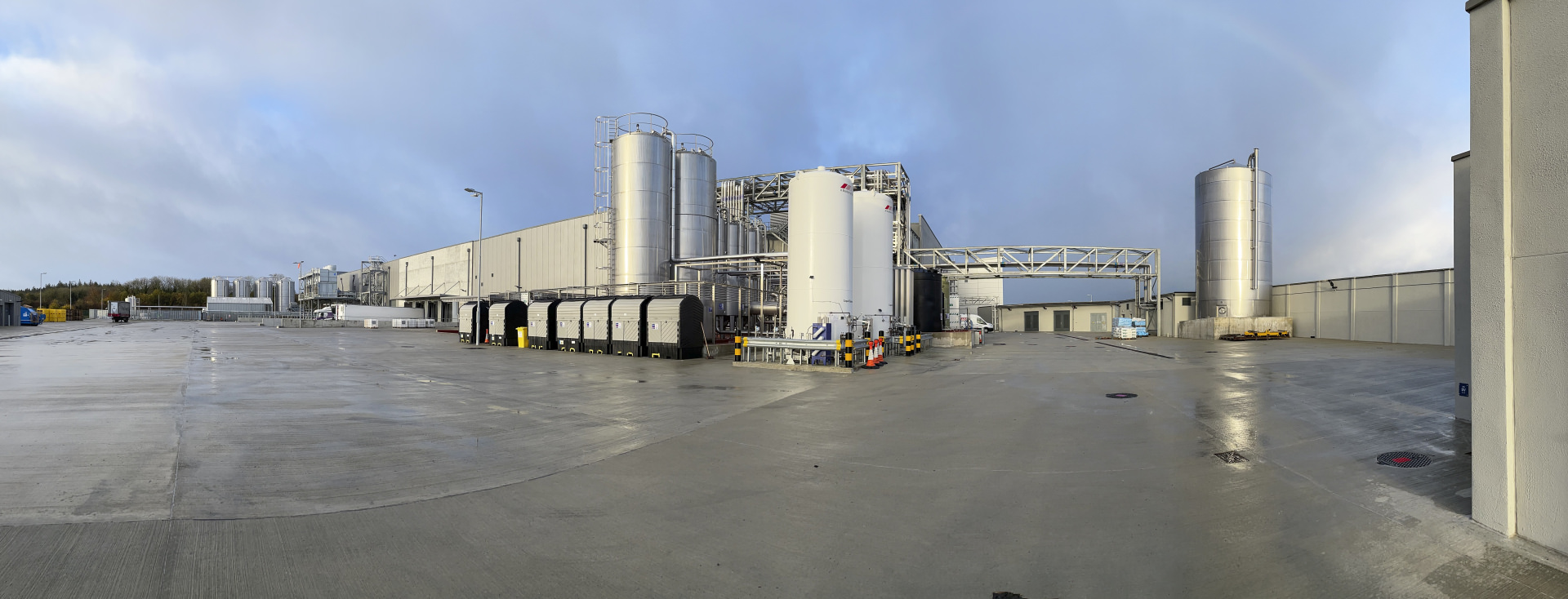
Raport z projektu
Glanbia Cheese
Nowy zakład do produkcji sera mozzarella
Transport płynów w nowej fabryce mozzarelli
Budowa instalacji i rurociągu do transportu uniwersalnego produktu mlecznego
Grupa kapitałowa obejmująca Glanbia Cheese i Leprino Foods otworzyła nowy zakład do produkcji mozzarelli w Portlaoise w Irlandii. Zakład wykorzystuje opatentowane i dedykowane procesy zaprojektowane tak, aby umożliwić produkcję receptur dostosowanych do potrzeb klientów. Mając na celu spełnienie rygorystycznego standardu jakości, wymagania w stosunku do wszystkich dostawców były bardzo wysokie, a szczegóły wdrożenia niezwykle trudne. Podczas pandemii COVID-19, liczni wykonawcy z całego świata koordynowali duży, ruchliwy plac budowy z rozbudowanymi obiektami. Jako specjalista w dziedzinie produktów płynnych, producent instalacji Ruland Engineering & Consulting GmbH przewodził planowaniem, projektowaniem i realizacją większości zaopatrzenia w media dla procesów produkcyjnych, jak również budową kompletnych modułów instalacji wymaganych w sektorze przetwarzania płynów.
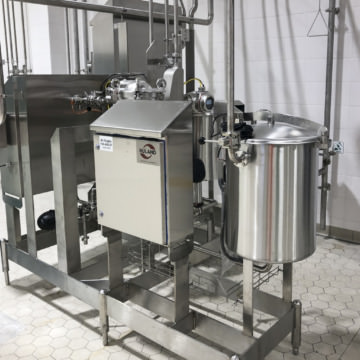
Higieniczne projektowanie, aby sprostać najwyższym wymaganiom
Staranne planowanie projektu zaczyna się od inżynierii podstawowej
Podczas wizyty w jednej z ich głównych fabryk w Ameryce Północnej, Leprino i Glanbia Cheese przedstawiły wszystkim potencjalnym dostawcom swoje wysokie wymagania w zakresie higienicznego projektowania. Klient ten stosuje całościowe podejście z jasno określonymi specyfikacjami i wymaganiami dotyczącymi projektu budynku, procesu, użytych komponentów oraz higienicznego projektowania modułów procesowych i instalacji elektrycznej we wszystkich obszarach. Po wizycie w USA zespół projektowy dokładnie znał oczekiwania klienta wobec nowego zakładu produkcyjnego w Irlandii. Nawet według producenta instalacji Ruland, który uważa się za eksperta w dziedzinie higienicznego projektowania i wykonywania, dbałość o szczegóły w realizacji tego projektu była imponująca i niecodzienna dla producenta żywności. W oparciu o swoje wieloletnie doświadczenie, inżynierzy Ruland zdołali jeszcze bardziej zoptymalizować pewne szczegóły. W 2017 roku projekt r rozpoczął się od intensywnej fazy inżynierii podstawowej. Firma Ruland była odpowiedzialna za obszary mediów procesowych. Oszacowała przewidywane zużycie wszystkich wymaganych mediów, z uwzględnieniem usług budowlanych, w wykresie z 20 tys. komórek. Zespół projektowy ocenił wszystkie dane, określił potrzeby i odpowiednio zaprojektował urządzenia. Dodatkowo, spontaniczna zmiana z klasycznej dostawy energii na zespół kogeneracyjny w celu zaoszczędzenia kosztów energii i zasobów, została uwzględniona ze wszystkimi konsekwencjami. Przed rozpoczęciem szczegółowego planowania, firma Ruland przeprowadziła wspólnie z klientem rozruch poszczególnych jednostek, w ten sposób zespół mógł skupić się na inżynierii szczegółowej głównego zadania.
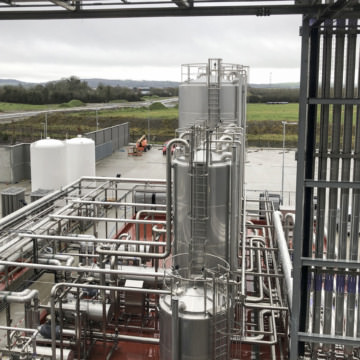
Wyposażenie techniczne zakładu produkcyjnego
Projekt i dostawa systemów i instalacji rurociągowych
Dalszy zakres realizacji firmy Ruland obejmował dwa główne obszary: projekt i dostawę instalacji, jak również kompletny projekt rurociągów i montaż na miejscu dla całej fabryki. Firma Ruland zapewniła dużą część wyposażenia technicznego całego projektu. Technicy Ruland prefabrykowali i okablowali wszystkie części instalacji w Neustadt i uruchomili je na miejscu, w tym:
Stacja wodna wraz z dziennym zbiornikiem buforowym i uzdatnianiem wody, oddana do eksploatacji na miejscu | Przygotowanie oraz doprowadzenie ciepłej i zimnej wody dla całego zakładu | Moduł dozujący do wszystkich składników płynnych | Centralna stacja CIP (ang. Cleaning in Place – czyszczenie na miejscu) do zasilania wszystkich instalacji procesowych ze zbiornikami (do objętości 100 m3) i pięć obwodów z przyłączem DN150. Instalacja oczyszczania CIP została zaprojektowana i zamontowana na zewnątrz ze względu na jej wysokość i odpowiednie warunki klimatyczne | Magazyn zbiorników na chemikalia, w tym zbiorników na kwas i ług | Stacja dozująca do dalszych chemikaliów | Różne obwody regulacji temperatury dla instalacji procesowej | 28 stacji mycia pod wysokim ciśnieniem w specjalnej konstrukcji higienicznej w tym stacja zasilania | Elektryczne szafy sterownicze do wszystkich modułów Ruland
Szczegółowy plan rozkładu rur wspomaga późniejszą realizację
Dzięki rysunkom 3D i BIM, projekt nabiera życia
Pierwszy projekt całego orurowania fabryki opierał się na tablicy klienta i planie przestrzennym zakładów. Następnie inżynierowie zaplanowali sieć rurociągów i zaprojektowali model 3D, na którym przedstawiono wszystkie trasy rur i kabli, jak również przebicia ścian i sufitów. Wraz z architektem i firmą budowlaną realizującą projekt, firma Ruland zintegrowała dane 3D w cyfrowy model o nazwie BIM (ang. Building Information Modelling – modelowanie informacji o budowaniu). Za sprawą tego modelu każda jednostka miała wgląd w aktualny status budowy. Dzięki temu kompleksowemu planowaniu 3D, architekt, firma budowlana, kierownictwo budowy Ruland i wszyscy inni dostawcy sprzętu mogli jasno określić i omówić ewentualne problemy w obszarach współdziałania. Dodatkowo, dzięki BIM, wszyscy mieli jasną wizję tego, jak będzie wyglądała fabryka w późniejszym czasie i mogli kontrolować oraz optymalizować przebieg prac.
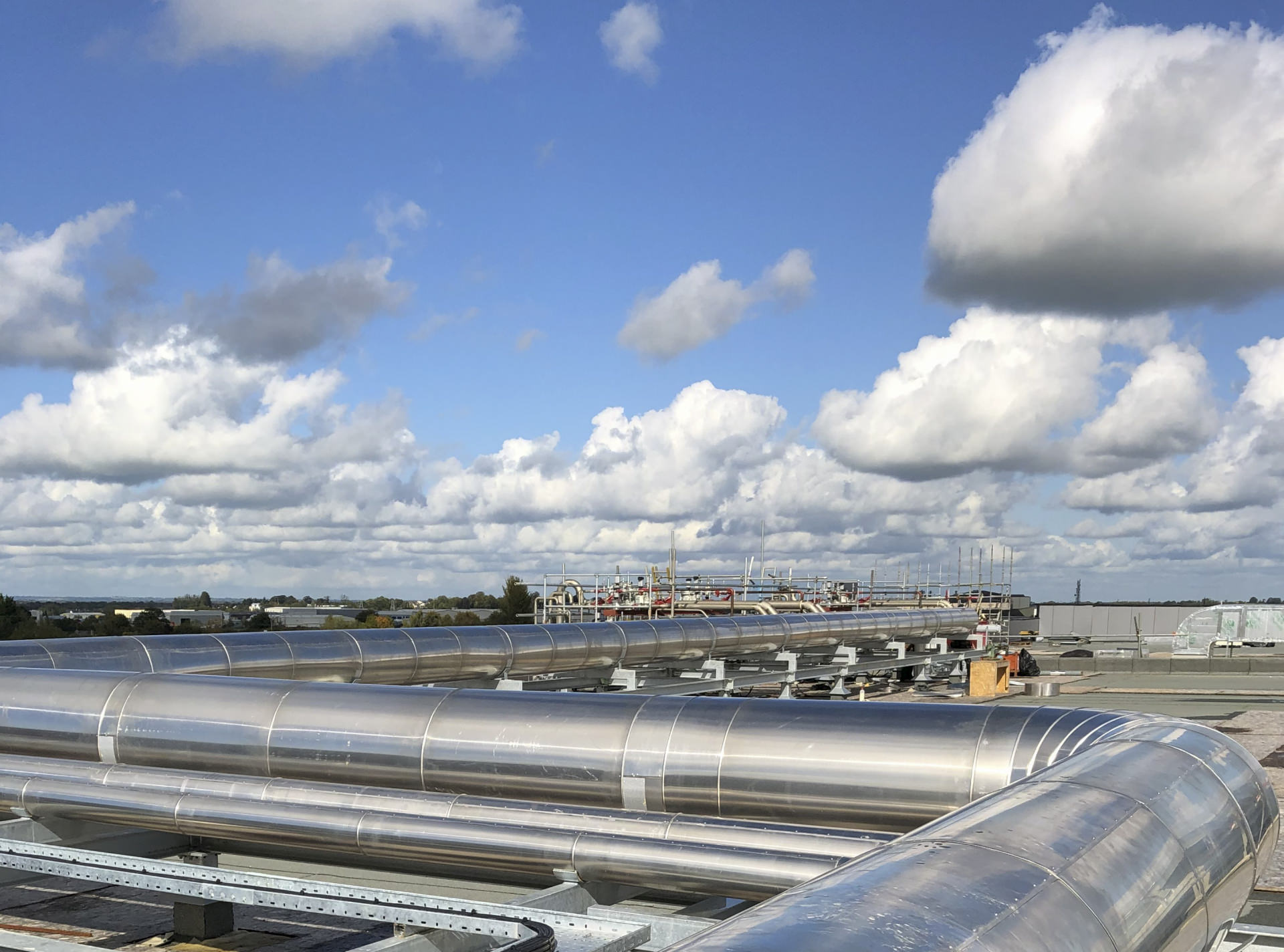
W sierpniu 2019 r. zespół rozpoczął od realizacji i organizacji placu budowy. Axel Steinbach, nadzorca, powiedział: „Dzięki modelowi BIM i bardzo kompetentnym technicznie osobom kontaktowym po stronie klienta możliwe było znalezienie rozwiązań dla pojawiających się problemów bez komplikacji i w krótkim czasie. Drobne błędy, które ujawniły się dopiero na miejscu zostały szybko usunięte. Układanie tras rur i kabli w niskim podwieszanym suficie było szczególnie trudne. Musieliśmy wymyślić na to sprytne rozwiązanie.” Klimat Irlandii był również wyzwaniem podczas montażu wielu kilometrów rurociągu zewnętrznego. Dla zapewnienia nienagannego spawania konieczne było chronienie montowanych rur przed wiatrem i pogodą. Zespół zadbał o jakość szwów spawalniczych za pomocą badania endoskopowego. Firma Ruland potrzebowała 500-tonowego dźwigu do podniesienia i odpowiedniego umieszczenia ciężkich suwnic i mostów do rurociągów. Zespół Ruland był również odpowiedzialny za całość instalacji kanalizacyjnej i podłączenie zbiorników na ścieki na miejscu.
Projekt w liczbach
Materiał, siła robocza, zarządzanie projektem
Materiał:
- 30 km materiału rurowego, DN15 – DN300
- 6 000 kolanek
- 1 000 trójników
- 1 000 redukcji
- 10 900 obejm rurowych
- 39 km kabla
- 50 000 opasek kablowych
Siła robocza:
- 22 700 godzin pracy inżynierskiej
- 71 500 godzin pracy montażowe
Realizacja:
- do 60 pracowników na miejscu
- 50 dokumentów do oceny bezpieczeństwa pracy
- 450 szkoleń z zakresu bezpieczeństwa
Plac budowy:
- ok. 25 firm
- ok. 350 osób
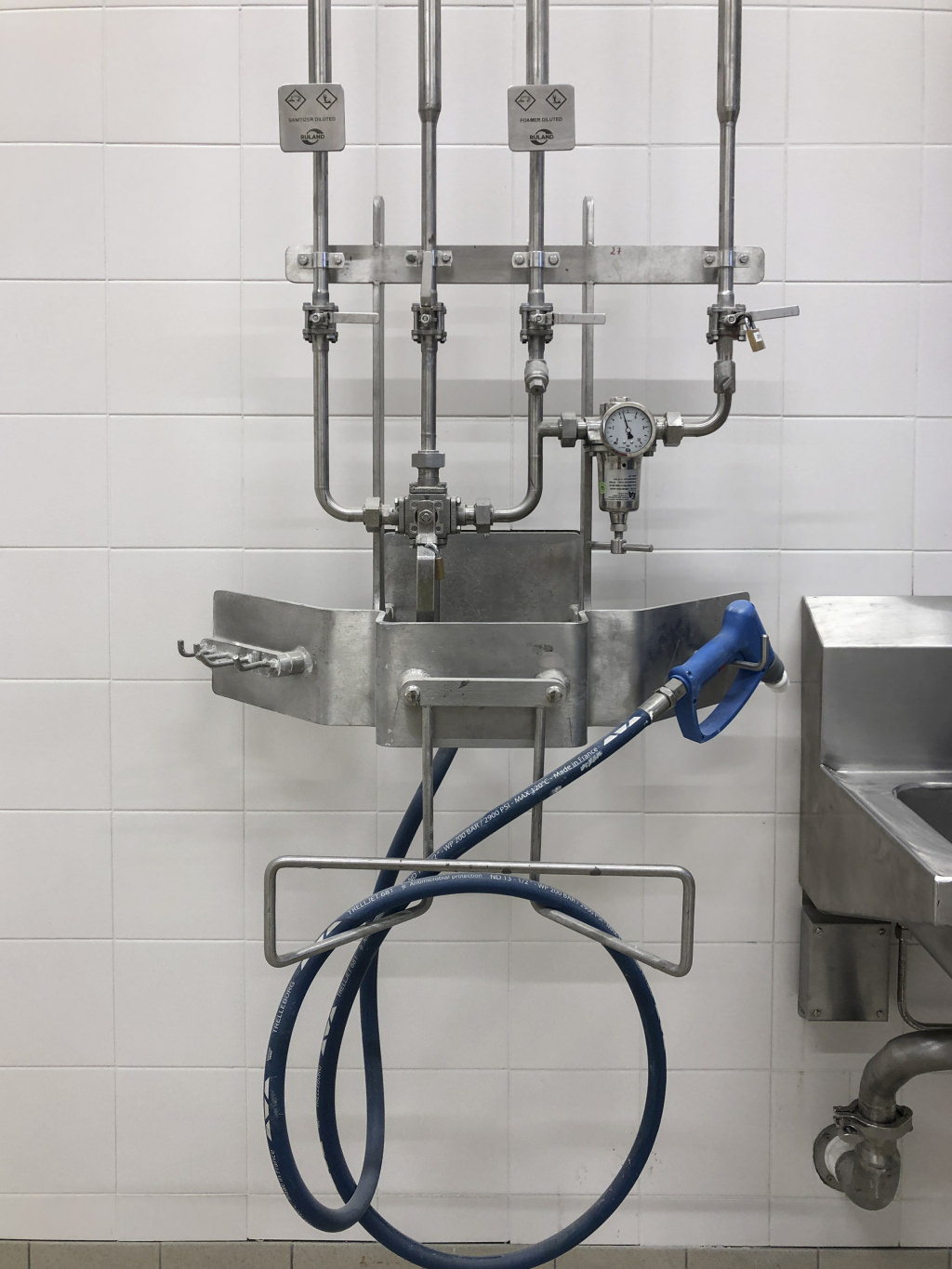
Sposób realizacji pozwolił uniknąć ryzyka zanieczyszczenia w każdym detalu
Higieniczne projektowanie jako specjalne wyzwanie projektowe
W projekcie budynku, Glanbia ściśle rozróżnia strefy o wysokim i niskim poziomie czystości. Odzwierciedla to codzienną produkcję, podczas której poszczególni pracownicy są odpowiedzialni za zadania tylko w jednej strefie higienicznej. W ten sposób można uniknąć czasochłonnych zmian stref. Główne orurowanie znajduje się w suficie podwieszanym typu walk-on nad obszarem produkcyjnym. Uszczelnione otwory rurowe, wychodzące pionowo z sufitu podwieszanego, są dokładnie połączone z modułami instalacji tak, że w obrębie strefy wysokiej czystości prawie nie ma tras poziomych. Dla wszystkich ram w strefie wysokiej czystości, zespół zastosował płaskie profile stalowe, ponieważ ani w ramach modułów, ani w suwnicach rurowych nie było dozwolone stosowanie kształtowników drążonych. Dużym wyzwaniem był również montaż instalacji elektryczno-pneumatycznej. Wszystkie kable prowadzące ze strefy niskiej czystości do głównych szafek i skrzynek stacjonarnych są w zamkniętym systemie przewodów. Kable i węże powietrza są otwarte tylko na ostatnich kilku metrach aż do czujnika lub urządzenia. Oczywiście firma Ruland zastosowała wyłącznie dławnice kablowe ze stali nierdzewnej z certyfikatem EHEDG na wszystkich wlotach i wylotach aż do systemu zamkniętego.
Wymogi specyficzne dla danego kraju determinują dodatkowe wymagania projektowe
Pandemia COVID-19 zaostrza przepisy dotyczące bezpieczeństwa pracy
Bardzo istotnym elementem przedsięwzięcia było przestrzeganie przepisów bezpieczeństwa pracy. Każdy pracownik Ruland musiał ukończyć kurs BHP w ciągu dwóch dni przed wejściem na plac budowy. Dodatkowo wszyscy dostawcy musieli złożyć deklarację bezpieczeństwa w celu zapewnienia bezpiecznego wykonania swoich prac montażowych. Dla każdego pomieszczenia konieczne było również sporządzenie deklaracji dotyczącej metody oceny ryzyka, opisującej z wyprzedzeniem prace i możliwe zagrożenia, a także odpowiednie środki pozwalające ich uniknąć. Ogromnym wyzwaniem dla realizacji projektu był wybuch pandemii COVID-19. Na szczęście po krótkiej przerwie udało się wznowić prace na budowie, z zachowaniem ścisłej 14-dniowej kwarantanny i po dodatkowym szkoleniu online i na miejscu. Zespół mógł pracować tylko z zachowaniem minimalnej odległości około 2 metrów, przy jednoczesnym stosowaniu ochrony ustno-nosowej i myciu rąk co 3 godziny. Dzięki tym działaniom możliwe było kontynuowanie prac na budowie i zakończenie rozruchu systemu na końcu 2020 roku. Po wykonaniu drobnych pracach uzupełniających, zespół zakończył projekt w marcu 2021 roku.
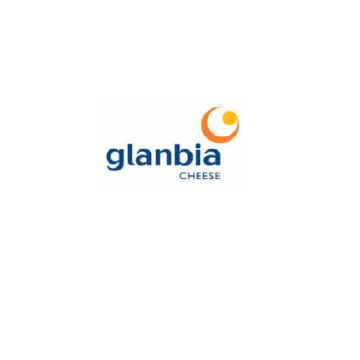
Opinia Klienta
"Dostarczenie tego projektu zgodnie z naszymi rygorystycznymi wymogami w trudnym do zachowania terminie wymagało najwyższego poziomu profesjonalnych kompetencji od wszystkich wykonawców projektu.
Firma Ruland Engineering & Consulting GmbH zaoferowała dokładnie taki poziom wiedzy i skalę działania, aby spełnić wymagania dotyczące zarówno inżynierii projektowej, jak i instalacji procesowej projektu. Wspólny pogląd na to, co można uznać za „znakomite”, otwarta i pełna zaufania relacja między obiema stronami, a także wysoce wykwalifikowany personel sprawiły, że było to satysfakcjonujące doświadczenie. Z przyjemnością mogę polecić Ruland jako firmę, która dąży do doskonałości w swojej specjalizacji w zakresie zaspokajania przyszłych potrzeb przemysłu spożywczego ” – powiedział Conor O’Donovan – Dyrektor ds. Technicznych Glanbia Cheese Ltd.
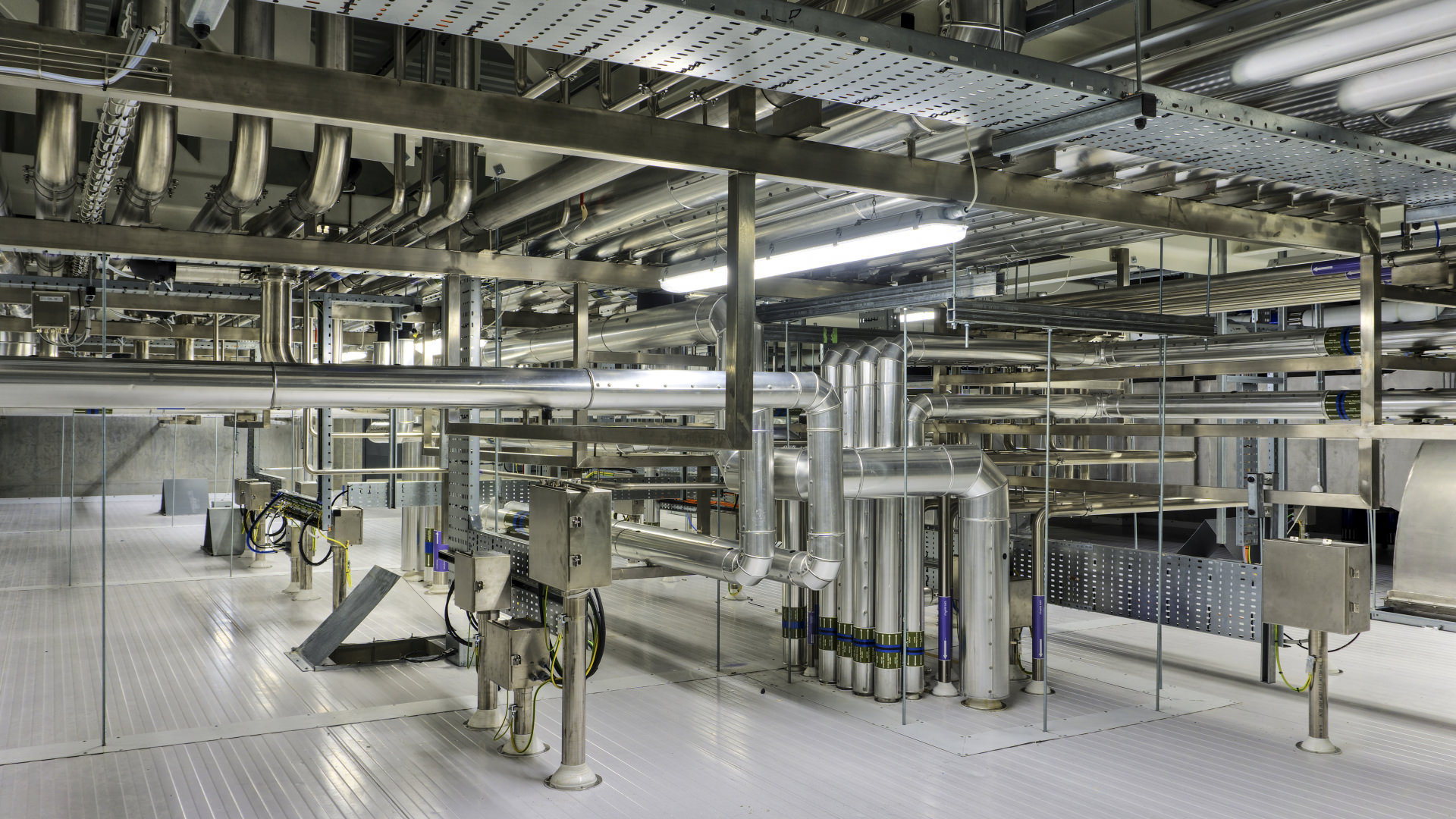
Higieniczne projektowanie dla firm
Chcesz dowiedzieć się więcej o naszym doświadczeniu w zakresie inżynierii i budownictwa międzybranżowego oraz o naszych ogólnofirmowych koncepcjach dotyczących higienicznego projektowania?
Czekamy na Twój telefon lub e-mail!