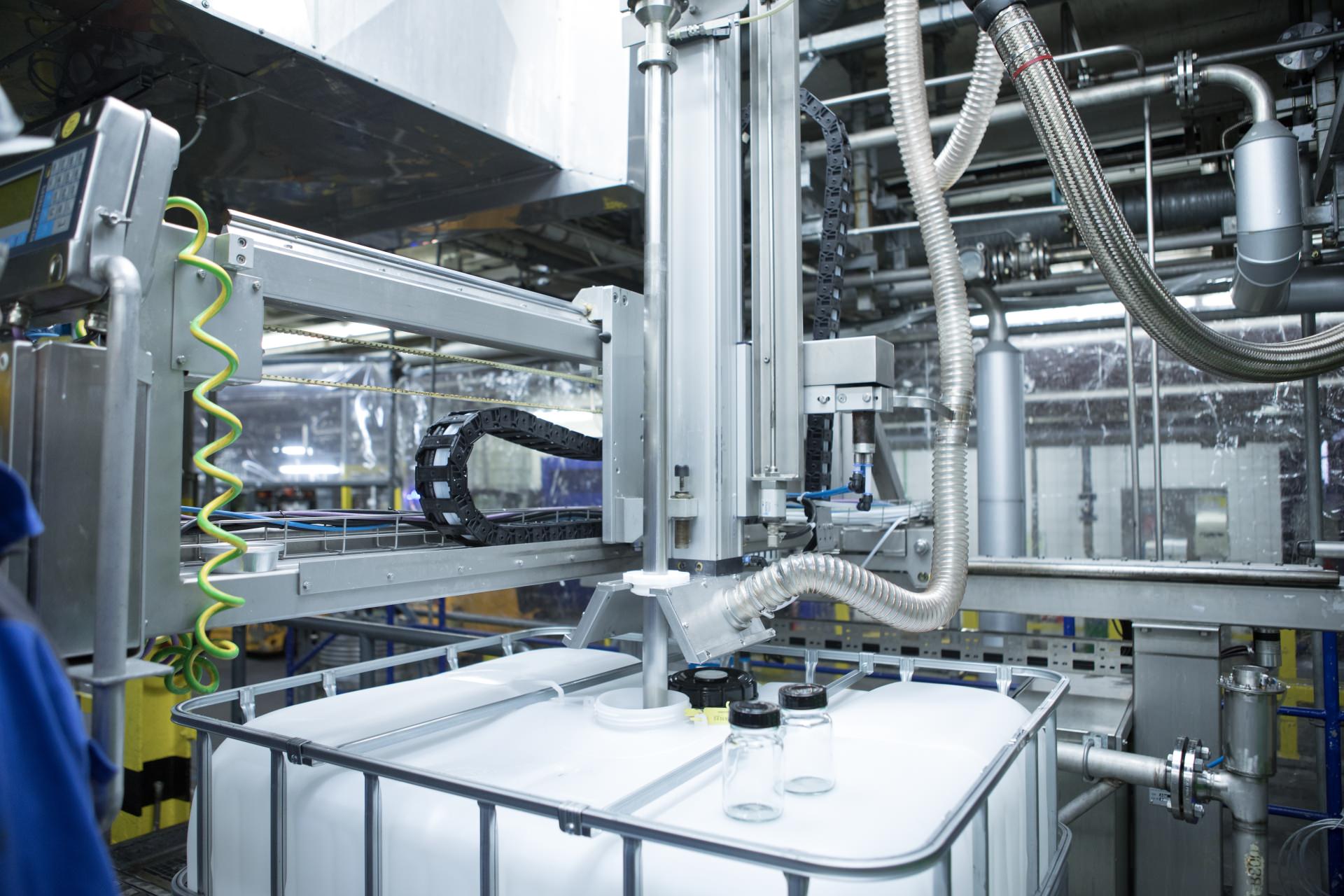
Project report
Improved yield and faster changes of products
BASF Personal Care & Nutrition GmbH
Cleaning of pipes with the Whirlwind technology
Since the BASF has used the Whirlwind technology to clean the pipes, they have not only improved the yield but also minimised the time it takes to change products.
Efficient economy while producing – that is the producing industry’s maxim. One of the producer’s biggest wishes is a faster change of products with the highest purity and maximum yield rates. Already while planning the production processes, it should be made sure to get a minimum of mixed phases. One possibility is to clear out the product with an auxiliary medium. Via sensors, the mixed phase is recognised due to chemical and physical characteristics and the cleaning of the pipes is activated automatically. Only the pigging- or Whirlwind technology are able to fully avoid or to at least reduce the mixed phases as far as possible. Choosing the most suitable method according to the individual needs helps the plant engineer to avoid possible obstacles
In this way it is possible to produce difficult products simply, efficiently and sustainably with quick changes. Ruland Engineering & Consulting GmbH is specialised on the innovative Whirlwind technology that can also be easily integrated into already existing production systems and achieves highest results even at complicated piping routes. Ruland modernised the existing process for changes of products including cleaning for a plant of the BASF group. For more than a year now, the customer has used the Whirlwind technology and it has fully met all expectations, because next to an improved yield it has also achieved an excellent cleaning performance.
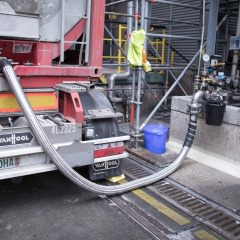
An individual concept for already existing piping systems
The grown piping system at BASF needs a flexible method for pipe clearing and cleaning.
The BASF Personal Care & Nutrition GmbH develops, produces and markets a broad range of ingredients for the cosmetics industry as well as for household- and industry detergents based on renewable resources. Over the years, the system has grown and the filling process runs over a ramified network of pipes. The piping station runs from tank trucks or farms to several filing scales and a station to load tank trucks. The condition of the piping system limits the possibilities for cleaning: a great number of branches, hose coupling points, valve clusters and the instrumentation are the reason why the pigging system is not effective for this system. However, for an air vortex, these piping elements are no obstacle. Due to its high flexibility, the Whirlwind technology offers the chance to simplify processes and to optimise the yield, even under these circumstances.
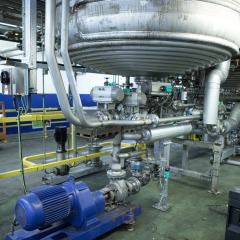
Finding a solution after analysing
Ruland starts with test series and a detailed plant analysis to identify the potential for faster changes of products and a higher yield at the piping system.
First, Ruland tested the cleanability of the various products from BASF Personal Care & Nutrition at the Ruland-test system in Neustadt. They also made a detailed analysis of the system in Düsseldorf to exactly evaluate the starting position and found a situation that is common at chemical plants: the piping was unsuitable to achieve a satisfying, economical product change with an ensuing standard cleaning. Installations like T-pieces with death ends, big jumps in nominal width, complicated routing and instrumentation that was not hygienically optimised are general not really easy to clean. The cleaning takes a long time and is cost-intensive not at least because of the high scrap quantity. The pigging technology would only have been possible with a reconstruction of the whole piping system.
The planners of Ruland have been able to keep the effort at the system for the BASF in Düsseldorf very low. Thanks to the flexibility of the Whirlwind system it was enough, to selectively optimise the pipe network.
Prior to the Whirlwind technology, the cleaning of the system took place with steam and water. The result of this method was a high quantity of rinse- and cleaning water, loaded with product leftovers. The disposal of this water was very cost-intensive. The BASF did not only wish for a modernised technology that avoids or at least minimises waste water because of economic reasons but also because of their Group’s own sustainability strategy. It was also possible to reduce the time, the cleaning takes – a factor that multiplies itself, if changes of product often take place.
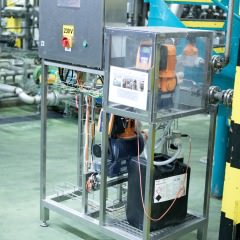
Sustainable cleaning of pipes
The Whirlwind system turns out to be the ideal technical solution for the challenging local requirements.
After precisely analysing the existing system and identifying and recording all weaknesses, the planners of Ruland developed a first concept for optimisation. Particularly under these difficult circumstances, the Whirlwind system was able to show its huge potential. It is easy to integrate the modules into the existing piping system. The modules are not complexly constructed and thus comparatively low in maintenance.
As Ruland has used this method already for several years, they have built up a certain expertise. Bernhard Scheller, Managing Partner, supervised this technology as pioneer right from the beginning and is convinced: “The Whirlwind system revolutionised changes of products and the intermediate cleaning of pipes“. It is also possible to convince interested companies with facts:
“We have a test facility at our head quarter in Neustadt”, says Scheller. “At this facility we are able to carry out cleaning tests with the individual products of our customers and check in advance how promising the system works.” Over the years, Ruland was able to gather a lot of measurement data, of which it is possible to derive clear statements and comparable figures. This exactly shows for which products it pays off and it guarantees for safety at the customer side.
Prior to the modernisation, the BASF plant in Düsseldorf had a high amount of waste material, which was very expansive in disposal. Since the new technology has been in use, they have reduced the disposal costs that much that the investment was recouped in a short time.
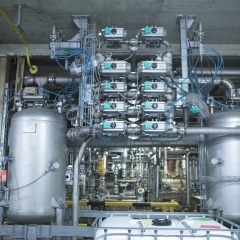
Reference values speak for themselves
Ruland was able to make the promise regarding cleaning power and efficiency based on the detailed situation analysis as well as the extensive experience and comparative values.
At the already mentioned preliminary tests, Ruland also measured the TOC-value at a defined piping route about 25m after a complete product change and a cleaning cycle with reference products and used it as basis for the acceptance at a comparable piping route on site. It was possible to clearly fall below the limit requested by the BASF at a route that was much longer: 75m.
Since 2016 the Whirlwind system has been successfully used in Düsseldorf. The responsible Production Manager at the BASF summarised: “We made the right decision by choosing this technology and we are satisfied with the results. We have been producing under better conditions since our system has been optimised. Product changes are now easier and quicker and we have less waste. The investment already paid off after 2 – 3 years.”
Do you have any questions regarding cleaning of pipes or systems?
Please talk to us about our cleaning systems.