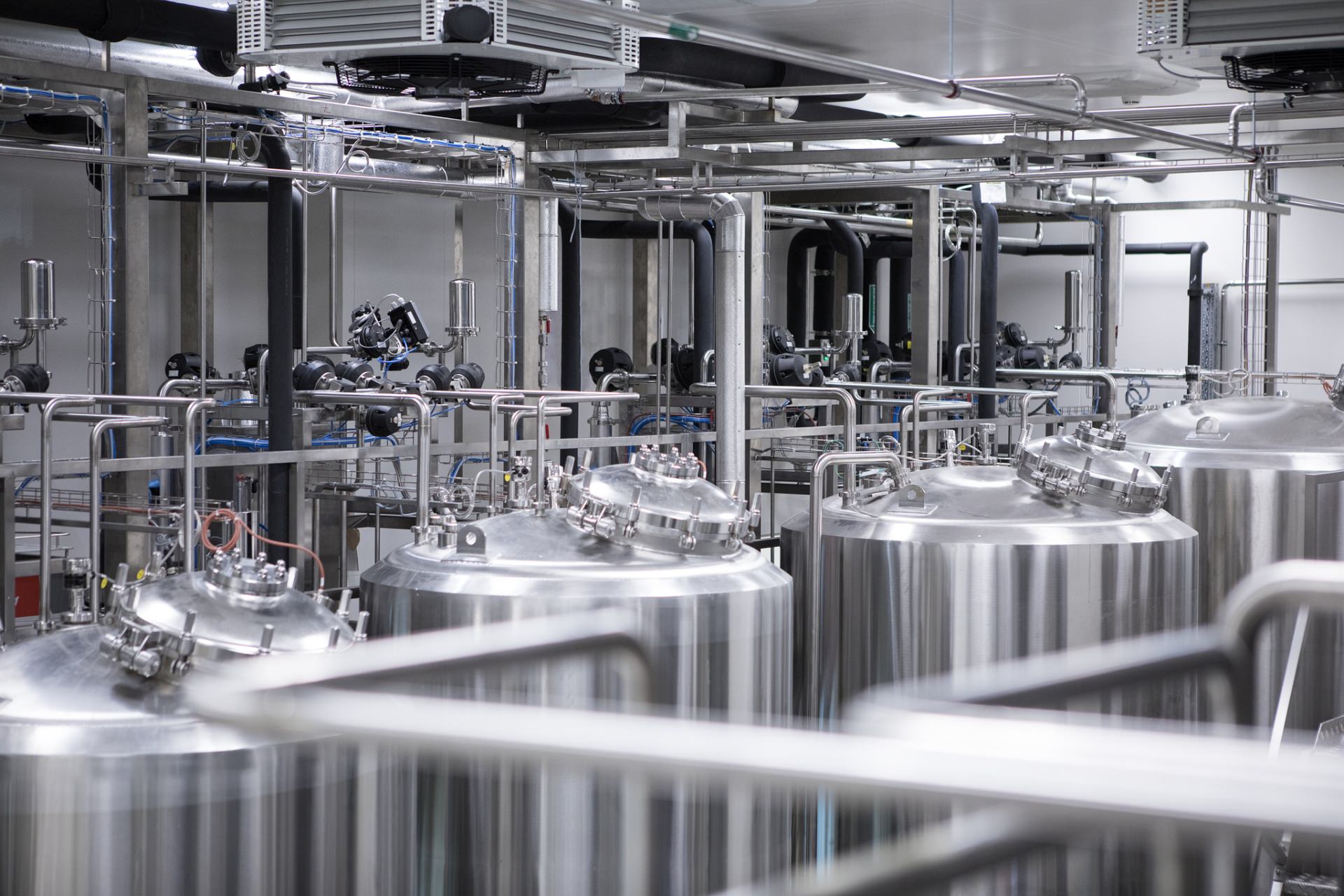
Projektbericht
Biotest AG
Vor- und Zwischenproduktanlagen für IgM Concentrate und polyvalentes Immunglobulin G
Neue Blutplasma-Anlagen für steigende Nachfrage
Vier Produktionslinien für die Biotest AG für die Verarbeitung von Blutplasma
Für die Biotest AG, Spezialist für Hämatologie und klinische Immunologie, hat Ruland vier neue Produktionslinien inklusive Steuerung für die Verarbeitung von Blutplasma geplant, konstruiert und installiert. Für das Investitionsprogramm „Biotest Next Level“ beauftragte die Biotest AG den Anlagenspezialisten mit der Detailplanung und dem Bau der Herzstücke der Erweiterung, den vier Produktionslinien für die neuen Produkte IgM Concentrate und für polyvalentes Immunglobulin G. Dazu gehört eine Vorprodukt-Anlage für beide Produkte sowie drei Zwischenproduktanlagen.
Blutplasma gehört zu den wertvollsten Flüssigkeiten überhaupt, denn aus dem Stoff werden lebensrettende Medikamente hergestellt. Rund 14 Millionen Liter werden laut WHO pro Jahr weltweit verarbeitet – und die Nachfrage steigt. Rund eine Million Liter verarbeitet alleine die Biotest AG in Dreieich. Der Hersteller von Plasmaproteinprodukten wie Immunglobuline, Gerinnungsfaktoren und Albumine hat jetzt seine Produktionskapazitäten auf 2,5 Millionen Liter erweitert. Dazu wurde ein neues Produktionsgebäude mit eigener Energiezentrale errichtet. Im Rahmen der Erweiterung mit einem Investitionsvolumen von rund 250 Millionen Euro sollen zusätzlich zu den 1.600 Mitarbeitern 300 weitere Arbeitsplätze entstehen.
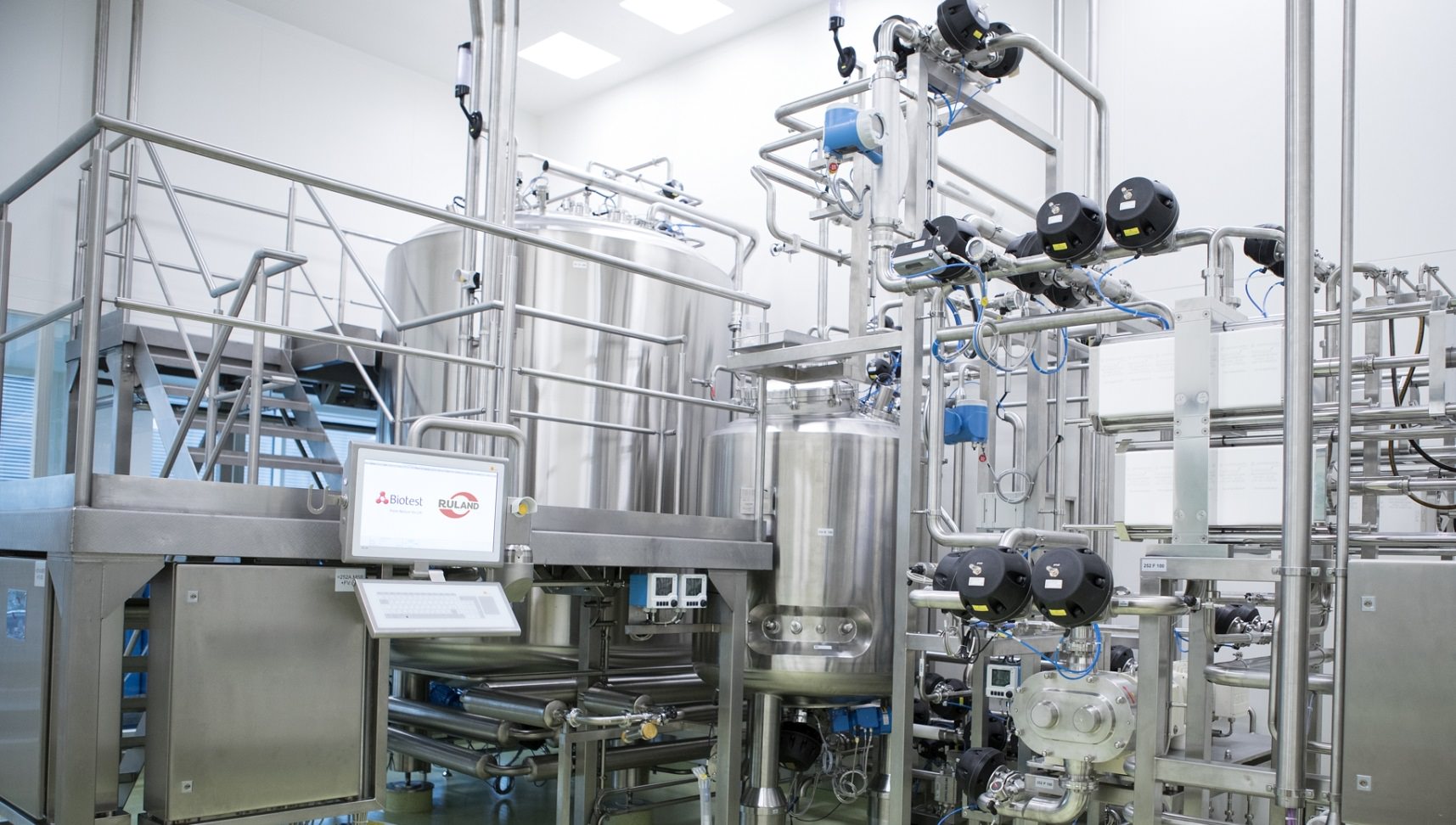
Vier Teilanlagen für die Aufbereitung des Blutplasmas mit verschiedenen Prozess-Schritten
wie Filtration, Virusinaktivierung, Fraktionierung und CIP-Reinigung
Bei dem Großprojekt der Biotest AG waren die Anforderungen wie immer hoch, denn für Prozessanlagen, auf denen Produkte aus Blutplasma verarbeitet werden, gelten die höchsten Qualitäts-, Sicherheits- und Hygienevorschriften. Für eine maximale Produktsicherheit mussten einzelne Teilanlagen strikt getrennt voneinander errichtet werden. Zudem gab es unterschiedliche Reinraumstufen zu beachten. Eine gewisse Flexibilität für künftige Erweiterungen oder Umrüstungen wurde von Anfang an berücksichtigt.
In der von Ruland erstellten Vorprodukt-Anlage wird zunächst die Blutplasma-Paste in eine Suspension überführt und dann über mehrere Filtrationsschritte zu einer Proteinlösung verarbeitet. Es folgt eine Behandlung zur Inaktivierung von Viren. Erst dann wird die Lösung an die Zwischenprodukt-Teilanlage weitergegeben, wo sie zunächst mittels Chromatographie in die zwei Wertfraktionen IgG und IgM aufgetrennt wird. Die beiden Fraktionen durchlaufen danach auf unterschiedlichen Linien weitere Filtrationsschritte wie Ultra-, Dia- und Nanofiltration sowie Chromatographie und UVC-Behandlung. Über ein zentrales Tanklager werden die Linien mit den notwendigen Pufferlösungen versorgt. Mehrere CIP-Anlagen übernehmen die Reinigung der Anlagen.
Dabei stellte Biotest einige Komponenten als Package Units bereit. Beispielsweise Filterpresse, UF-Filterhalter sowie die UVC-Anlage wurden von Ruland vollumfänglich integriert.
Detail-Engineering, Programmierung und Umsetzung
der Anlagen für die Blutplasma-Verarbeitung
Ruland übernahm das verfahrenstechnische Engineering inklusive der Spezifikationen von Soft- und Hardware, Programmierung und Visualisierung sowie die mechanische, elektrische und pneumatische Montage, die Schaltschrank-Konstruktion und die Steuerung samt Anbindung an das SAP-System. Die Design-, Installations- und Funktionsqualifizierung entsprechend der europäischen GMP-Richtlinien, Factory-Acceptance-Tests, die Erstkalibrierung aller Messstellen sowie die Inbetriebnahme und eine ausführliche Dokumentation gehörten ebenfalls zu den Leistungen.
Zu Projektbeginn stand zunächst das Detail-Engineering, das sich am Basic-Engineering, am Lastenheft, am Chargenbelegungsplan sowie am Rohrleitungs- und Instrumenten-Fließschema des Auftraggebers orientierte.
Grundsätzlich ist der Kunde der Experte für seinen Prozess. Umso wichtiger ist die enge Zusammenarbeit schon zu Beginn der Planungsphase. Das Team von Ruland konzipiert, überprüft und detailliert die Anlage, prüft die Auslegung aller Komponenten und erstellt Simulationen, die sämtliche Prozesse abbilden. Eine exakte Visualisierung stellt dann schematisch alle Einzelkomponenten dar, inklusive aller Rohrleitungen, Ventile, Motoren und Schnittstellen.
Bei dem Projekt „Biotest Next Level“ waren unterschiedliche Anlagenbauer involviert. Hier spielte besonders die Kommunikation über den Generalplaner eine große Rolle, denn am Ende müssen alle Anlagenteile perfekt passen, reibungslos miteinander arbeiten und ebenfalls miteinander „kommunizieren“.
Auch während der Umsetzungsphase eines solchen Projekts sind die Anforderungen hoch. Das erfordert vom Anlagenbauer ein hervorragendes Projektmanagement, denn einerseits sind die Anlagen sehr komplex, andererseits arbeiten zahlreiche Teams unterschiedlicher Lieferanten meist auf begrenztem Raum. Jürgen Schütze, Projektleiter bei Ruland: „Wir haben innerhalb relativ kurzer Zeit mehrere Teilanlagen geplant und realisiert. Obgleich eine exakte Planung Voraussetzung ist und die Vorgaben zu 100 Prozent umgesetzt werden müssen, erfordert es doch auch immer wieder Flexibilität, wenn einzelne Bereiche eine kurzfristige Anpassung benötigen. Diesen Spagat haben unsere Mitarbeiter bestens bewältigt, und wir sind sehr zufrieden mit den Ergebnissen.“
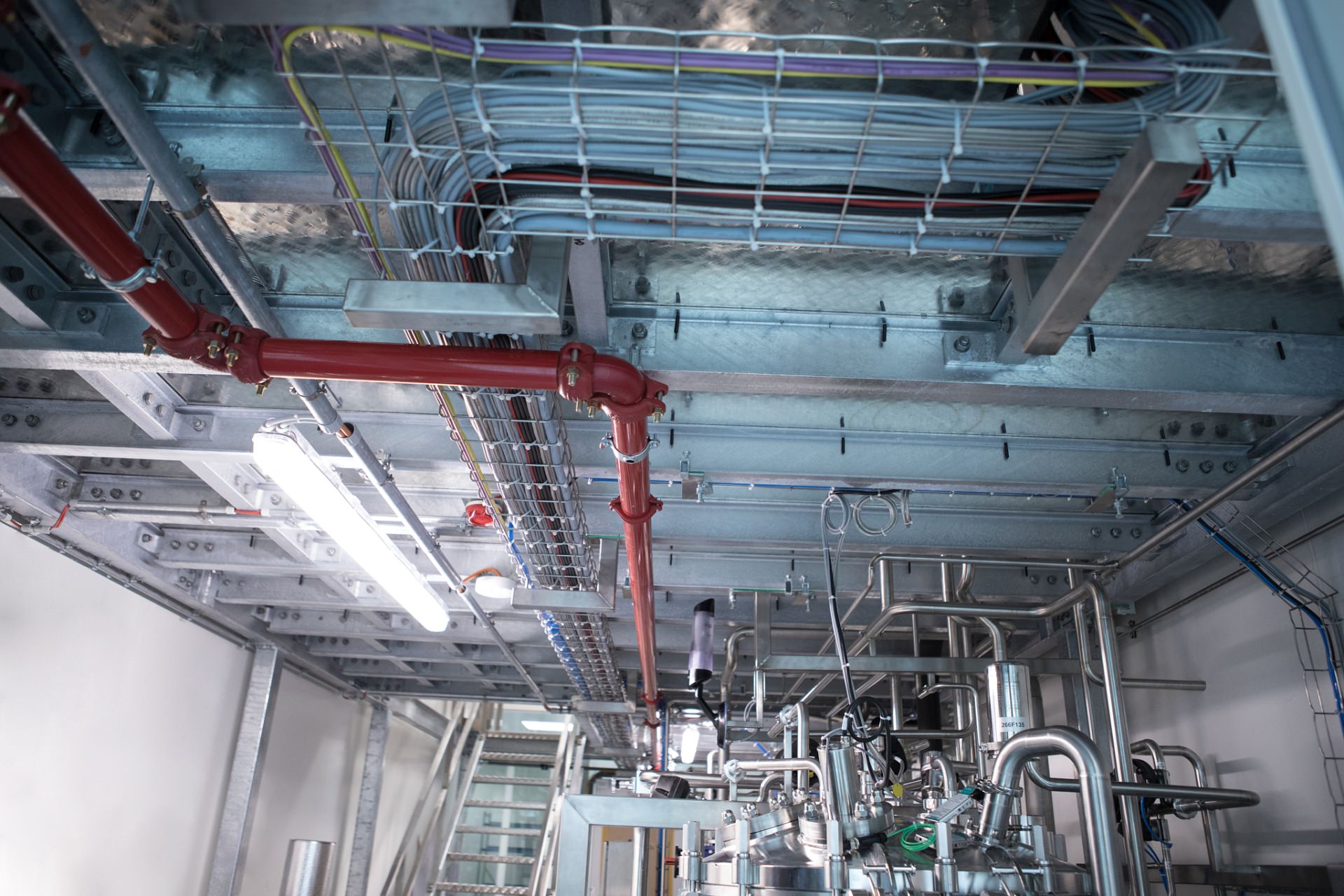
Komplexe Anforderungen bei
Komponenten, Rohrleitungs-Montage, Steuerung und Qualifizierung
Eine große Herausforderung war die schiere Größe des Projekts. Mit rund 3.500 Komponenten, darunter 2.300 automatisierte Ventile, dazu 1.800 Mess-, Steuer- und Regelungs-Komponenten, 100 Pumpen und Rührwerke sowie über 40 Tanks erforderte das Projekt ein großes Team – in Spitzenzeiten waren 35 Techniker und Ingenieure von Ruland bei Biotest im Einsatz. Für die durchgängige Automation der vier eigenständigen Teilanlagen wurden über 30 Last- und Serverschränke und außerdem mehr als 90 dezentrale Schaltschränke für die Anbindung der Ventilinseln und Feldsignale an die acht Siemens-Steuerungen installiert. Auch die Verrohrung beeindruckt: Aus verschiedenen Edelstählen in Pharma-Ausführung, teilweise aus hochkorrosionsbeständigem Hastelloy 22 oder Kunststoffleitungen in PVDF, wurden fast 9 Kilometer prozessführende Rohrleitungen und Medienversorgungsleitungen verlegt. Die 39.000 Schweißnähte wurden pharmagerecht dokumentiert.
Die von Ruland erstellten Teilanlagen erstrecken sich über vier Stockwerke. Insgesamt wurden 24 Reinräume, Technikräume und elektrische Betriebsräume mit dem entsprechenden Equipment ausgestattet. Um einer modernen Arbeitsergonomie sowie strengsten Kriterien der Arbeitssicherheit gerecht zu werden, wurden dazu 10 Pharma-Edelstahlbühnen und 12 Technik-Bedienbühnen geplant und geliefert.
Anlagen zur Plasma-Aufbereitung werden in SAP verwaltet
und das Prozessleitsystem berichtet an SAP
Hoch komplex sind auch die Steuerung und die SAP-Anbindung. Von zwei zentralen Leitwarten aus können sämtliche Prozesse zentral beobachtet und gesteuert werden. Für die vor Ort-Bedienung stehen in den Produktions- und Technikräumen 26 Panel-PC zur Verfügung, die auf 16 Server zugreifen. Für die Sicherheit sorgen personalisierte RFID-Chips: Jeder Benutzer muss sich authentifizieren, damit unerlaubte Zugriffe praktisch ausgeschlossen werden können.
Im Zuge des Investitionsprogramms hat Biotest SAP als zentrale Plattform für die Produktion eingeführt. Das Prozessleitsystem der Teilanlagen wurde zur übergeordneten Prozesskontrolle und Datenaufzeichnung über eine standardisierte Schnittstelle mit SAP gekoppelt. Sämtliche Vorgänge, die im Zuge der Produktion ausgeführt werden können, sind dabei in SAP vorgegeben und werden über Handhelds zunächst geprüft und dann freigegeben. Über einen bidirektionalen Datenaustausch werden zum einen Prozessdaten ausgewertet und archiviert, zum anderen können Informationen direkt in den Herstellprozess einfließen. Erfasst und überwacht werden unter anderem die Prozessaufträge, Batchprotokolle und Materialflüsse. Das System gibt aber auch Wartungs- und Kalibrierungsintervalle vor und überprüft und verwaltet die Berechtigungen der Mitarbeiter.
Damit die Serversysteme maximal verfügbar sind, war eine redundante Serverarchitektur unbedingt erforderlich. Hier setzte Ruland Stratus-Server mit systemintegrierter Redundanz ein.
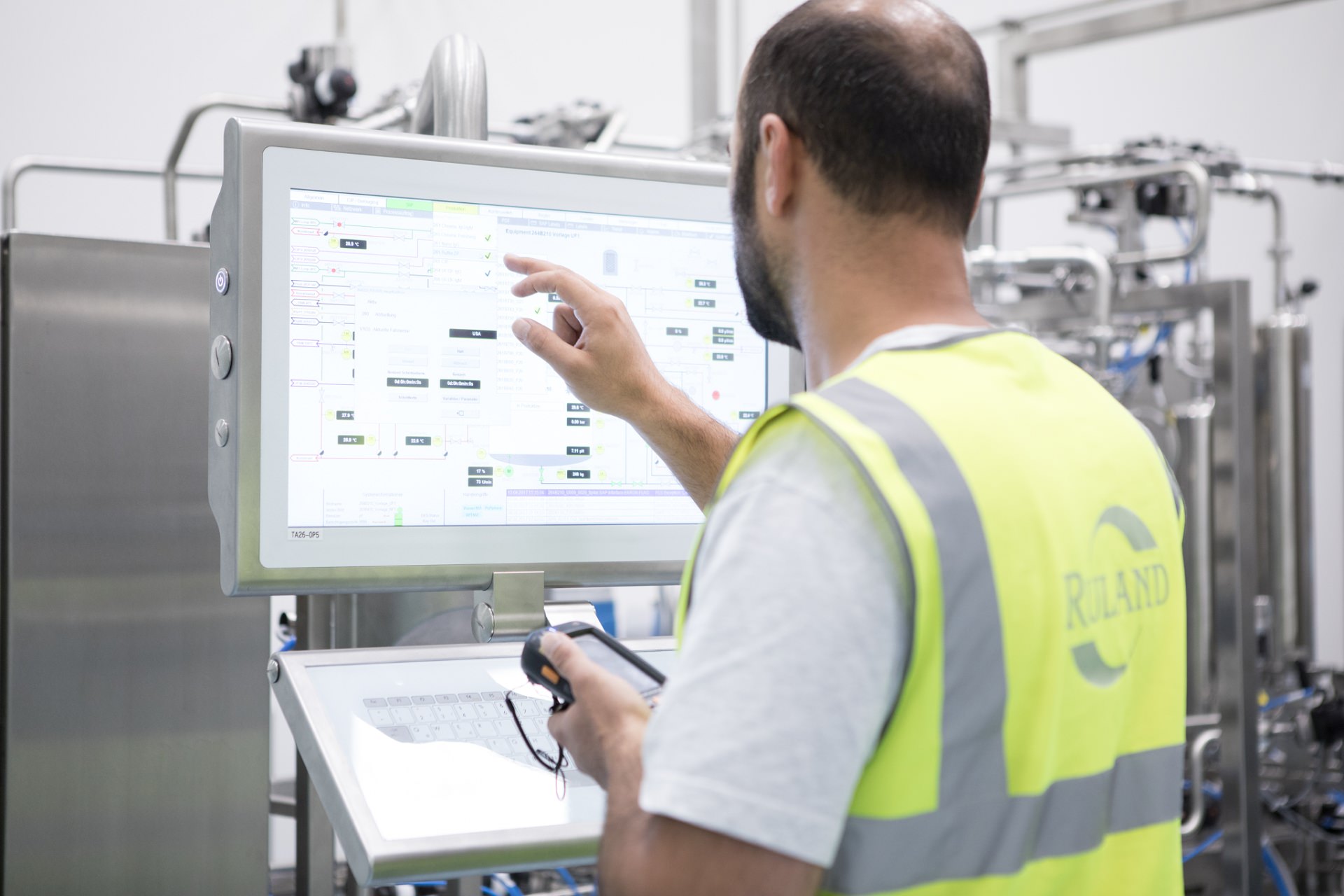
Komplexe Anlagentechnologie für die Produktion der Blutplasma-Produkte
mit flexibler, lösungsorientierter Umsetzung
„In einem so komplexen Projekt ist es unabdingbar, dass sämtliche Beteiligten eng zusammenarbeiten. Insbesondere wenn mehrere Lieferanten Teilprojekte in einem so großen Umfang umsetzen, ist eine gute Kommunikation sowie die Weitergabe von Informationen das A und O“, so Michael Rodemer, Director Technical Project Management, Biotest AG. „Von zuvor realisierten Projekten wussten wir, dass die Ingenieure von Ruland nicht nur ausgezeichnete Arbeit abliefern, sondern auch äußerst lösungsorientiert mit anderen Unternehmen Hand in Hand arbeiten.“ Tatsächlich hatte Ruland im Rahmen des Projekts etliche technische Konzepte und Detaillösungen erarbeitet, die dann von anderen Lieferanten als Umsetzungsvorlage für weitere Teilbereiche genutzt wurden, so zum Beispiel das innovative Reinigungskonzept – welches bei der Produktion pharmazeutischer Blutplasma-Produkte eine ganz herausragende Rolle für die Produktqualität- und Sicherheit spielt. Ruland ist seit seiner Gründung Partner der Biotest AG und hat unter anderem Produktionsanlagen im Reinraum mit dem zugehörigen CIP-Equipment realisiert.
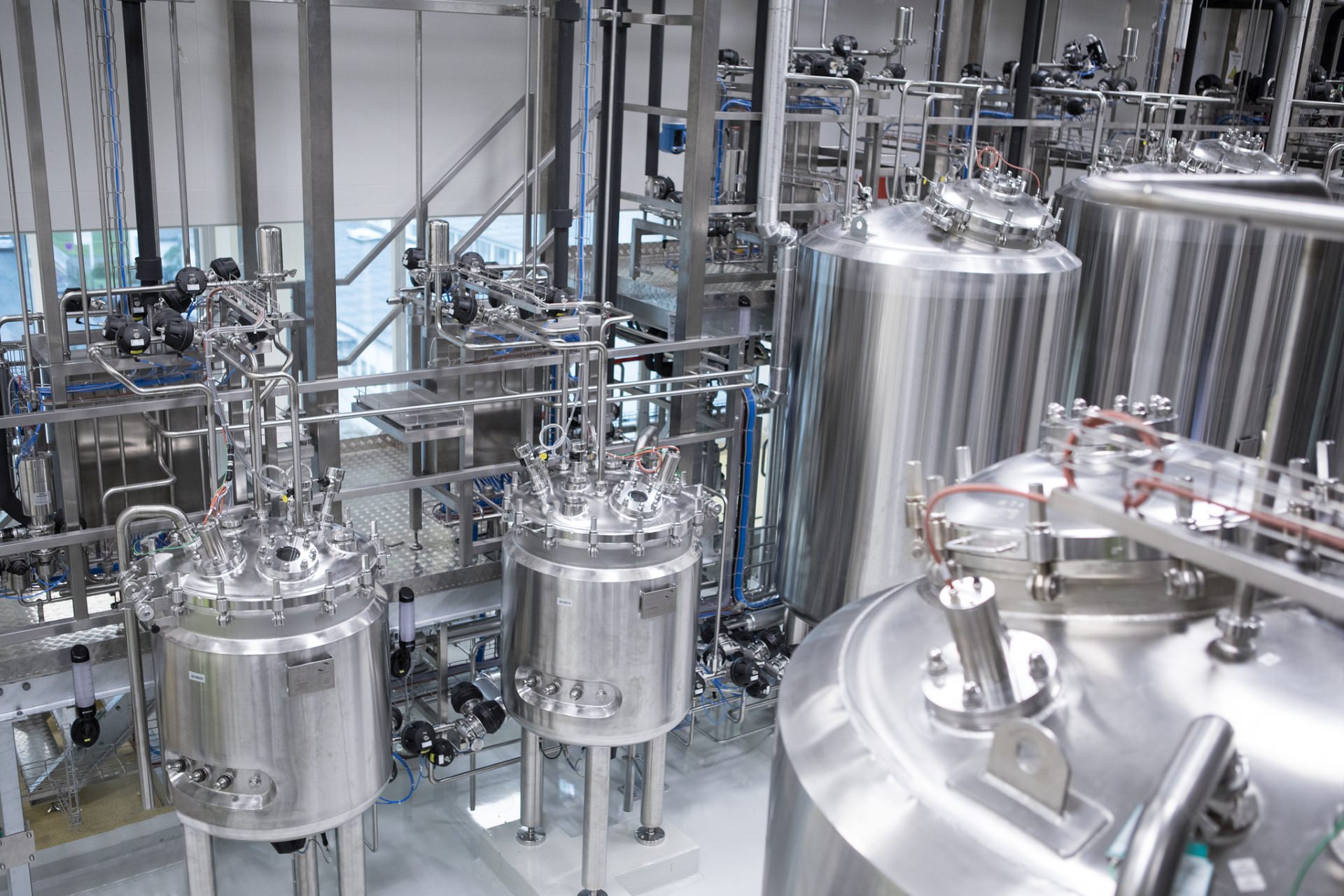
Produzieren Sie hochsensible Produkte?
Sprechen Sie mit uns über Ihre Anforderungen an die Anlagen-Technologie und den Prozess. Wir übernehmen das Engineering und liefern die Prozesstechnologie.