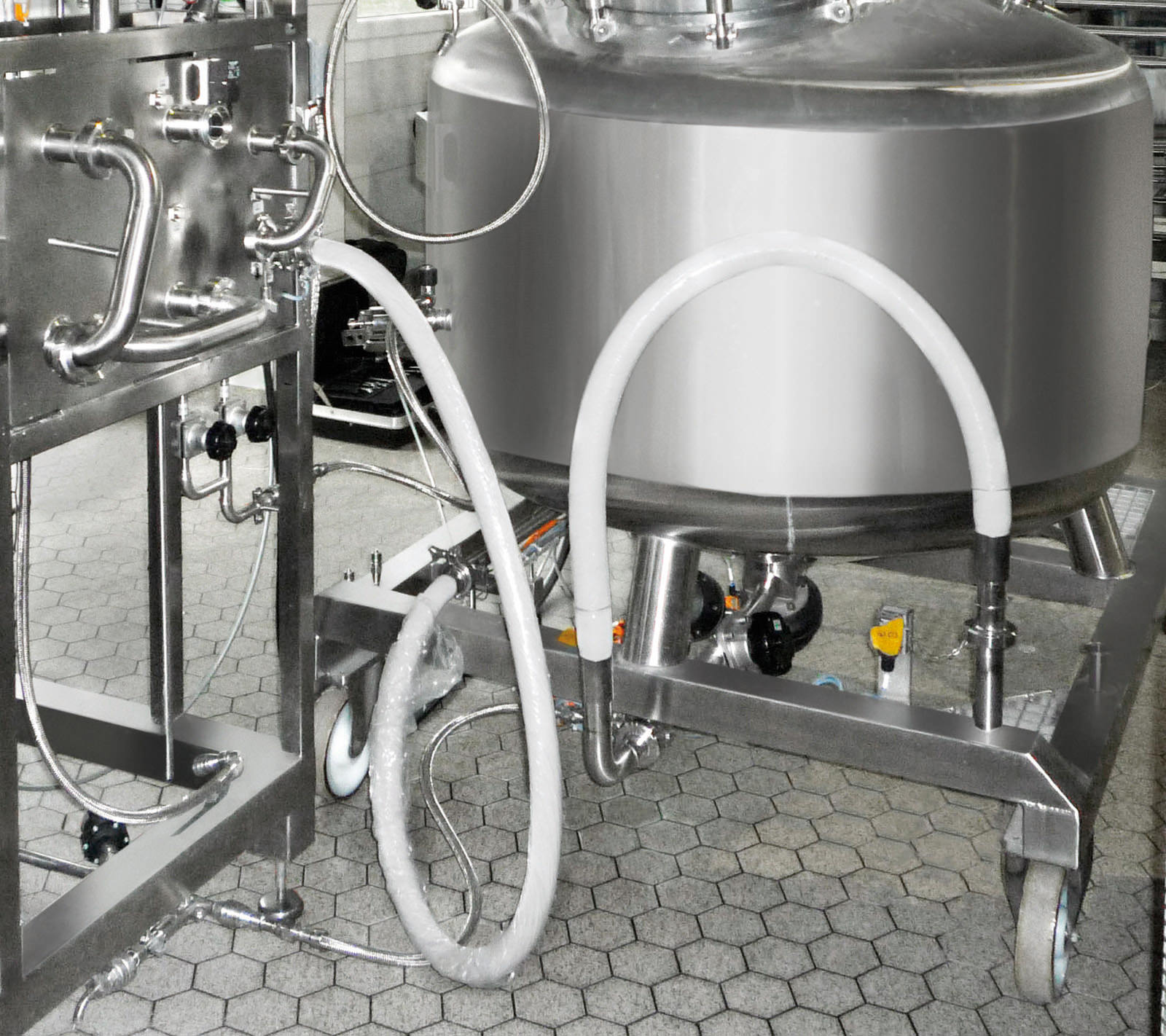
Projektbericht
Kleine Chargen - große Vielfalt
Plantextrakt GmbH & Co. KG
Produktion von anspruchsvollen Produkten in geringen Chargengrößen erfordert optimierte Prozessabläufe
Ruland Engineering & Consulting GmbH in Neustadt verwirklichte für die Plantextrakt GmbH & Co. KG in Vestenbergsgreuth eine Prozessanlage zur Pasteurisation von Kräuter- und Tee-Extrakten. Plantextrakt ist eine Business Unit der Martin Bauer Group und weltweit führend bei der Herstellung von Tee-, Früchte- und Kräuterextrakten sowie entkoffeinierten Schwarz- und Grüntees.
Ein weiteres Geschäftsfeld ist die Herstellung von Teearomen. Insgesamt vertreibt das Unternehmen mehr als 2.000 unterschiedliche Rezepturen auf Basis von über 120 verschiedenen Pflanzen. Für die Erschließung neuer Märkte mit den vorhandenen Produkten wollte Plantextrakt den Produktionsbereich mit Pasteurisation und anschließender aseptischer Abfüllung erweitern. Hierfür hat Ruland mit dem Kunden in einem Consulting-Projekt ein Konzept zur Erweiterung des Produktionsstandorts in drei Stufen erarbeitet.
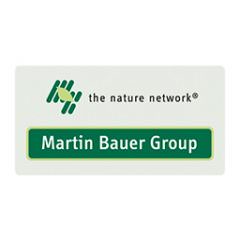
Die spannende Aufgabe in der Consulting-Phase war, die Diskussion mit allen Abteilungen des Hauses Plantextrakt zu koordinieren. Dabei wurden die Vor- und Nachteile der unterschiedlichen Anforderungen aus den verschiedenen Abteilungen ausführlich diskutiert und gemeinsam die Vorgaben an den neuen Produktionsbereich definiert, wie zum Beispiel Qualitätssteigerung durch aseptische Gebinde, kleine Chargengröße, häufige Produktwechsel, hohe Produktviskosität, möglichst geringe Produktverluste.
In der Realisierungsphase für die Standorterweiterung wurde eine neue Werkhalle neben dem bereits bestehenden Ausmischbereich errichtet. Um ein einheitliches Versorgungsmanagement zu ermöglichen, hat Ruland die Energieleitungen und deren Trassen mit Hilfe von 3D-Modellen in das neue Gebäude geplant. Die Möglichkeit späterer Ausbaustufen und eines weiteren Neubaus ist in die Planungen eingeflossen.
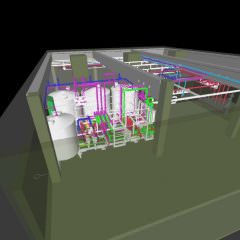
Die realisierte Anlage
Die realisierte Prozessanlage besteht aus einem Erhitzermodul mit Anbindung an den bestehenden Ausmischbereich, einem 6.000-Liter-Steriltank, zwei mobilen Behältern, einer CIP-Anlage, einer kombinierten Doppelstation zur Reinigung und Sterilisation für die mobilen Behälter und einer Doppelreinigungsstation für 1.000-Liter-Kunststoffcontainer. Vom Steriltank oder vom mobilen Behälter werden die Produkte über einen Bag-in-Box-Füller aseptisch abgefüllt. Die Erhitzerlinie der ersten Ausbaustufe wurde als molchfähige Anlage mit einer Leistung von 500 l/h realisiert. Damit wird den Anforderungen aus dem Consulting am Besten Rechnung getragen. Die geringe Produktionsgeschwindigkeit von 500 l/h führt zu einer kleinen Nennweite der Produktleitungen (hier DN 20). Größere Nennweiten würden einen schlechten Wärmeübergang aufgrund der schlechten Strömungsverhältnisse bedingen.
Kleinere Nennweiten würden zu sehr hohen Druckverlusten führen, die sich wiederum in größer dimensionierten Wärmetauschern und Produktpumpen widerspiegeln würden. Zur Auslegung des Wärmetauschers wurden in der Frühphase der Projektierung Versuche an einer Pilotanlage durchgeführt. Viele Produkte der Plantextrakt haben einen relativ niedrigen Wassergehalt (50 bis 65 % Trockensubstanz) und müssen bei der Behandlung in den Prozessanlagen vor einem nachträglichen Eintrag von Frischwasser oder Kondensat geschützt werden. Aus diesem Grund wird das Produkt bei Produktionsbeginn und –ende mit einem Molch in die Erhitzerröhre ein- bzw. ausgefahren. Für die kleineren Leitungsdimensionen wurde eigens ein spezieller Molch entwickelt.
Beschickung für größere Batches oder Kleinchargen
Der Erhitzer kann über zwei Wege beschickt werden. Für größere Batches bis 6.000 Liter stehen im Ausmischbereich Ansatztanks. Von dort wird das Produkt über eine Transferleitung zum Vorlaufbehälter des Erhitzermoduls gefördert. Auch hier ist zur Vermeidung von Mischphasen Molchtechnik eingesetzt. Am Produktionsende wird der Molch mit Druckluft durch die Leitungen geschoben. Auf diese Weise werden Wassereinträge ins Produkt ausgeschlossen, da die Produktleitung zu Transferbeginn und nach Transferende trocken ist. Bei Kleinchargen bis 1.000 Liter können die mobile Behälter im Ausmischbereich befüllt und direkt am Erhitzer angedockt werden. Auf diese Weise werden Produktverluste durch Anhaftungen an Behälterwänden und in Schlauchleitungen zusätzlich weiter minimiert. Die mobilen Behälter sind über eine Schnittstelle mit der Steuerung verbunden und voll automatisiert. Alle produktkritischen Schlauchverbindungen werden von der Steuerung überwacht und über einen Druckaufnehmer werden der Sterilstatus und der Vordruck für die Erhitzerpumpe gesteuert und überwacht. Am Schaltkasten der mobilen Behälter lassen sich die Aktoren auch von Hand schalten. Dies ermöglicht den Einsatz der mobilen Behälter an Orten, an denen keine Verbindung zur Steuerung aufgebaut werden kann (Technikum).
Die mobilen Behälter dienen auch als Steriltanks. Somit können Kleinchargen von einem mobilen Behälter in einen anderen mobilen Behälter pasteurisiert und steril zwischengelagert werden ehe sie zur Abfüllung freigegeben sind. Natürlich kann, wie bei jedem anderen Steriltank, gleichzeitig befüllt und zum Füller hin entleert werden. Für die Reinigung und Sterilisation der mobilen Behälter gibt es eine CIP-/SIP-Station mit zwei Stellplätzen. Hier werden die Behälter vollautomatisch gereinigt und bei Bedarf mit Reindampf sterilisiert. Nach der Sterilisation wird das Kondensat ausgeblasen und die Behälter mit Sterilluft überlagert. Viele Halbwaren für die Produktausmischung werden bei Plantextrakt in 1.000-Liter-Kunststoffcontainern bereitgehalten und teilweise auch in diesen Gebinden an Kunden ausgeliefert. Durch die vielseitige Befüllung der Container ist eine gründliche Reinigung erforderlich, da es ansonsten zu Verunreinigungen bei nachfolgenden Befüllungen kommen kann. Um die Reinigung der Kunststoffcontainer zu standardisieren und zu automatisieren, lieferte RULAND eine Reinigungsstation für zwei Kunststoffcontainer, die an die CIP-Anlage angeschlossen ist und dementsprechend mit allen Medien versorgt werden kann. Die Reinigungsstation ist optional um einen dritten Stellplatz erweiterbar.
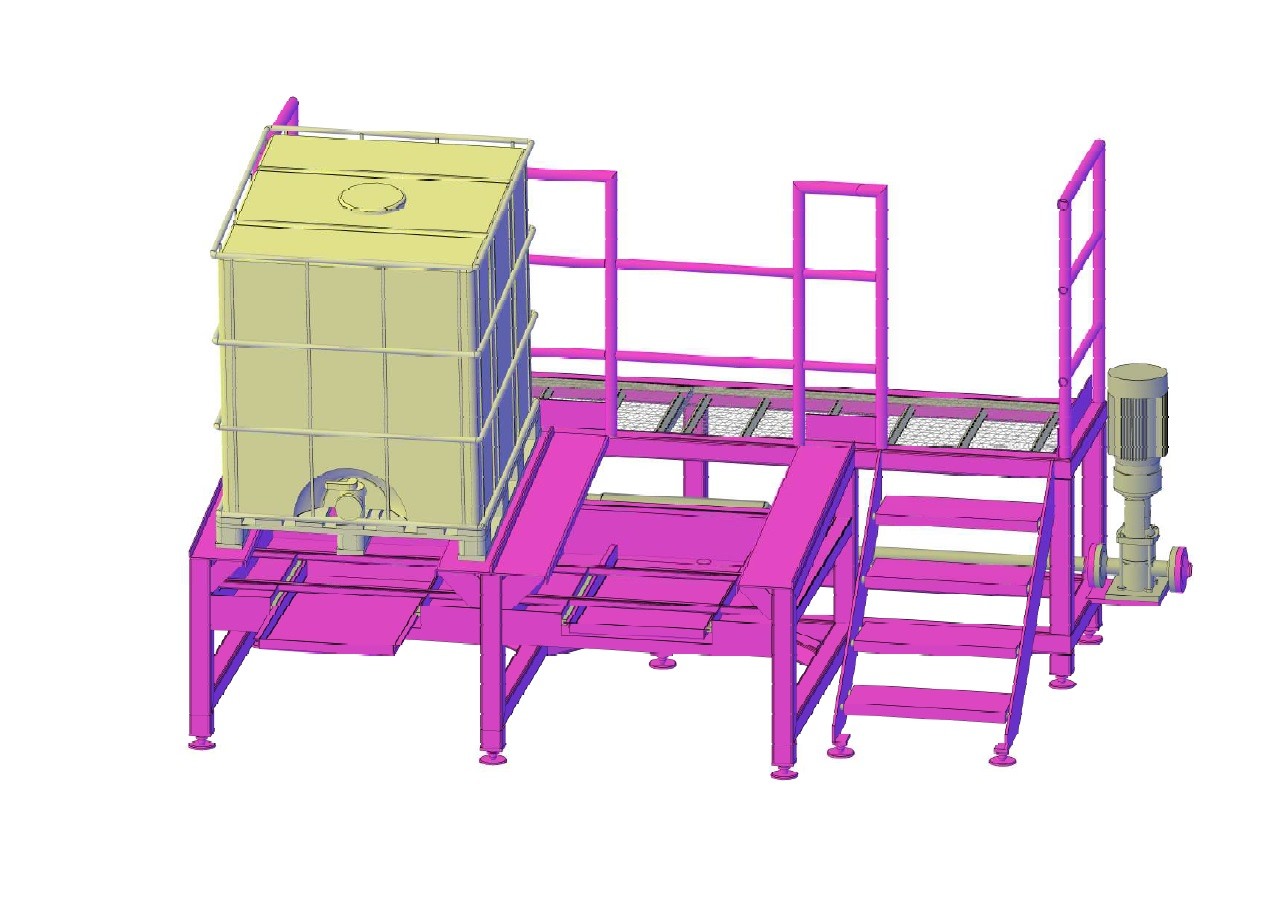
Reinigung und Steuerung der Anlage
Die Vier-Tank-CIP-Anlage mit zwei Reinigungskreisen wird für die Prozessanlagen und die CIP-Stationen der mobilen Behälter und der Kunststoffcontainer eingesetzt. Die Anlage ist auf vier Reinigungskreise erweiterbar. Um für alle Anlagenteile (Erhitzer, Steriltank und Füller) ein optimales Reinigungsergebnis zu erzielen, ist für die Reinigung eine Rezepturverwaltung hinterlegt. Hier können für jede Produktgruppe Rezepte zur angepassten Reinigung hinterlegt werden. Die Überwachung und Bedienung der Anlage erfolgt über einen 19-Zoll-Touchscreen am Erhitzermodul und einen PC in der Leitwarte. Beide Stationen sind redundant zu einander ausgeführt und vereinfachen die Bedienung für das Personal, da sie sich in Aussehen und Funktionalität gleichen. Für die Lebensmittelindustrie ist die durchgängige Protokollierung aller Produktionsschritte ein wichtiger Baustein in der Qualitätssicherung. Die eigentliche Software für die Chargenprotokollierung ermöglicht eine sehr genaue Anpassung an die Bedürfnisse des Betreibers. Bei Plantextrakt werden ab dem Beginn der Sterilisationsprogramme alle Statusmeldungen, Alarme, Bedieneingriffe, festgelegte Schreiberkurven der jeweiligen Charge mit der Auftragsnummer im Archiv abgelegt.
Sie möchten mehr über unser Projekt bei Plantextrakt erfahren?
Schreiben Sie uns.