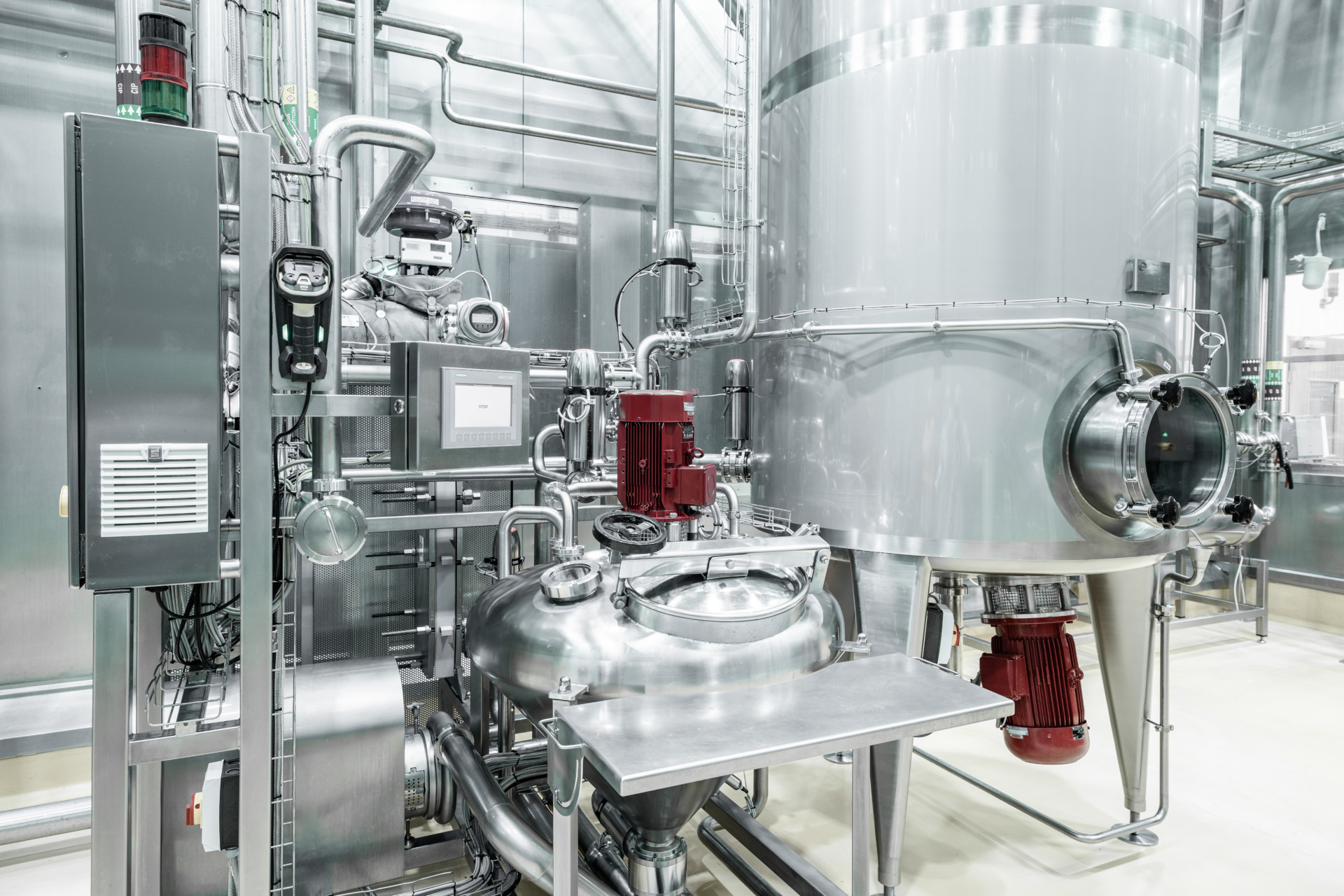
Powder dissolving and dosing systems for the beverage industry
Efficient solutions for demanding raw materials
Our powder dissolving and dosing systems ensure stable processes, reproducible product quality, and maximum efficiency – even with poorly soluble powders such as pectin, xanthan gum, or thickening agents.
Clean dissolving. Precise dosing. Reliable processes.
A module with clear advantages
Beverage production is a complex process that requires precision, hygiene, and a high degree of automation. Manufacturers must respond to consumer trends, ecological and technological challenges, while remaining competitive with high product quality.
The dissolution and dosing phase is an important factor that determines the quality, taste, and stability of the end product. We provide you with a well-designed solution that meets all requirements – from hygiene to repeatability. With clear advantages for production:
- High solution speed – even with critical substances
- Dust-free handling and hygienic design
- Precise, automatic dosing
- Modular design – flexibly adaptable to your product range
- Can be integrated into existing lines
Hygienic design systems
Reliable powder mixing with EHEDG-compliant system design
Our technology ensures fast, complete dissolution and consistently stable parameters in the final solution. This is particularly important in the production of energy and functional drinks, whose recipes are complex and place high demands on solubility and dosing accuracy. Ruland consistently focuses on hygienic design. As an active member of the EHEDG, we meet the highest hygiene standards – from engineering and manufacturing to installation in your production environment. Every component is designed to ensure cleanability and product safety.
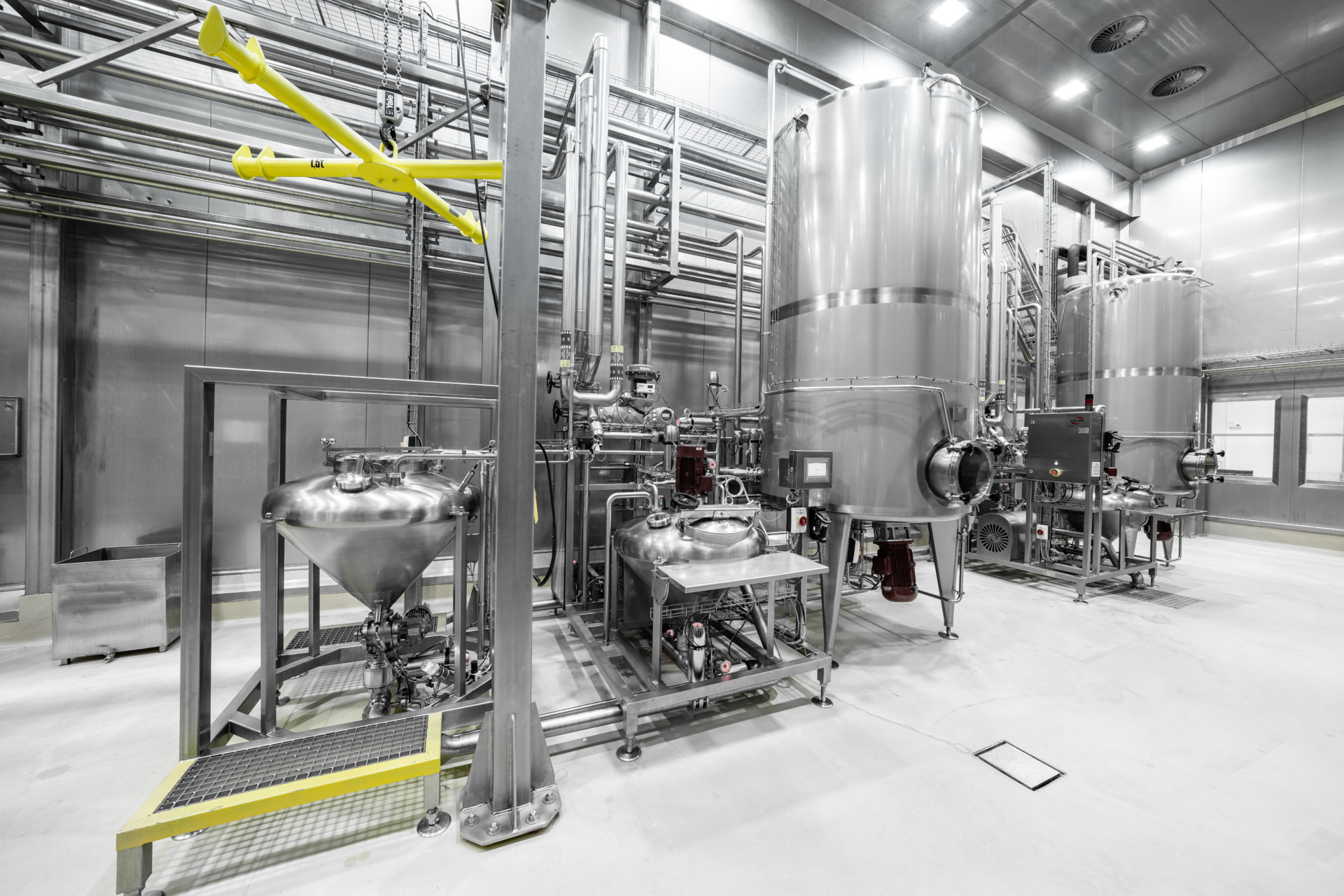
Modular systems for dissolving powder and for dosing
For efficient beverage production
Our powder dissolving and dosing system consists of precisely coordinated modules: Two hoppers for precise powder feeding | Reaction tank for controlled dissolution | Heating system for process support with thermally sensitive substances | Bridge crane for efficient handling and ease of use. Each component meets the highest standards of hygiene, functionality, and flexibility—ideal for modern beverage production. The first hopper is specially designed for bulk material from big bags. An integrated stainless steel crane enables safe and hygienic handling in sensitive production areas. The system is easy to clean and offers lasting corrosion resistance. A specially developed feed hopper minimizes dust emissions when emptying the big bags. The system thus increases process reliability and improves working conditions at the same time. Hopper number 2 is a real all-rounder. It doses powders and liquids from various types of packaging, such as bags, bottles, or canisters. Thanks to its high flexibility, the hopper can process both cold and hot media. An integrated heat exchanger precisely regulates the temperature of the process water and ensures that the finished solution exactly meets the specifications of the recipe.
Three-stage mixing
Mixing technology for reproducible processes in plant engineering
At the heart of the system is a three-stage mixing process. It ensures fast, uniform, and complete dissolution—regardless of the physical or chemical properties of the materials used. In the first stage, a high-speed agitator disperses the components directly upon entry. A circulation circuit then stabilizes the mixture and ensures continuous homogeneity. In the third stage, a turbo nozzle in combination with a floor-mounted agitator thoroughly mixes the entire volume in the reaction vessel. Our dissolution system works reliably and delivers reproducible results – even with demanding formulations.
Flexible dosing technology
Adaptable system solution for varying batch sizes
The system processes both full tank volumes and small batch sizes – ideal for systems with frequently changing recipes and smaller production quantities. A floor-mounted agitator ensures homogeneous mixing until the tank is completely emptied. This keeps the solution stable even in the final phase of the mixing process. The reaction tank is equipped with a sight glass and a glass hatch, which allow real-time visual inspection without interrupting the process. In addition, a foldable work table on the hopper ensures easy handling of a wide variety of packaging types. This significantly increases ergonomics and improves occupational safety.
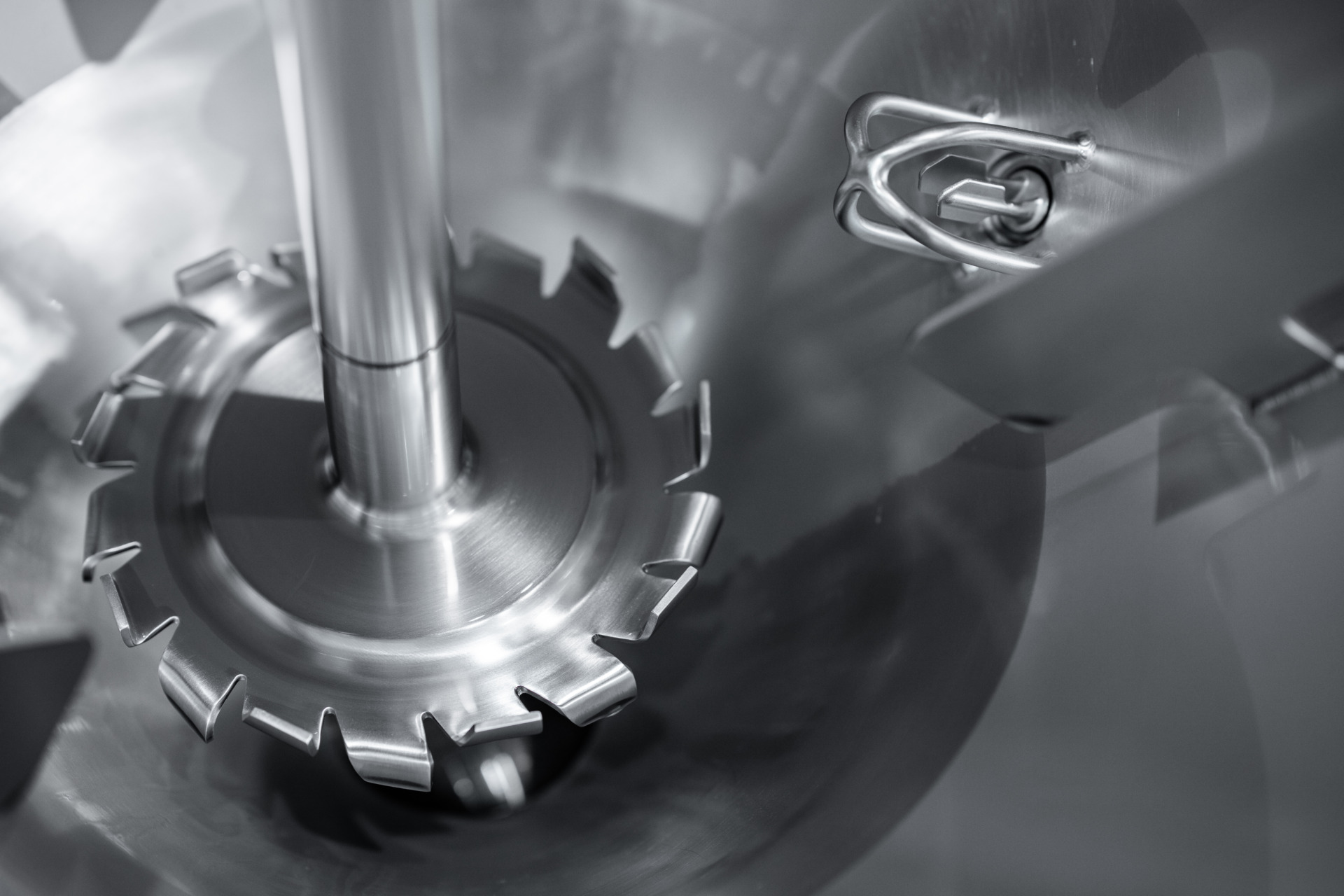
Safe process systems for operators and technology
Ruland protects with sensor technology and intelligent control
Ruland’s process systems meet the highest safety standards. They protect both the technology and the operating personnel through a combination of mechanical, electrical, and software-based protective measures. A physical safety grid in the hopper area prevents the ingress of packaging residues or foreign objects. It is coupled with position sensors. If the grid is removed, the system automatically stops the agitator. This ensures safety and plant protection at all times.
Automated recipe control for dissolving and dosing
for reproducible product quality
A central element of the system is the recipe software specially developed by Ruland. It controls and monitors all relevant parameters in real time, such as medium temperature, agitator speed, and mixing phase duration. The software provides the operator with clear instructions throughout the entire process regarding dosing sequences, timing, and quantities. This reduces operating errors and ensures that each batch meets the specifications exactly. By intelligently combining automation and safety, we create a controlled process environment. It ensures consistent product quality – regardless of the operator or batch. The system thus meets all the requirements of modern beverage production: safe, reproducible, and efficient.
Intuitive recipe software
User-friendly software with automatic quantity calculation
Our user-friendly recipe software is an integral part of the plant control system. The user interface is intuitively designed so that staff can create new recipes or adapt existing ones independently after a short training period. The software is included in the scope of delivery, requires no licenses or subscriptions, and is based on an open architecture. In addition, the software automatically calculates the exact quantities of each component based on the desired production volume. This ensures that the entire manufacturing process is planned efficiently and executed reliably.
Think economically – produce efficiently
Use resources – avoid product losses
The dissolving and dosing system developed by Ruland combines intelligent technology with economical operation. A single, centrally located pump handles both the dissolving process and the delivery of the finished mixture. Together with the maintenance-free injector system and optimized parameter control, the system reduces media consumption and significantly lowers maintenance costs. An integrated packaging rinsing system reliably recovers product residues from containers. This increases yield, improves dosing accuracy, and increases the repeatability of each batch. Even the rinsing water used is not wasted: the system automatically records its volume and takes it directly into account in the recipe – for maximum resource conservation.
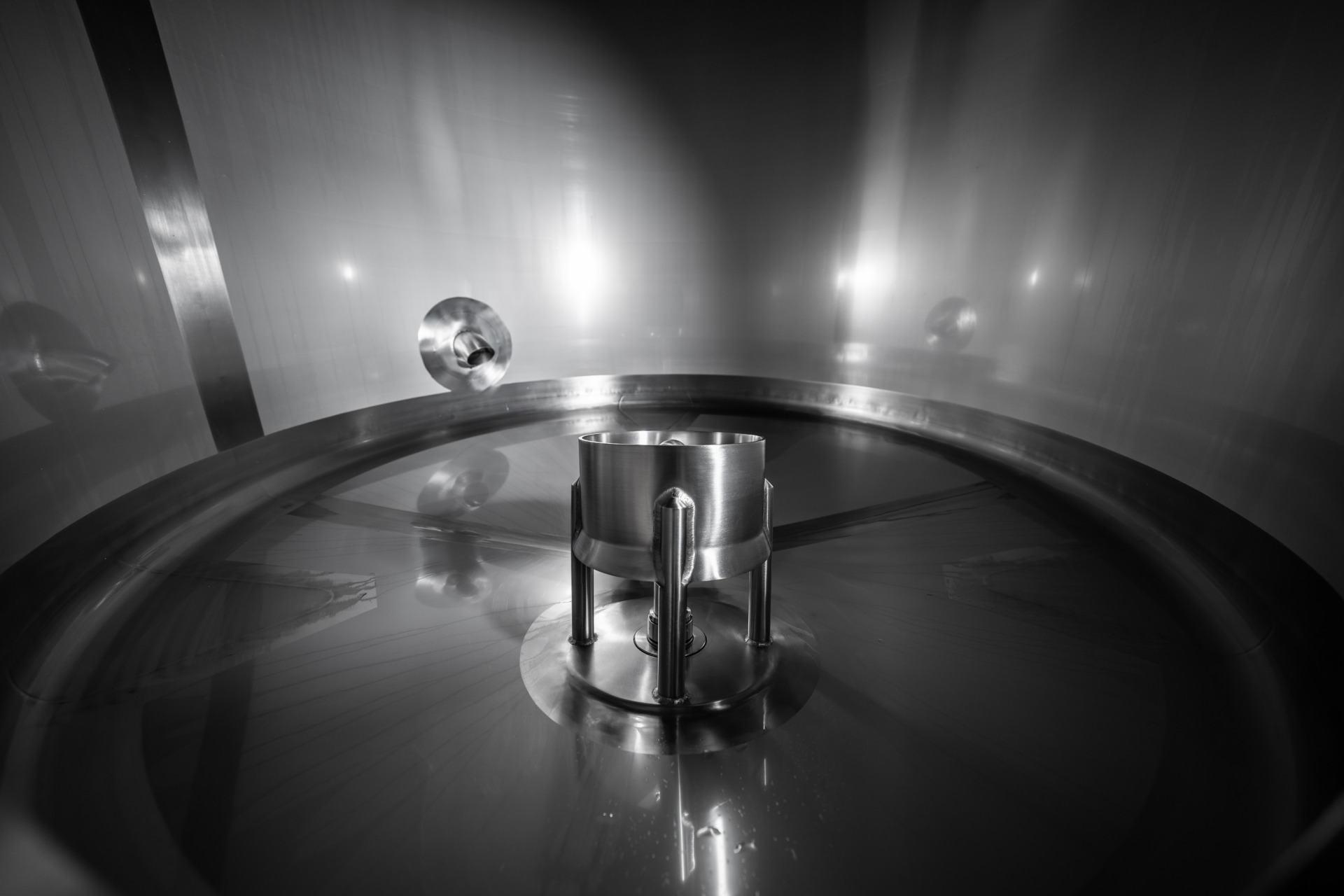
Modular, scalable, future-proof
Automated systems for a wide range of recipes
Ruland’s dissolving and dosing systems are designed as universal systems for a wide variety of recipes. They can be flexibly adapted to individual production requirements and are already being used successfully by many well-known beverage manufacturers. Their sophisticated design, high degree of automation, and consistent focus on process reliability make them a key component of modern production lines—scalable, low-maintenance, and ready for new requirements.
Plant engineering with experience
Discuss your projects with us at Drinktec 2025 in Munich
Visit us from September 15 to 19 at Drinktec 2025 in Munich and experience the latest version of our powder dissolving and dosing system live. Our systems are suitable for all applications in the beverage industry, including soft drinks, fruit juices and concentrates, milk-based beverages, plant-based products, sports and energy drinks, as well as syrups and premixes. Take the opportunity to talk directly to our experts about innovative process solutions from the Ruland portfolio – practical, technically sound and tailored to your individual requirements.