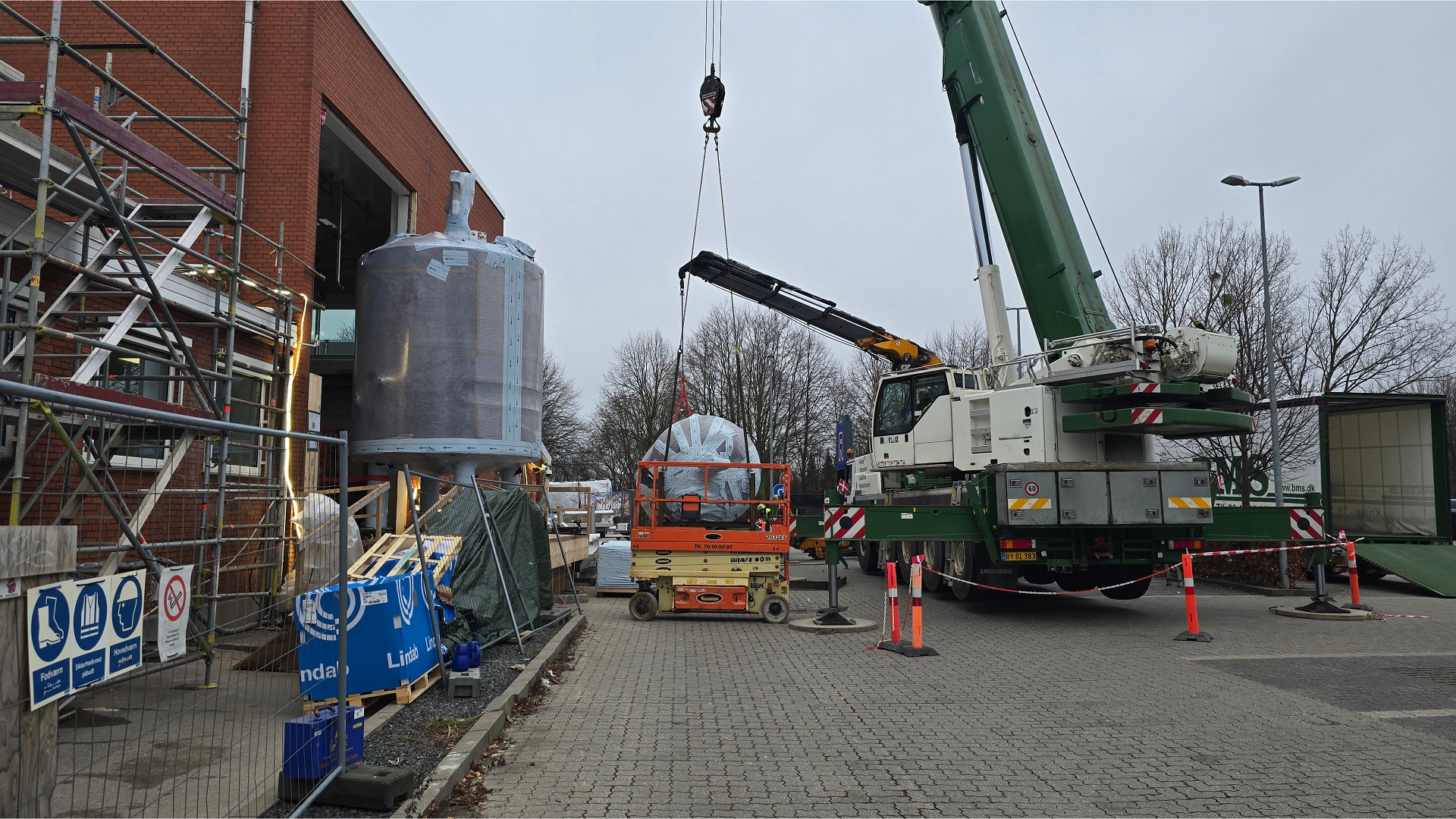
Hygienic design system gets additional vessels
Planning and implementation to the highest hygiene standards
At the end of 2023, we won an exciting order from a long-standing customer. The customer in the pharmaceutical sector wants to increase its production capacities for fermentation significantly. To this end, the customer ordered new production tanks with an operating platform and system technology in hygienic design.
A particular challenge in the project was to install the containers in the building during ongoing production. The integration into the existing, qualified production process and infrastructure was to take place during the production phase.
Preparation of the assembly work
during summer shutdown
Our fitters and engineers used the 2024 summer shutdown for preparations. They fitted existing pipes with the required additional outlets and pulled the pipes up to the boundary of the new reactor room. A section of the operating platform was then set up in the almost empty room and the pipe routes prepared. For later installation, recesses had already been made on the platform with precise match to the containers. This way, our team on site was able to prepare the connections and subsequent assembly. This allowed also to qualify the customsed system modules in cooperation with the customer.
Quick insertion
and hygienic design
The containers were recently installed. To do this, a side wall of the production building was opened and the tanks were moved quickly and precisely to their intended positions with the help of a roller system. The second half of the operating platform was then installed around the tanks. The building technology, process modules and cabling still have to be added.
The high hygiene requirements of this system are met by a consistent diamond-shape design. This avoids horizontal contact surfaces. This allows liquids to drain away quickly, and prevents the build-up of residues. The frames are all installed at a 45-degree angle, components are screwed in and a special selection of components is used to create a hygiene zone that is easy to keep clean.
Smooth integration
thanks to extensive 3D planning
Thanks to the extensive 3D preliminary planning, the smooth installation of the containers and a high level of prefabrication, the new plant, including integration of the control systems, shall be commissioned by Summer 2025 the latest, and production in the new fermenters will start.