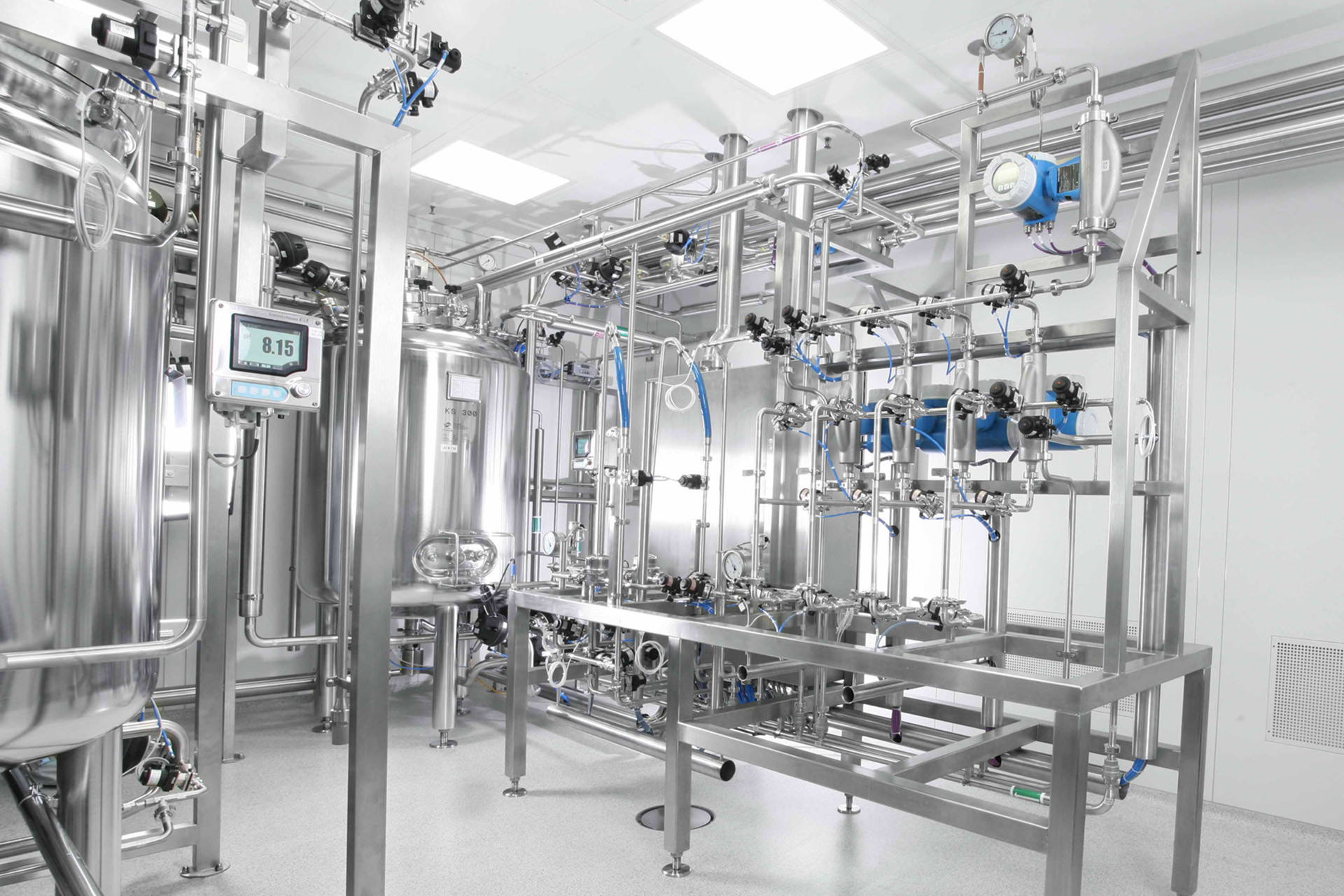
Filtration systems
High product quality thanks to filtration with automated filtration plants
During filtration process, the filtration systems concentrate liquids or separate substances to achieve a certain product quality. There are various separation processes for the filtration of liquid products. For many years, Ruland has been designing and building filtration plants for beverage, food and pharmaceutical products. With filtration plants, our customers achieve an improved product yield and continuous product quality. When engineering the plants, we consider respective hygienic requirements and local conditions. We realise filtration plants that separate the substances via membranes. The membranes act like mechanical fine screens. In membrane filtration, the size of the pores determines which particles are retained. Depending on the product, we select the adequate process and filter medium together with our customers. Ruland builds mainly dead-end-filtration plants with filter cartridges and cross-flow filtration plants with polymer membranes or ceramic membranes.
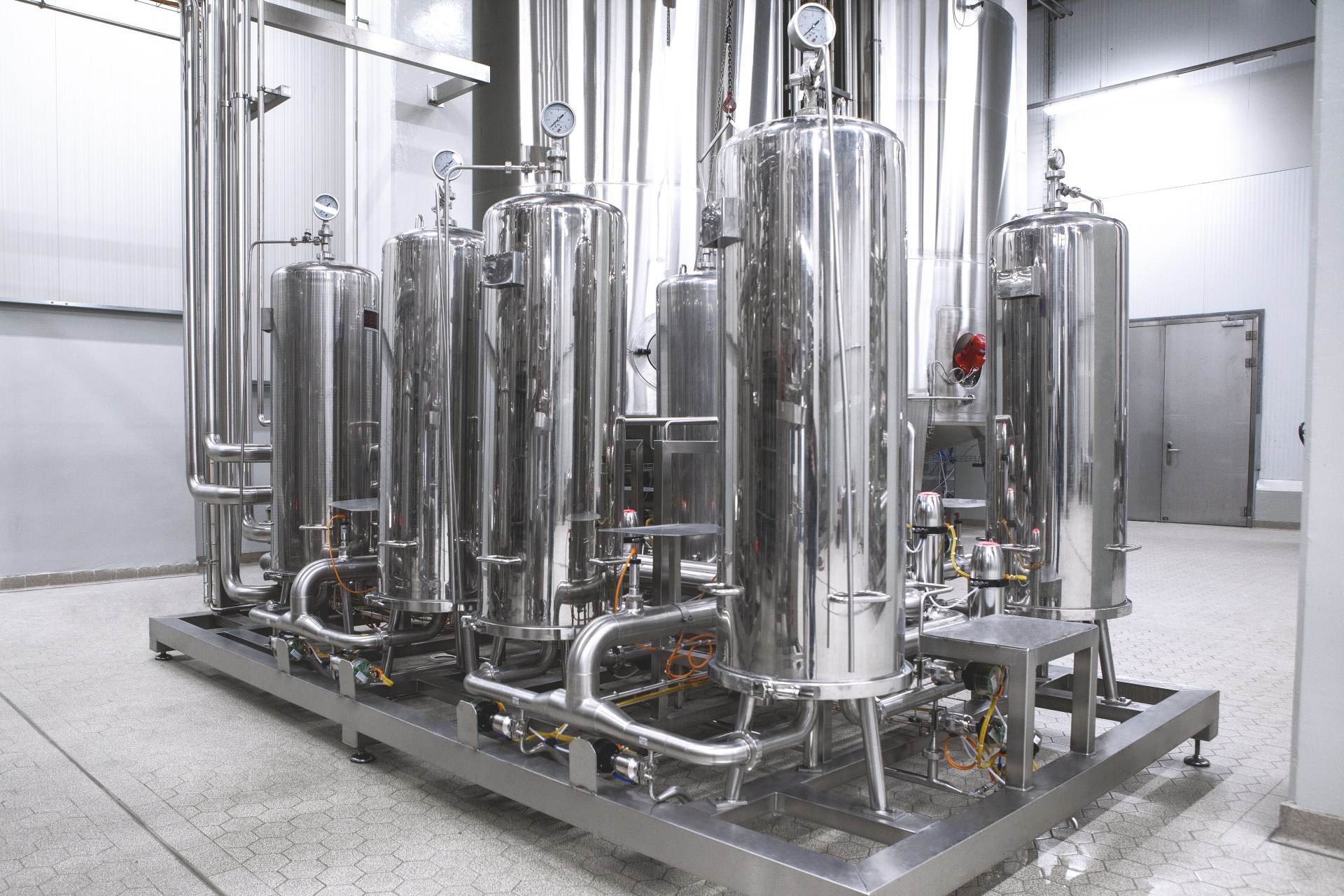
Dead-end-filtration
Simple structure for the classic dead-end filtration process
Dead-end is also often called “the classic filtration process”. The best known dead-end filtration process is a coffee filter. Due to the relatively simple process of dead-end filtration, the construction of these plants is less complex compared to other filtration processes. It also offers higher energy efficiency. As the retentate is not continuously flushed, residues (filter cake) are formed quickly with this method and must be disposed.
Dead-end-filtration is used for particle separation and sterile filtration of water, fruit spritzers, beer or wine.
Cross-flow filtration
Continuous process with cross flow filtration
Cross flow filtration is also called tangential flow filtration. In this filtrations process, most of the liquid flows along the filter membrane and does not directly flow through a filter as at the dead-end filtration. During cross-flow filtration, two liquid streams are formed: the permeate and the retentate. This enables a continuous process. The fluid flows parallel to the membrane (the filter) and prevents a filter cake from settling and closing the filter surface. The continuous flow in the filter circuit requires a lot of energy, but also makes the design more hygienic than other filtration methods.
The food industry uses the crossflow filtration very often. For example during short time heating and the concentration of fruit juices as well as for the filtration of wine, sparkling wine and vinegar. However, pharmaceutical companies also use crossflow filtration for product concentration and fractionation or separation of small particles such as viruses and bacteria as well as for the treatment of pure and ultrapure water.
Membrane filtration
Membrane filtration processes include microfiltration, ultrafiltration, nanofiltration and reverse osmosis
Membrane filtration includes all processes in which substances are filtered through membranes. The size of the pores determines which particles are retained and which pass through the membrane. The difference in the various filtration processes is in their pore diameter:
Micro filtration 0.5 – 0.1 µm
Ultra filtration 0.1 – 0.01 µm
Nano filtration 0.01 – 0.001 µm
Reverse osmosis 1.0 – 0.1 µm
The membranes are made of synthetics or ceramics. Depending on the design of the modules for filtration, a differentiation is made between hollow fibre membrane modules, spiral modules, tubular modules, plate modules and cushion modules. Ruland mainly uses hollow fibre and spiral modules for its filtration systems.
If microorganisms are to be filtered from liquids, this is called sterile filtration. Bacteria-proof membranes are used for sterile filtration. Sterile filtration is used for heat-sensitive liquid products such as vitamin solutions, vaccines, protein solutions, but also for wine, beer, fruit juice drinks, plasma fractionation and fermentation processes.
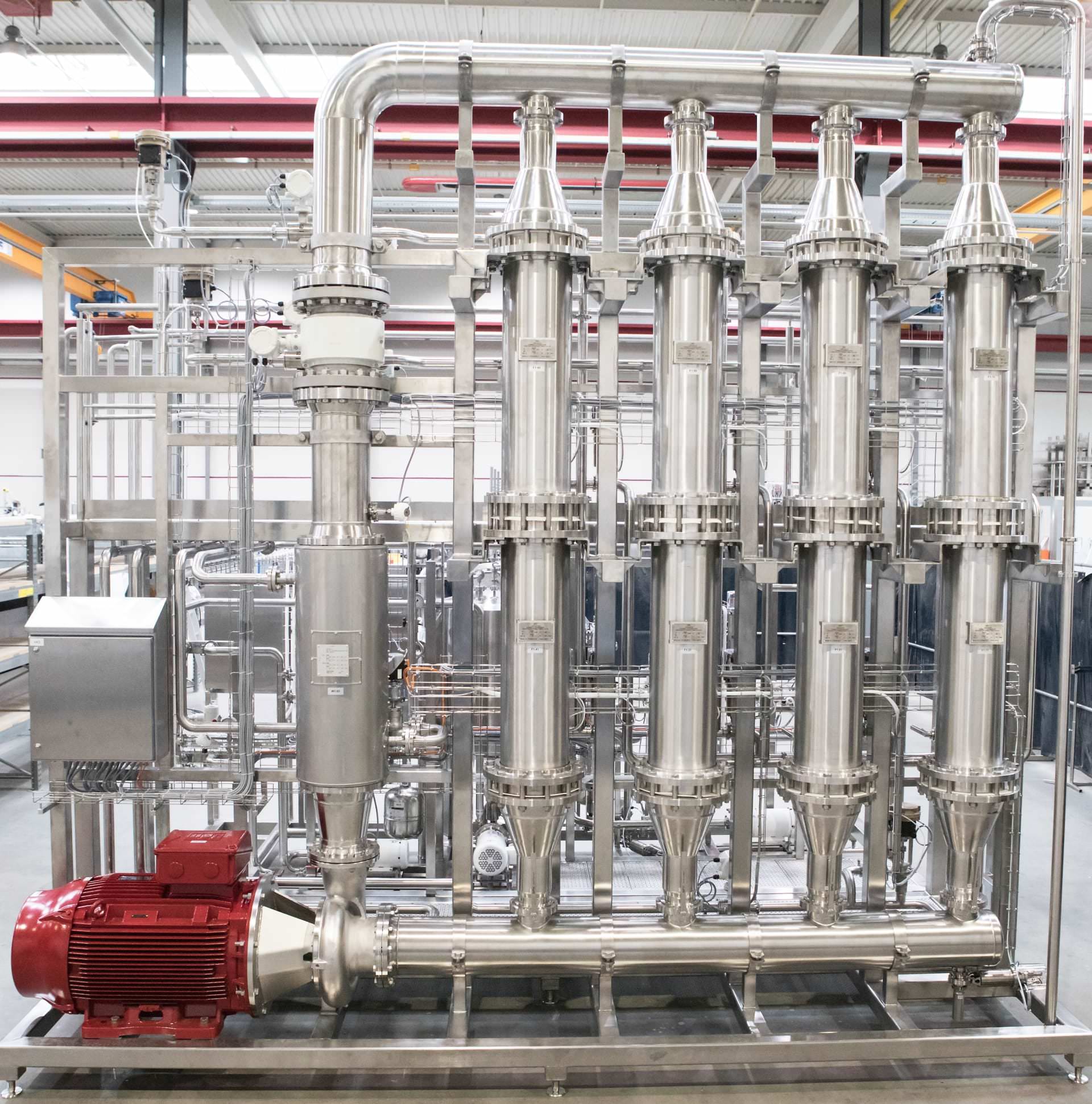
Microfiltration
For microfiltration we use spiral wound modules or hollow fibre modules, but also ceramic membranes
Typical examples of the use of microfiltration plants are:
Purification | preparation for sterile filtration of beverages or fermentation products | separation of bacteria in juice, milk etc. | fractionation of milk into fat and skimmed milk | pre-filtration of waste water | recovery and purification of cleaning media
Ultrafiltration
For ultrafiltration, we usually use hollow fibre modules for the filtration process
Our customers use ultrafiltration in their plants for various processes such as
Concentration and fractionation of proteins such as blood plasma proteins, whey protein | concentration of fruit juices | concentration of waste water and heavy metals
Diafiltration is a special application of ultrafiltration.
Nanofiltration
The nanofiltration separates or concentrates very small particles
The food and pharmaceutical industries use nanofiltration plants for
Separation of heavy metal ions or very small particles | removal of viruses from protein solutions (virus inactivation) | partial desalination/softening of raw water
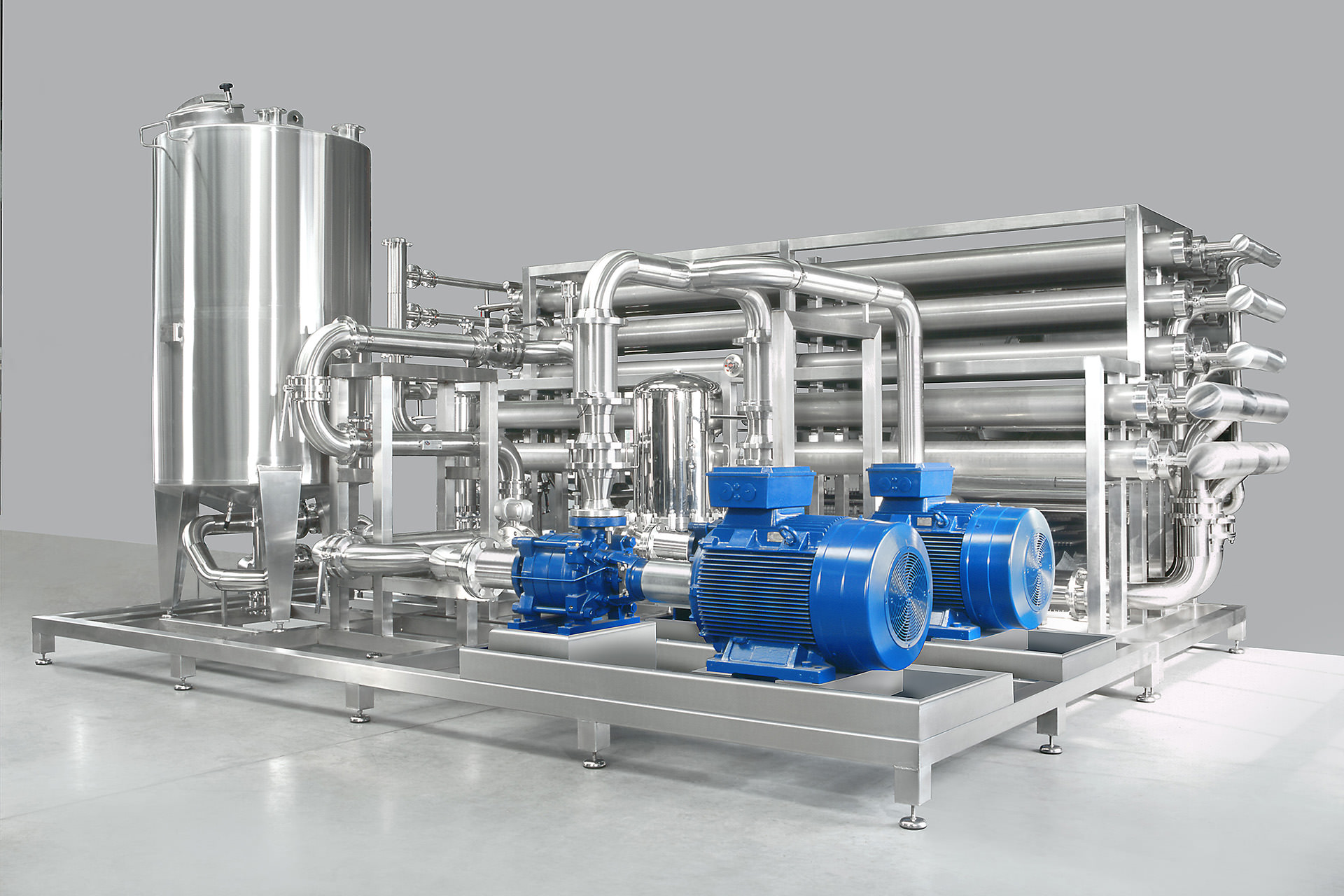
Reverse Osmosis
The reverse osmosis (RO) process works with very high pressure
In reverse osmosis filtration, the membrane pores are so small that all dissolved substances are retained and only water can pass through the membrane. A very high pressure is used to reverse the natural osmosis. Therefore, the membranes used for the reverse osmosis process are designed for very high pressures.
Production of ultrapure water | drinking water treatment | seawater desalination | treatment of product water for food and beverages | in combination with evaporation processes also for dealcoholisation of beer, wine etc.
The possibilities of filtration are manifold.
We would be pleased to discuss the individual filtration processes with you. Explain us your application!