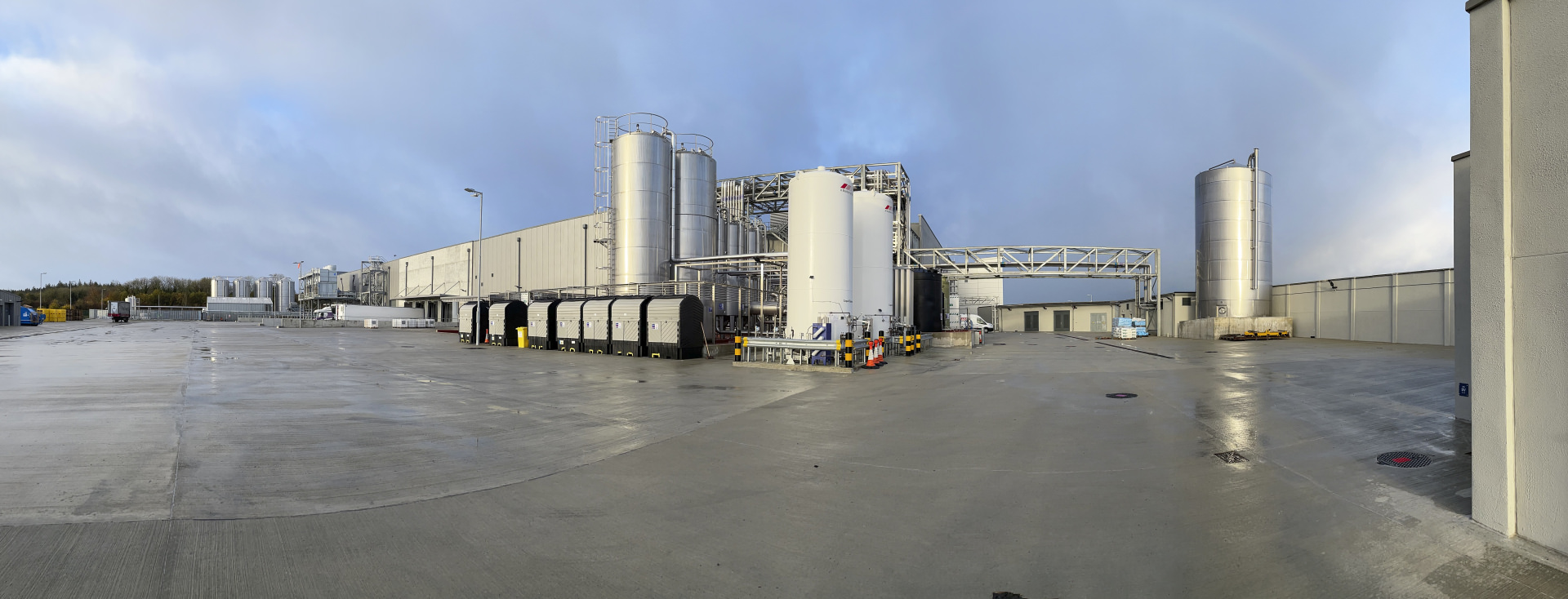
Project report
Glanbia Cheese
New plant for the production of mozzarella cheese
Liquid handling for the new mozzarella factory
Plant and pipeline construction for liquid handling of the versatile dairy product
The corporate group of Glanbia Cheese and Leprino Foods opened a new plant for producing mozzarella in Portlaoise, Ireland. The facility uses patented and bespoke processes designed to enable the production of recipes tailored to customers’ needs. To comply with exacting quality standard, the demands on all suppliers were very high and the implementation details extremely challenging. During the COVID-19 pandemic, numerous contractors from all over the world coordinated a busy large construction site with complex buildings. Being a specialist for liquid products, the plant manufacturer Ruland Engineering & Consulting GmbH took charge of the planning, design and realisation for the most parts of the utility supply for the production processes as well as the construction of the complete plant modules required in the liquid processing sector.
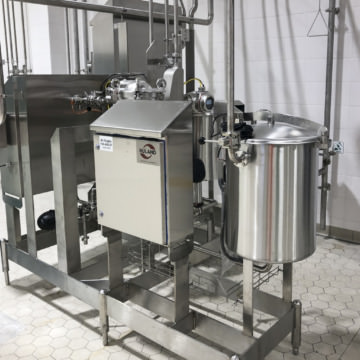
Hygienic design to meet the highest demands
Careful project planning starts with the basic engineering
During a visit to one of their flagship factorys in America, Leprino and Glanbia Cheese introduced to all potential suppliers their high demands regarding hygienic design. The customer employs a holistic approach with clear specifications and demands regarding building design, process, used components and the hygienic design of process modules and electrical installation in all areas. Following their USA visit the project team exactly knew the customer expectations for the new production site in Ireland. Even for the plant manufacturer Ruland, which sees itself as an expert in hygienic design and execution, the attention to detail in the implementation of this project was impressive and not commonplace for a food producer. Based on their many years of experience, Ruland’s engineers were able to further optimise some details. In 2017, the project started with an intensive basic engineering phase. Ruland was responsible for the areas of the process utilities. For all required media they gathered the expected consumption, building services included, in a 20,000-cell-chart. The project team evaluated all data, identified the needs and designed the units accordingly. In addition, a spontaneous change from the classical energy supply to a cogeneration unit to save on energy costs and resources was respected with all consequences. Before the detail planning started, Ruland checked together with the customer the commissioning of the single crafts, this way the team was able to focus on the detail engineering of the core task.
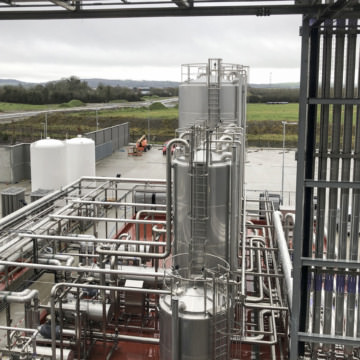
Technical equipment for the production facility
Design and delivery of systems and piping routes
There were two main areas in the subsequent Ruland scope of delivery: The design and delivery of plants as well as the complete piping design and installation on site for the entire factory. Ruland covered a large part of the technical equipment of the overall project. The Ruland technicians prefabricated and cabled all plant parts in Neustadt and put them into operation on site, including:
Water house including a daily buffer tank and water treatment, put into operation on site | Preparation as well as supply of hot and cold water for the entire plant | Dosing module for all liquid components | Central CIP unit for the supply of all process plants with tanks (up to a volume of 100 m3) and five circuits with a connection DN 150. The CIP cleaning plant was designed and installed externally owing to its height and the suitable climatic conditions | Chemical tank storage including storage tanks for acid and lye | Dosage unit for further chemicals | Various temperature control circuits for the process plant | 28 high pressure cleaning stations in special hygienic design including supply station | Electrical control cabinets for all Ruland modules
A detailed pipe planning supports the completion later on
Thanks to 3D and BIM, planning becomes vivid
The first planning of the entire factory piping was based on the consumer array and the spatial planning of the plants. Thereafter the engineers planned the pipe network and designed a 3D-model in which all pipe and cable routes as well as wall and ceiling break-throughs are graphed. Together with the architect and the executing construction company, Ruland integrated the 3D-data into a digital model named BIM (Building Information Modelling). With this model, each craft was able to call up the current status. Thanks to this comprehensive 3D-planning, the architect, construction company, Ruland-construction management and all other equipment suppliers could clearly identify and discuss possible problems at the interfaces. Additionally, due to BIM, everybody had a clear idea what the factory would look like later on and had the opportunity to check and optimise workflows.
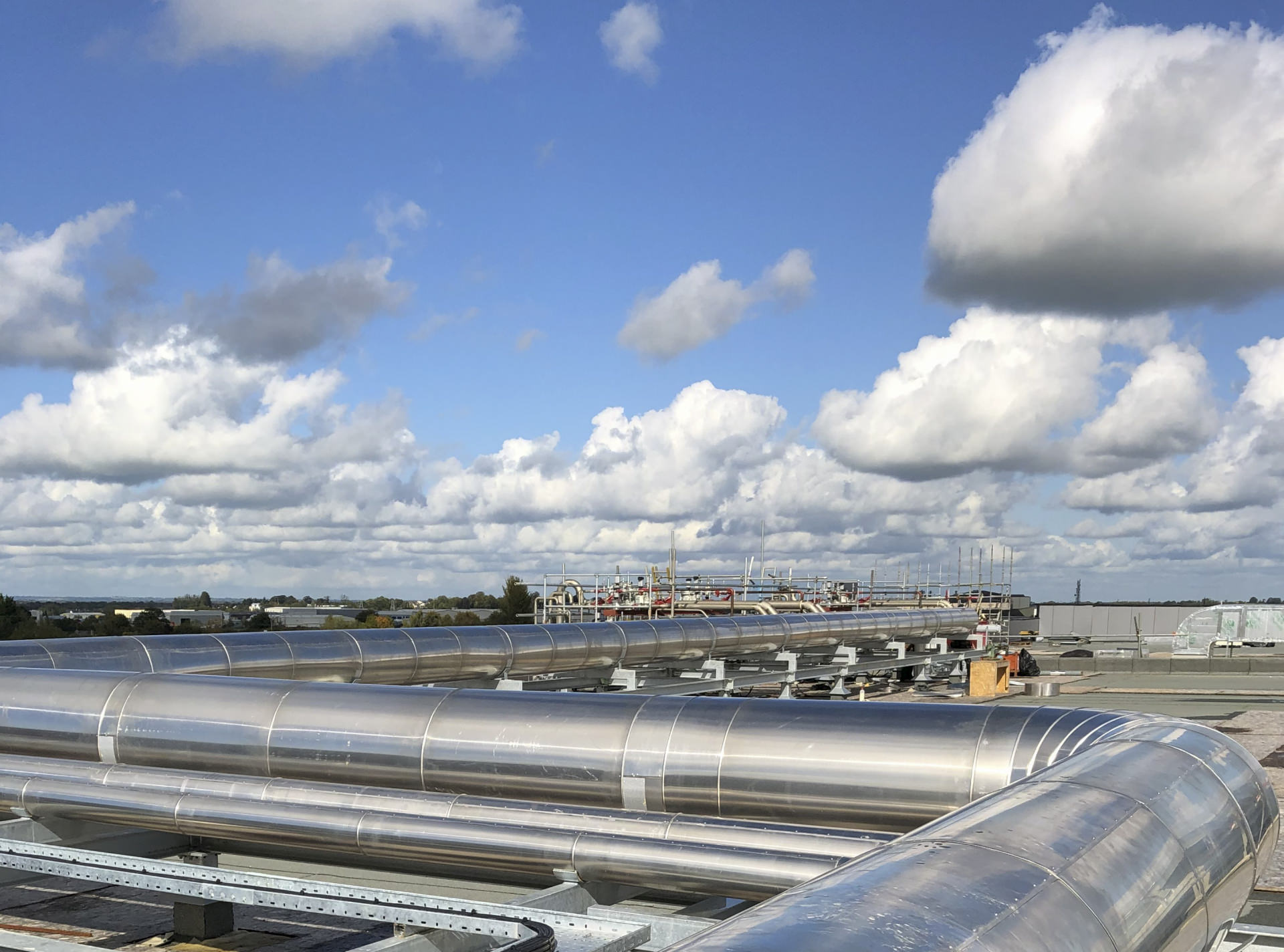
In August 2019, the team started with the realisation and organisation of the construction site. Axel Steinbach, the supervisor said: “Thanks to the BIM model and the technically very competent contact persons at the customer side, it was possible to find solutions for occurring problems without complications and on short notice. Minor errors that only became apparent on site were quickly corrected. Laying the pipe and cable routes in the low suspended ceiling was particularly tricky. We had to come up with a clever solution for this.” The Irish climate was also challenging for assembling the many kilometres of external pipeline . For impeccable welding it was necessary to protect the pipes against wind and weather during assembly. The team ensured the quality of the welding seams by an endoscope-test. Ruland needed a 500-t-crane to lift and place the heavy gantrys and pipe bridges. The Ruland-team was also responsible for the entire waste-water-piping and the connection to the waste-water-tanks on site.
The project represented in figures
Material, Manpower, project management
Material
- 30 km tube material, DN 15 – DN 30
- 6,000 bends
- 1,000 t-pieces
- 1,000 reductions
- 10,900 pipe clamps
- 39 km of cable
- 50,000 cable ties
Manpower
- 22,700 hours of engineering
- 71,500 hours of assembly work
Execution
- up to 60 employees on site
- 50 documents for evaluating occupational safety
- 450 safety trainings
Project
- approx.25 companies
- approx. 350 persons
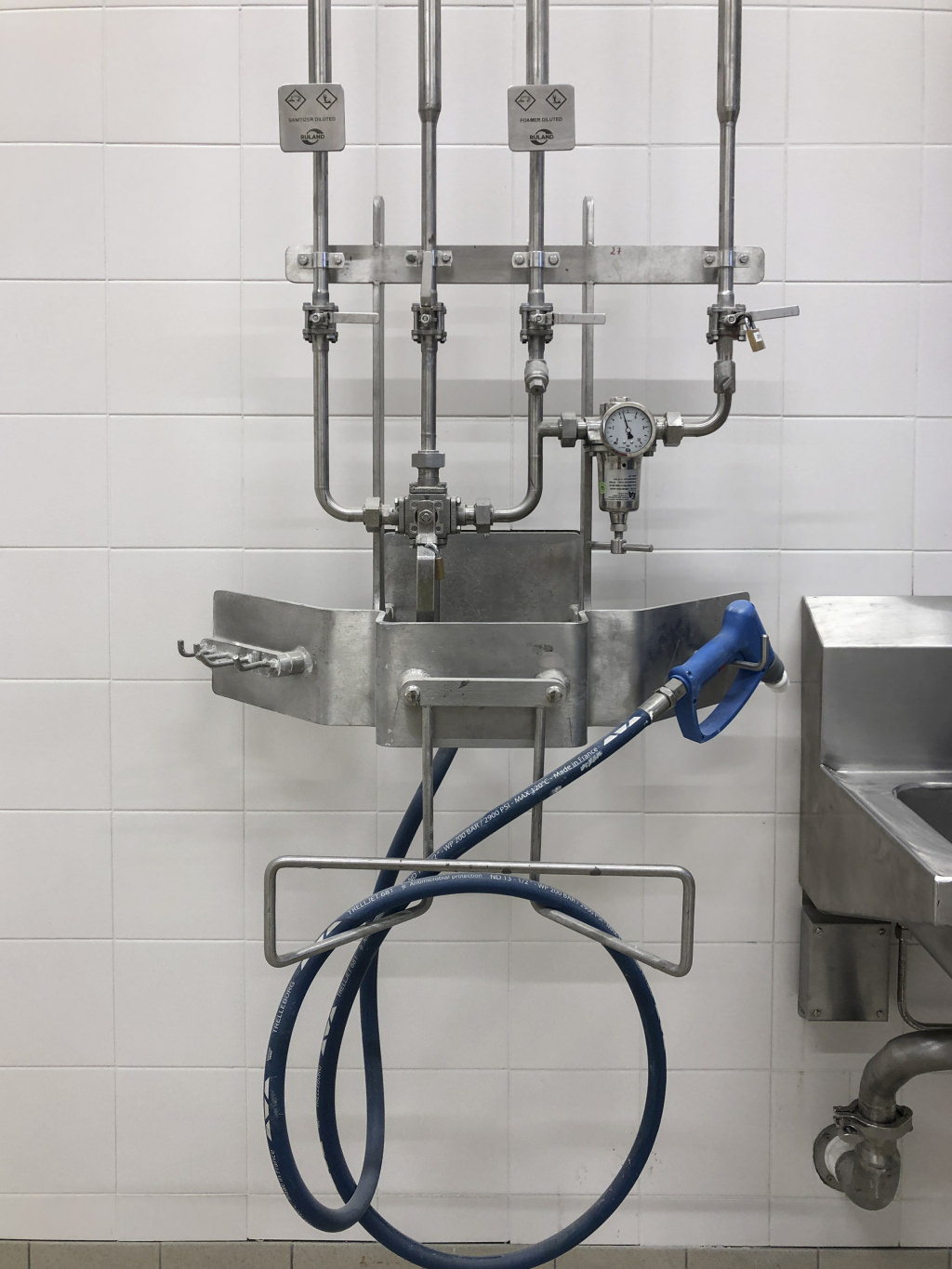
The realisation avoids contamination risks down to the last detail
Hygienic design as special project challenge
Glanbia strictly distinguishes between high- and low care areas in the building design. This displays the everyday production, one employee is only responsible for tasks within one hygienic area. This way it is possible to avoid time-consuming area changes. The main piping is located in a walk-on suspended ceiling above the production area. Sealed pipe openings, coming vertically from the suspended ceiling, are precisely connected to the plant modules such that there are nearly no horizontal routes within the high care area. For all frames in the high care area the team used flat steel profiles as neither for module frames nor at tube gantrys were hollow sections allowed. The electric-pneumatic installation was also very challenging. All cables leading from the low care area to the main cabinets and the on-site boxes are in an enclosed conduit system. The cables and air hoses are only open at the last few meters up to the sensor or device. Obviously, Ruland only used EHEDG-certificated stainless steel cable glands for the in- and outlets up to the closed system.
Country specific requirements result in additional project requirements
The COVID-19 pandemic tightens the occupational safety regulations
It was very important to respect the occupational safety regulations. Each Ruland employee had to complete a safety course for two days before entering the construction site. Additionally, all suppliers had to submit a safety statement for the safe performance regarding their assembly work. For each room it was also necessary to create a risk assessment method statement, describing the work and possible risks in advance as well as appropriate measures to avoid them. Extremely challenging to project delivery was the outbreak of the COVID-19 pandemic, but after a short break, it was possible to continue work at the construction site under strict 14-days-quarantine and with additional online- and on-site-training. The team was only allowed to work with a minimum distance about 2 meters, wearing mouth-nose protection and washing hands every 3 hours. Thanks to these measures, it was possible to continue the work at the construction site and to finish commissioning of the system at the end of the year 2020. After some small supplemental works, the team finished the project in March 2021.
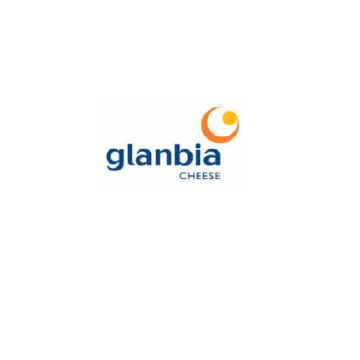
The customer’s feedback
“Delivering this project to our exacting requirements in a challenging timeline necessitated the highest levels of professional competence of all the project vendors.
Ruland Engineering & Consulting GmbH offered exactly the level of expertise and scale of operation to fulfil both the design engineering and process installation requirements of the Project. A shared view of what ‘great’ looks like, an open trusting relationship between both parties and highly skilled personnel made for a rewarding experience; I am happy to recommend Ruland as a company that strives to excel in their field of expertise in meeting the future needs of the food industry.” Conor O’Donovan, Director of Technical Services, Glanbia Cheese Ltd
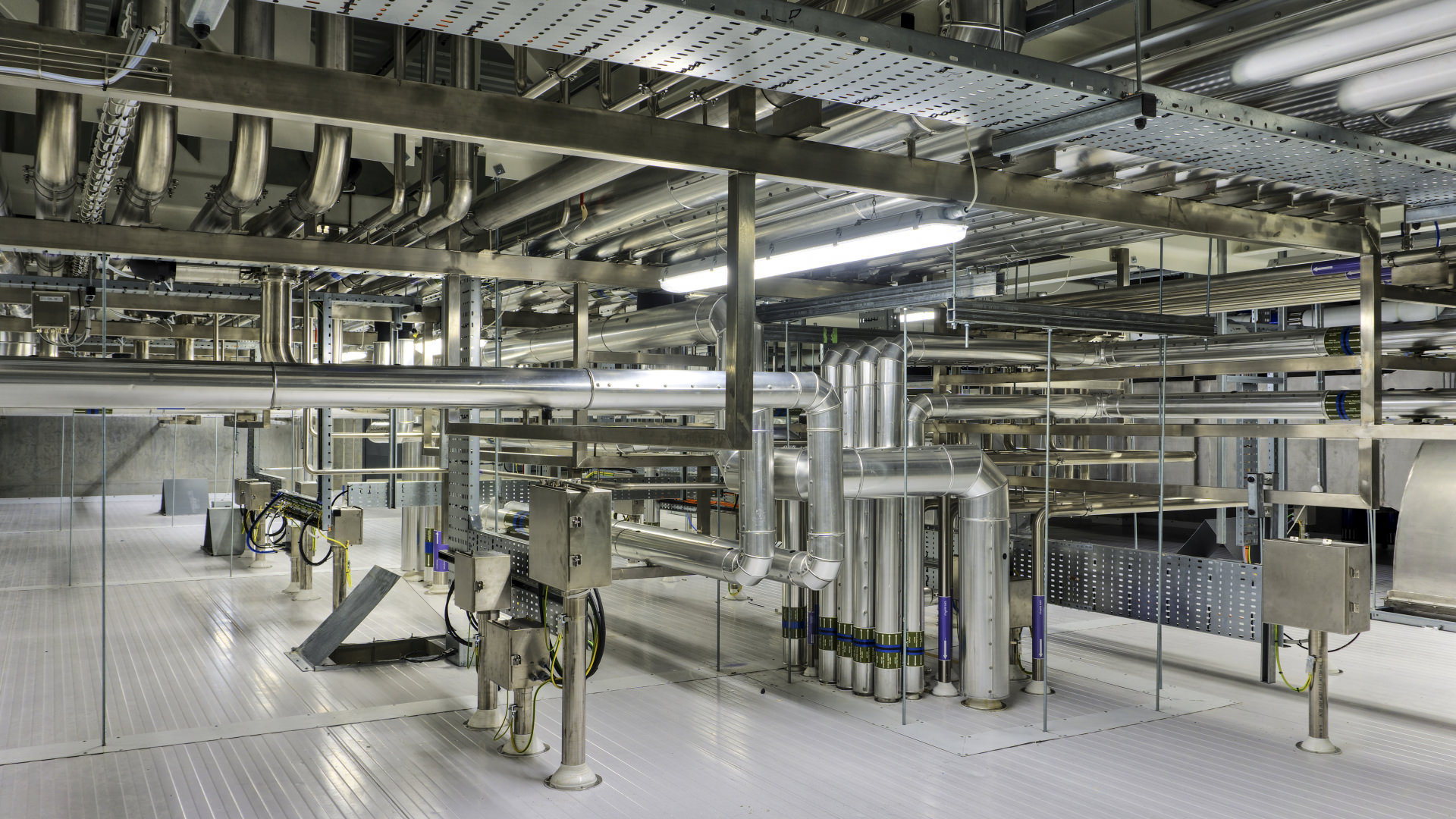
Corporate Hygienic Design
Would you like to know more about our cross-industry engineering and construction experience and our company-wide concepts for Hygienic Design?
We are looking forward to your call and your e-mail!