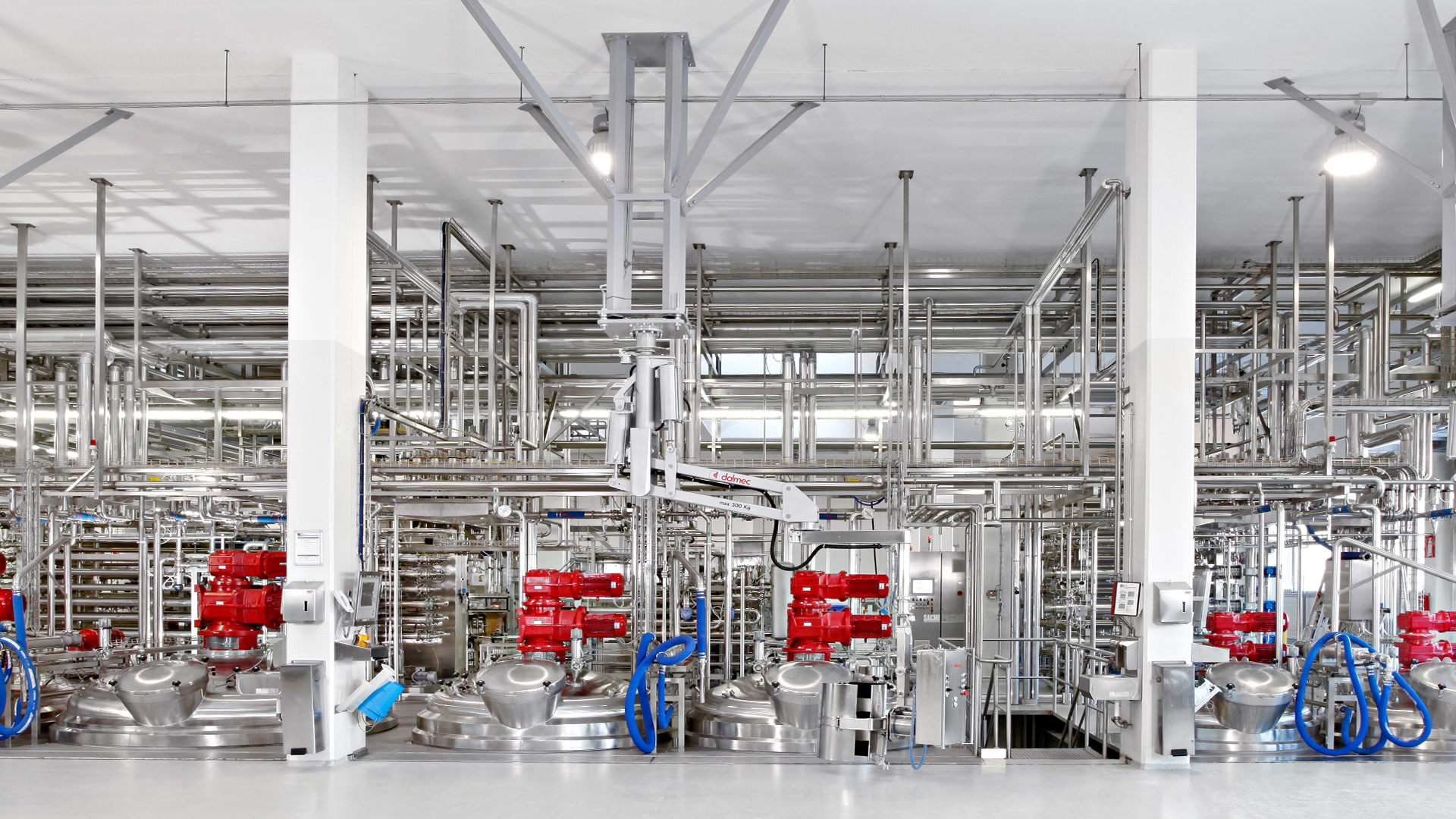
Projektbericht
Prozesslinie für Fruchtverarbeitung und -veredelung
Iprona AG
Ausstattung eines neuen Werkes mit Prozessanlagen
Für die Iprona AG realisierte Ruland das Projekt "Prozesstechnik für das neue Werk". Das Projekt wurde in zwei Phasen umgesetzt: Consulting und Realisierung.
Consulting
Nach Jahren starken Wachstums wurde 2005 mit dem Bau einer neuen Produktionsstätte in Lana, Italien begonnen. Um herauszufinden, welches Vorgehen für das Projekt am besten wäre, entschied sich Iprona zunächst für ein Consulting. In der ersten Phase ging es um die Erstellung eines Grobkonzeptes, das in einer zweiten Phase in das Feinkonzept/Detailengineering münden sollte. Zu Beginn wurde die aktuelle Produktionsweise aufgenommen und ein Blockdiagramm erstellt, das den gesamten Materialfluss von der Rohwarenannahme/-lagerung bis zu den Fertigproduktlinien enthält. Die Ist-Aufnahme und die Detailgespräche wurden von Beginn an gemeinsam mit dem Iprona-Projektteam durchgeführt. Dazu gehörte die Werks-/Produktionsleitung sowie Mitarbeiter aus Technik, Qualitätssicherung, IT und Produktion. Die Einbindung der Produktionsmitarbeiter hat sich als sehr wichtig erwiesen, denn dadurch konnte deren immenser Erfahrungsschatz einfließen. Darüber hinaus konnten die Produktionsmitarbeiter die neuen Verfahren und Bedienkonzepte mitentwickeln und standen deshalb voll und ganz hinter den geplanten Neuerungen. Zum Ruland-Projektteam gehörten ein Senior Consultant, ein Projektingenieur und Ingenieure aus den Bereichen Rohrleitungsplanung und Automation.
Detail-Planung
Auf Basis des Blockdiagramms hat dieses Team nach und nach die einzelnen Bereiche als Verfahrensfließbilder (RI-Schema) entwickelt. Die RI-Schemata wurden in Detailgesprächen mit der Iprona AG immer weiter verfeinert. In dieser Planungsphase ging es um die eindeutige Beschreibung der Prozesse, noch nicht um die exakte Auslegung der Komponenten (Nennweite, Fabrikat, Anschlüsse, etc.). Für Teilbereiche wurden unterschiedliche Bedienungs- bzw. Automatisierungskonzepte ausgearbeitet, vorgestellt, gemeinsam diskutiert, bewertet und entschieden. Im Bereich des Saft-Tanklagers führte dies weg von der zunächst favorisierten Ventilknotenlösung hin zu einer komplexen, aber dennoch bedienerfreundlichen, Rohrzaun-Lösung. Bereits in dieser frühen Phase wurde die 3D-CAD-Planung eingesetzt, was sich als sehr hilfreich erwiesen hat. Speziell bei den Bedienern der zukünftigen Anlagen war der Wiedererkennungswert ihrer Abläufe dadurch sehr hoch. Zum Consulting-Umfang gehörte auch eine einfache 2D-Rohrtrassenplanung. Die Planung erfolgte für alle Medien, um Kollisionen bei der Trassenführung der unterschiedlichen Gewerke zu vermeiden. Nach dem Consulting erhielt Ruland direkt den Zuschlag für die Umsetzung der Planung.
Produktionsverfahren
Die Iprona AG verarbeitet sowohl frische als auch tiefgefrorene Früchte, die zuerst zu sogenanntem Muttersaft verarbeitet werden. Die Früchte werden gepresst und in weiteren Verarbeitungsschritten zu klaren oder naturtrüben Säften verarbeitet bevor sie nach einer Kurzzeiterhitzung in 30 m3 großen Steriltanks eingelagert werden. Die Bandbreite der verarbeiteten Rohstoffe/Ausgangsmaterialien ist hierbei sehr groß und geht von Honigmelonen über Waldbeeren (Erdbeere, Brombeere, Johannisbeere u. a.) bis hin zu Holunderblüten. Der Muttersaft kann in zwei verschiedenen Anlagen aufkonzentriert werden. Zum Einsatz kommen eine thermische Konzentratanlage und eine Gefrierkonzentratanlage. Auf den Fertigproduktlinien werden die Hauptprodukte wie Pulp-, Püree- und Saftkonzentrate, auch mit Fruchtstücken und –kernen individuell nach Kundenwünschen in Mischtanks verschiedener Größen ausgemischt. Danach über Anlagen unterschiedlicher Wärmetauscherarten pasteurisiert und aseptisch abgefüllt werden.
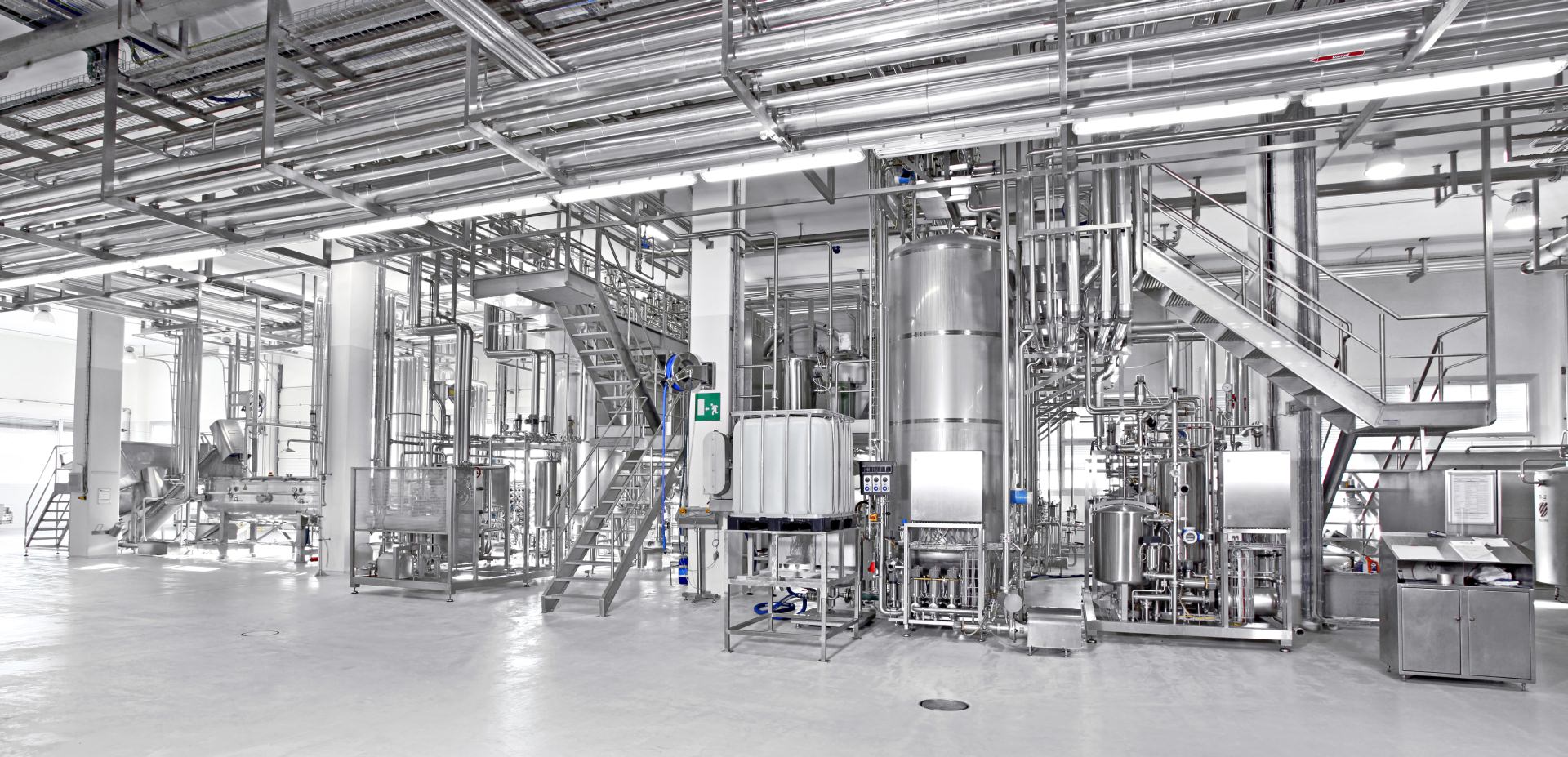
Realisierung
Ruland war für alle Bereiche der Produktion, angefangen von der Saftherstellung, dem Safttanklager, der Einbindung von bestehenden Konzentratanlagen bis hin zu den Fertigproduktlinien und der Versorgung aller Anlagen mit CIP-Reinigungsmedien verantwortlich. In der Consultingphase wurde festgestellt, dass aufgrund des bereits fertig gestellten Gebäudes in einigen Bereichen Kompromisse eingegangen werden müssen. Um eine ergonomische Bedienhöhe zu erreichen wurden die Mischtanks tiefer, in ein Zwischengeschoss, gesetzt. Der Einsatz von Koaxialrührwerken in den Mischtanks gewährleistet einen homogenen Ansatz für die folgenden kontinuierlichen Pasteurisationsprozesse. Je nach Chargengröße und Produktanforderung kann die Fahrweise über Platten- oder Kratzwärmetauscher gewählt werden. Das ermöglicht eine große Flexibilität. Der jeweils gewählte Produktionsweg ist leckagesicher, sodass auf parallelen oder kreuzenden Wegen zeitgleich andere Produkte oder Reinigungen laufen können. Diese Flexibilität wird über Sterilventilknoten auch bei der aseptischen Abfüllung von Bag-in-Box, Bag-in-Drum oder Edelstahl-Transportcontainern sichergestellt. Auch innerhalb einer Charge kann problemlos auf ein anderes Abfüllsystem gewechselt werden. Zur Reinigung der Produktionsanlagen baute Ruland zwei zentrale CIP-Anlagen. Fertigproduktlinien und Saftherstellung sind somit auch über die Reinigungsmedien strikt getrennt, Verschleppungen ausgeschlossen. Dem hohen Qualitätsanspruch der Iprona AG wird damit Rechnung getragen. Über eine Matrix wurden die insgesamt 13 Reinigungskreisläufe so verteilt, dass wenig Überschneidungen bei der Reinigung in den unterschiedlichen Bereichen vorkommen und eine maximale Effektivität für die Produktion erreicht wird. Wirtschaftlich sinnvoll war, vorhandene Tanks für eine CIP-Anlage umzubauen und wieder einzusetzen. Neben diesen Bereichen wurde ein Konzept zur energetischen Nutzung anfallenden Brüdenwassers aus der thermischen Konzentratanlage umgesetzt.
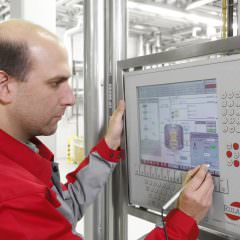
Anlagensteuerung
Um die komplexen Prozesse durchgängig zu steuern und einheitlich zu bedienen wurde das Prozessleitsystem PCS7 von Siemens eingesetzt und mit einem von Ruland entwickelten MES-System, das die Schnittstelle zwischen dem ERP-System der Iprona AG und dem Prozessleitsystem bildet, kombiniert. Alle notwendigen Daten werden damit vom Kunden-Auftragssystem übernommen, im MES-System zu Produktionsrezepten überarbeitet und anschließend mit den entsprechenden Produktions- und Reinigungsparametern der Prozesssteuerung übergeben, wobei die Parameter individuell auf die verschiedenen Produkte eingestellt und in den unterschiedlichen Rezepten gespeichert sind. Zusätzlich sind alle Komponenten von Unterlieferanten, die über eine individuelle Automation verfügen, über eine von Ruland konzipierte, einheitliche Schnittstelle in das Leitsystem eingebunden. Für den Anlagenfahrer wird durch dieses Konzept eine durchgängige Bedienung und Überwachung aller Anlageneinheiten ermöglicht. Automatisierungsinseln, die sich in Aussehen und Funktionalität unterscheiden und ein ständiges Umdenken des Anlagenfahrers erfordern, werden hierdurch vermieden. Da das System Bausteine zur Prozesssteuerung, Rezeptur- und Auftragsverwaltung sowie zur Chargenrückverfolgbarkeit enthält, ist der gesamte Herstellungsprozess hierarchisch, beginnend bei den Bedienern bis hin zur Unternehmensleitung, jederzeit transparent nachvollziehbar und die tatsächliche Effektivität der Produktionsanlage sichtbar. Von der Auftragssteuerung und Chargenverfolgung in der Leitwarte bis hin zum Sensor und Aktor im Feld ergibt sich eine durchgängige Automatisierungslösung aus einer Hand.
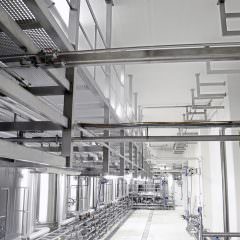
Auf 5 Gebäudeebenen wurden über 50 km Rohrleitungen verlegt. Aufgrund der komplexen räumlichen Situation, wurde das gesamte Projekt in 3D erstellt. Dies und eine frühe, permanente Montagebegleitung seitens der Projektingenieure ermöglichten eine verfahrenstechnisch und in Bezug auf Produktverluste optimierte Verlegung der Rohrleitungen. Durch die sehr enge Kommunikation und den partnerschaftlichen Umgang der Projektteams und Verantwortlichen seitens Iprona und Ruland ist es gelungen, ein sehr großes, komplexes Projekt äußerst effektiv und erfolgreich durchzuführen.
Möchten Sie mehr zum Thema Prozesstechnik wissen?
Schreiben Sie uns.