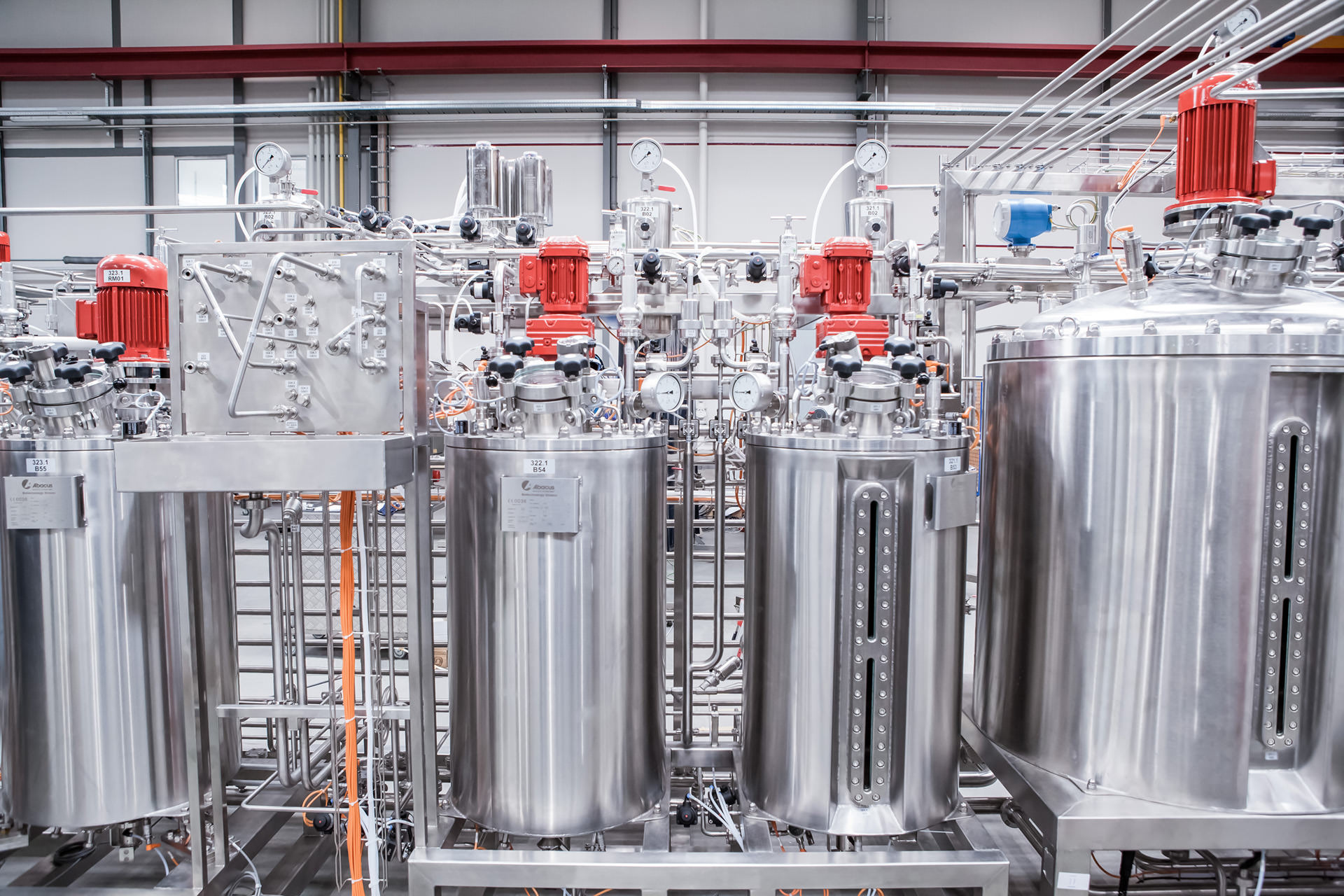
Achema 2024 - exhibition in Frankfurt
Efficient and sustainable production processes with fermenters and IBC tilting stations from Ruland
We are eagerly awaiting this year’s Achema in Frankfurt! In hall 4.0 at booth A3, from 10.06. to 14.06.2024, we will be exhibiting a container station for both aseptic filling and emptying of IBCs and bag-in-bags in Hall 4.0 at booth A3. Our team will also be on hand to answer visitors’ questions on all topics relating to the broad spectrum of plant engineering. For example, on the subject of fermenters, which we manufacture in a wide range of sizes from pilot plants on a laboratory scale to large industrial fermenters.
You can register for a free ticket to Achema at www.achema.de/de/tickets using the code A_zthNby6S.
Fermenters in many applications
the same in all process: precise control of fermentation conditions
Fermenters are used in various industries as the pharmaceutical and food industries, the cosmetics industry and the chemical industry. The fermentation process involves the supply of nutrients and the control of temperature, pH and other environmental conditions. Modern fermenters, such as those developed by Ruland, are equipped with advanced sensors, automation technology and control systems. This precise control creates optimal growth conditions for microorganisms and triggers biochemical reactions that lead to the desired product formation. The better the conditions, the more efficiently the microorganisms work.
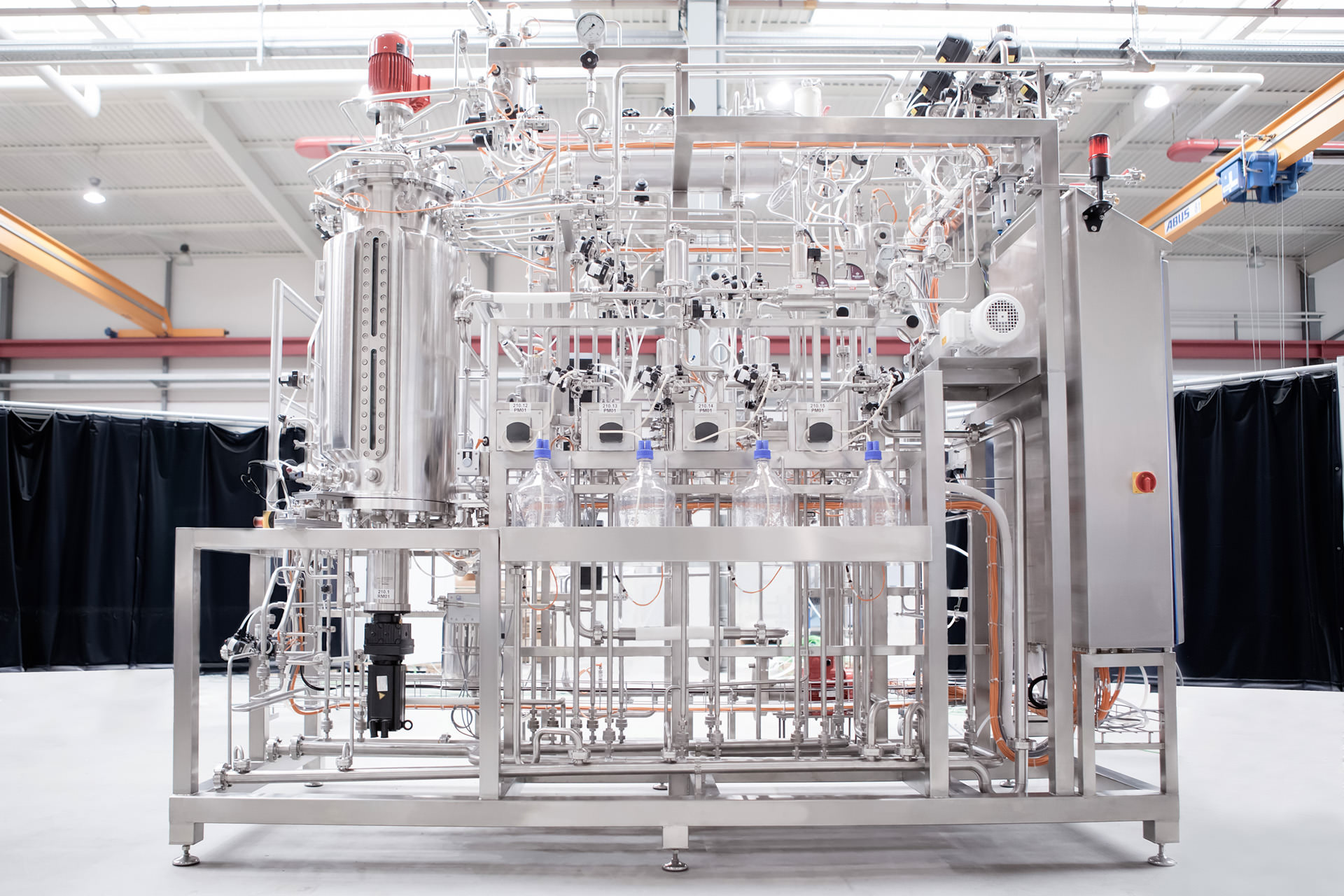
Fermenter in production
With up- and downstream processes for the complete production chain
Ruland supplies fermenters and bioreactors in many sizes for production: from pilot plants on a laboratory scale to large industrial fermenters. For projects in which production, processes or products are initially to be tested in small quantities, we accompany the scale-up process. We scale up containers, stirring behavior, gassing and other processes with consistent procedures and integrated control software. For the production of the end product on an industrial scale, we supplement our expertise in the optimal process technology for the actual fermenter or bioreactor with the appropriate plant modules in the upstream and downstream production process. This also includes the provision of media from various containers or tank farms, the mixing of raw materials and their preparation (such as thermal treatment, filtration, storage). The Ruland experts also consider the downstream process, such as aseptic emptying from the fermentation tank and subsequent further processing (storage, extraction, filtration, separation, aseptic transfer to filling). Particularly in large-scale industrial production processe fermentation cascades optimized for efficiency are used, from which the fermented product is transferred from one tank to the next larger one. The flexibility and scalability of the fermentation processes allow them to be adapted to different production requirements, from small laboratory batches to large-scale industrial production. This ensures that both small start-ups and large industrial companies can benefit from the advantages of modern fermentation technology. Ruland is committed to the continuous development of fermenter technologies to increase efficiency and to promote sustainable and environmentally friendly production processes. These innovations are crucial for the development of new products, such as vegan alternatives, and support the production of conventional products in a sustainable way.
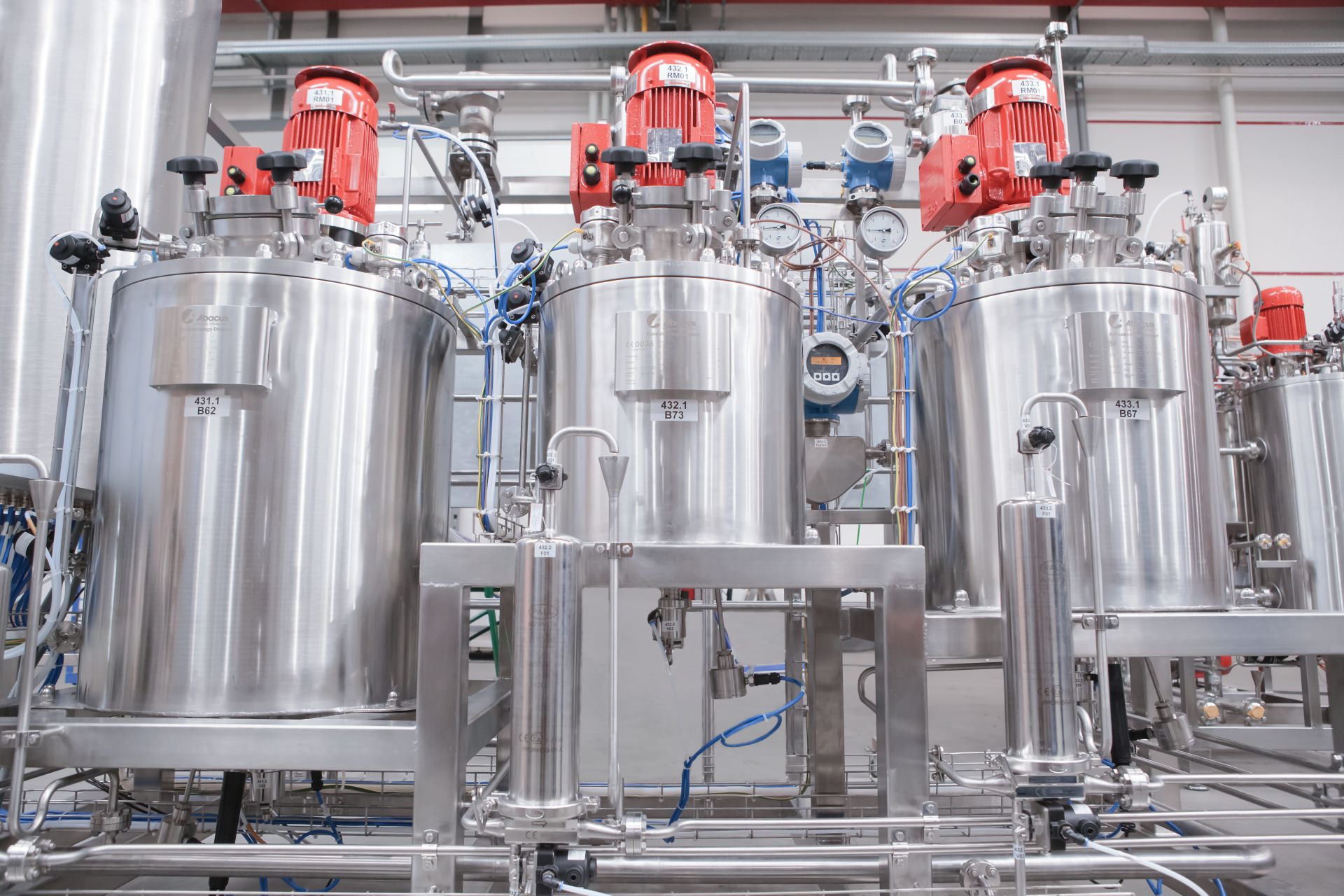
Ruland IBC tilting station
Efficient emptying and safety
The IBC tilting station from Ruland enables the safe tilting of an IBC by approx. 7°, ensuring optimum residual emptying – even with hazardous substances. Thanks to its robust design, the station is particularly wear-resistant and corrosion-resistant, which ensures a long service life. Our IBC tilting station offers maximum operating safety and impresses with its simple handling. Ease of maintenance is our top priority, so you can rely on smooth operation. The space-saving design and variable usability make the Ruland IBC tilting station the ideal solution for your requirements.
Click at the link below to activate the video. Please note that after activation your data will be submitted to the respective provider.
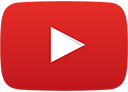
Customized solutions for your requirements
IBC tilting station - as individual as your needs
The IBC tilting station from Ruland offers customized solutions for your needs. The dimensions – length, width, depth and height – can be customized to fit perfectly into your operating environment. A hazardous goods tray can be placed under the tilting station or alternatively a VA tray to ensure maximum safety. The height of the tilting station is designed so that a storage space can easily be set up underneath. The overall height can also be individually adjusted to ensure optimum ergonomics and handling. For larger requirements, several tilting stations can be easily linked together, ensuring flexible and efficient use. Rely on the IBC tilting station from Ruland for a safe, adaptable and efficient solution in your business. You can find more information about IBC tilting stations in our brochure: Ruland tilting station
Expert knowledge at Achema
Professional expertise and advice
The experts from Ruland will be available for you at Achema for all topics relating to plant engineering and production processes for liquid products. Especially for in-depth questions about our fermenters and IBC tilting stations, you can count on the broad specialist knowledge in engineering and plant construction, supplemented by the expertise of the tank and apparatus manufacturer M. Roth.
Secure your ticket and make an appointment
You can use the voucher code A_zthNby6S to register for a free ticket to Achema at www.achema.de/de/tickets. Your contact for questions and appointments:
Nadine Plantefol | Marketing | +49 6327 382403 | nadine.plantefol@rulandec.com